ARC Advisory Group: Key Technology Trends for 2021
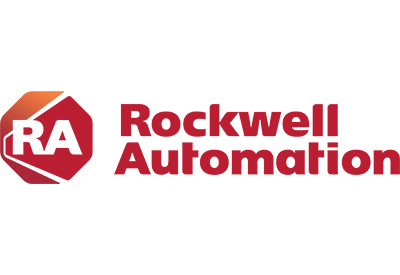
April 28, 2021
By Craig Resnick, Vice President, Consulting, ARC Advisory Group
This year’s “Key Technology Trends” report was strongly influenced by the COVID-19 pandemic, which shifted market demand more abruptly than any single event that we have ever witnessed. This drastically impacted the need for companies to respond fast and become agile, creating both business resilience and opportunities to thrive in this reconnecting world, otherwise known as the new normal. As economies reopened, manufacturers and processors had to deal with the new reality, running their operations remotely with employees working from home. Digital transformation accelerated the ability for physical and organizational boundaries to be broken to engage a real-time workforce, connect teams, and drive collaboration. These companies are under pressure to manage their supply chains to maintain their integrity and flexibility to respond to market demand shifts, doing this from remote locations with the tools to monitor uptime with real-time visibility and control. There are new methodologies required for the new normal, driven by the need to protect against failures, ensure product fulfillment, protect personnel, and all while leveraging enhanced security architectures.
In last year’s Key Technology Trends report, ARC Advisory Group focused on trends which include deploying the next generation of Industrial IoT edge solutions; the increasing use of cyber-physical systems; accelerating the development of open process automation systems and standards; digital transformation shifting focus from basic digitization to full digitalization; and applying systems engineering practices to industrial cybersecurity; all of which are poised to either enter the mainstream or – if already there – to continue to gain acceptance. All relate to the overall digital transformation of industry, infrastructure, and today’s increasingly smart cities and municipalities. For this year, in no order, here are some of the key technologies that ARC Advisory Group believes will increase in importance over the next twelve months or so. While far from a complete list, the technologies discussed in this report will almost certainly make an impact on industry, infrastructure, and municipalities in 2021, building upon the demands created for companies to thrive in the post-pandemic new normal.
Technology Convergence Morphing into Technology Fusion
The convergence of information technology and operations technology (IT/OT convergence) is progressing rapidly as industrial organizations realize it is key for successful digital transformation.
Connectivity and/or convergence between IT and OT is essential for businesses to compete. Manufacturers and other industrial organizations today face the increasing demand for tighter integration and more information. In response, they have started to leverage Industrial IoT and Industry 4.0 technology and approaches including 5G networking, cloud and edge computing, additive manufacturing, advanced analytics, digital twins, augmented reality (AR), virtual reality (VR), artificial intelligence (AI), machine learning (ML), and other emerging technologies.
Increasingly IT/OT convergence includes IT/OT cybersecurity, which helps fill existing security gaps and ensure consistent security levels across the enterprise. Increasingly, convergence also includes the integration of power and automation, which involves converging information about electrical assets (such as in motor control centers) and the production process to help improve sustainability across the entire lifecycle of a manufacturing plant. Convergence between power and automation also provides an integrated, digitalized approach that increases interoperability and flexibility, reduces CAPEX and OPEX expenditures, increases production efficiencies, decreases unscheduled downtime, and improves overall profitability.
Rather than a trend, ARC Advisory Group believes that this convergence between IT and OT, IT cybersecurity and OT cybersecurity, and power and automation will become permanent, representing a true technology fusion. In 2021, look for the introduction of innovative solutions where these technologies will move beyond convergence and be fused into a single offering.
Operational Resilience Becoming a Key Objective
One of the objectives of a company’s digital transformation journey is to ensure resilient operations to improve its capabilities to overcome today’s heightened business risks. These include increasing cybersecurity threats, new regulatory compliance mandates, and more strenuous plant and personnel safety requirements.
Even before the pandemic, manufacturers faced numerous challenges such as market and commodity uncertainty; rapid fluctuations in demand; supply chain disruptions; and the need to become more agile, efficient, and sustainable. However, the current pandemic magnified those challenges, leading manufacturers to focus on operational resilience as a key corporate objective.
