How To Match The Right Robot To The Right Task
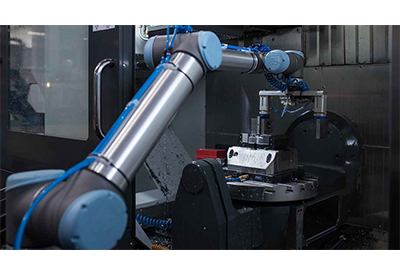
June 8, 2021
By Brad Henrie, Shelley Automation
Like any other industrial machine, robots need to be properly selected for their intended task. If they aren’t they can become a process bottleneck or require more maintenance. Sometimes a needlessly complex and expensive robotic solution is chosen when a simple economically priced one would work instead. Multiple types of robots exist and each excel in different applications while falling short in others. With so many factors to consider how do we select the most optimal robotic solution?
Collaborative Robots
Collaborative robots (cobots) are all the rage right now and they have certainly earned it due to their programming simplicity, human friendliness, and versatility. They are more like shop tools than robots, and have opened up applications that previously weren’t economical. For those unfamiliar with robots this is often the first contact they have with the technology and they can often get short sighted because cobots are so versatile. It’s possible to fit a cobot to almost every task, but it isn’t always the best tool for the task.
The Downside
For faster speeds or higher loads than cobots can handle traditional robot arms can be used. Initially designed for high-speed repetitive work in the automotive industry they are powerful, and fast. Their 6+ degrees of freedom arm design grants them more flexibility than other types of robots but payload capacity decreases the further the arm extends.
SCARA and Delta
When applications don’t require the level of flexibility articulated arms provide there are simpler options like delta and SCARA configurations. They have 3-4 degrees of freedom which constrains the end effector to be parallel to the surface the robot’s mounted on. But this works for applications such as pick and place, soldering, and screw driving. Their simplistic design means that higher speeds and throughput can be achieved which lowers ROI.
Cartesian and Gantry
Drawbacks of all arm designs are low payload capacity and low reach. Cartesian and gantry configurations overcome these limitations because they are constructed from linear slides and can be scaled to match the application. Being composed of linear slides means that they inherit the downsides of linear slides such as poor environmental ratings and take up more space than other robots. They have the largest payload capacity of all robots, but can also be constructed small enough to fit on a desk next to an operator.
So how do we choose a robot?
Shelley is uniquely positioned to answer this question. We carry over 5 different robotics lines and 5 different end effector lines, everything from gantry systems to collaborative robots, and large industrial robots. This diversity allows us to pick the best product for the job rather than just the one that will work. Contrast this with individual suppliers, who must pick a solution from their much smaller lineup. We also provide a complete solution by supplying peripherals such as conveyors, autonomous mobile robots, sensors, and safety systems.
Our sales staff know how to guide you through the process of selecting a robot. They are backed up by our engineering team who have intimate knowledge of all our product lines and know how to combine them into complete solutions.
If a project gets too big for us to handle we can work with engineering integrators who specialize in large projects, many of whom we have partnered with on a regular basis for years.