To achieve operational resilience, companies must often break down physical and organizational boundaries to more fully engage their workforces , connect teams, and enhance real-time collaboration. Operational resilience also requires supply chains to be managed in real time to maintain their integrity, agility, and flexibility, enabling the supply chains to respond to market demand and shifts in material availability. Companies are deploying new methodologies to protect against unscheduled downtime and asset failures, ensure product fulfillment, protect personnel, and enhance security architectures.
In 2021 and beyond, manufacturers will look to further increase their operational resilience to reduce supply chain vulnerability, lower safety risks, improve remote operational performance, and optimize production throughout the plant lifecycle.
Remote Operations Becoming the New Normal
In recent years, remote operations management was already becoming mainstream in selected sectors such as offshore oil and gas production and offshore wind farms. However, with social distancing mandates (and – in many instances – basic common sense) the pandemic has forced many more companies to shift to running their operations remotely. As a result, many previously on-site employees now work from locations outside of the plant, such as their own homes. This requires a connected workforce with appropriate, cyber-secure tools that provide real-time visibility and control to help meet the challenges of fully remote access to operations.
Ideally, the enabling technology for a connected and remote workforce should facilitate collaboration and reduce paperwork, provide secure access to information to appropriate individuals from anywhere, and support interactions with remote experts. Automation and IT suppliers alike have stepped up to help meet these needs with innovative solutions.
In addition to improving efficiency and providing a safer working environment for employees, these solutions also help companies capture and manage knowledge and incorporate and deploy new workflow processes. Augmented reality (AR), for example, allows the remote user to see any asset in the plant with relevant information digitally overlaid. AR devices (in the form of tablets, smartphones, smart glasses, or “wearable” computers) sense what the remote worker is looking at and display the data needed for the operation at hand.
Rather than a short-term trend, in 2021 and beyond, technology suppliers will continue to enhance their solutions for remote operations and industrial organizations are likely to continue practicing remote operations to varying degrees even after the effects of the pandemic have passed.
Automated Operations Becoming Autonomous Operations
Accelerated by the pandemic, industry urgently requires new modes of operation. Thanks to advances in digitalization, emerging open process automation standards, and IT/OT convergence; manufacturers have an opportunity to move from “automated” to “autonomous” operations for selected unit operations. This frees humans to perform more value-adding tasks and can improve the reliability and predictability of the operating plant. Today, human operators decide what to do when something unpredictable happens. Tomorrow, the autonomous systems may be making those decisions, with the humans serving as observers and overseers.
Autonomous systems supported by artificial intelligence, machine learning, and both historical and real-time data, can also help capture the knowledge of today’s highly experienced operators and technicians, helping mitigate (to a certain extent) the impact of impending retirements of the aging workforce on plant operations and business sustainability. In 2021 and beyond, manufacturers will continue to make inroads toward moving operations from automated to autonomous.
Edge Computing Platforms Becoming Edge Automation Platforms
Edge computing platforms and applications continue to grow rapidly, but these often require support from corporate IT personnel with specialized skills to install, program, operate, and support them. This has led to the development of edge automation platforms designed to provide the full capabilities and benefits of computing at the edge. These capabilities include gathering, analyzing, processing, and storing data locally in real-time at or close to the point that the data is gathered. The key difference is that personnel without specific IT skills will be able support these new edge automation platforms.
Edge automation platforms are critically important because edge computing platforms used in industrial processing and manufacturing applications are typically under the authority of the OT group, the same people who install, program, operate, and service automation equipment, such as programmable logic controllers (PLC), programmable automation controllers (PAC), distributed control systems (DCS), sensors, and other instrumentation. This creates tremendous savings in time and personnel costs. Furthermore, the edge automation platform is designed to run continuously without the need for specialized onsite or remote IT support. Look for new edge automation platforms to be introduced in 2021.
Other Trends to Watch
Other potentially transformative technology trends and approaches that ARC Advisory Group is following right now include, among others, smart vision systems and video analytics; additive manufacturing becoming more mainstream in production environments; the growing deployment of 5G networks in industry, infrastructure, and smart cities; the containerization of apps; and lifecycle management/optimization for connected assets. ARC Advisory Group will continue to research and evaluate these latest technologies and approaches and looks forward to witnessing their impact on the digital transformation of industry, infrastructure, and smart cities, which post-pandemic is more critical than ever for any organization to adopt to not only survive in the new normal, but to thrive long-term in a world where the only certainty is change.