Food and Beverage Industry: 3 Reasons You Should Invest in Robotics and Automation
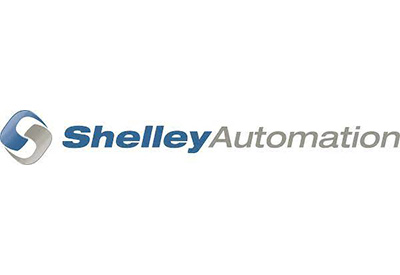
August 19, 2021
By Simab Khan, Marketing Specialist, Shelley Automation
There are many reasons companies in the food and beverage industry choose collaborative robots when they increase the level of automation in their operations.
Here are three factors for you to think about when considering automation in your own facility.
1. Flexibility
Larger companies that process a consistently high volume of each product and that also have lots of space available may choose traditional industrial robots to automate their operations. Industrial robots have the advantage of speed. But they also require more space than a collaborative robot, they’re more expensive, and it’s difficult to change their function once they’re set up.
If your company has a high-mix, low-volume type of production, you’ll need a robot that can easily switch between different products and tasks.
This is when we can introduce collaborative robots.
Cobots have various safety features such as force limiting so that if a person strays into the path of a moving cobot, the force of impact will automatically be limited. Cobots also often operate more slowly than typical industrial robots, so that people in the workspace of the cobot won’t be injured due to high-speed operations. (Or they can be programmed to slow down when a person is near, and speed up when nobody is close by.)
In addition to these safety features, cobots are unlike traditional robots in that they are often designed to interact with people. For example, a cobot arm can be ‘trained’ by an employee (no robotics expert needed) to perform a task. Or a cobot and a human can work together, side-by-side on a specific task. It’s also easy for employs to make changes to cobots so they can perform different tasks.
A wide range of different end-of-arm tools and sensors are available for Universal Robots’ cobot arms. It’s also possible to customize tooling for the processes in your facility.
It’s easy for employees to adjust cobots so they can handle different types of products — from large loaves of bread to tiny, delicate cookies, from squishy bags of milk to cartons of fragile eggs. Because employees can change the end-of-arm tools and re-program the robot themselves, there’s no need for a programming expert to make a change to the robot’s task.
“I wanted a robot that my employees could program for other tasks and place in production by themselves. With our previous robot, we needed to call expensive specialists each time we wanted to make a change. That became too costly.” – Bo Berghdahl, Production and Analysis Manager at Nordic Sugar
Cobots can also help you manage the seasonality of your food and beverage operations. They can work around the clock during busy periods, avoiding the need to hire and train temporary workers. And they can work fewer hours when it’s less busy, without having to lay people off.
2. Quality Control
Using robotics in the food industry makes it easier to achieve the consistency in branded products that customers expect. Unlike humans, robots are able to perform the same task — icing cakes or depositing tomato sauce on pasta — over and over again with less variation than humans (either the same human over time, or different humans across shifts). Not only does this provide the consistency consumers demand, it also reduces waste and the costs associated with it.
Nortura is a Norwegian meat producer and their palletizing robot also helps with quality control. It checks for errors that may have occurred earlier in the production line.
Read the full case study here: Food industry palletizing cobot with vision system works in tight quarters.
Cobot vision systems can be used for reading bar codes or QR codes to facilitate inventory management, sorting, or quality control. The software can give you greater insight into your facility’s productivity. It also helps with traceability in the production line because all steps can be tracked and analyzed.
3. Workplace Safety and Hygiene
Automation in the food industry can reduce the risk of employee injuries due to repetitive motions and heavy lifting of bins, totes, trays, and so on. Cobot arms are available in a range of reach and payload options.
Cobots can work indefinitely in environments that humans find uncomfortable after a short period e.g. humid greenhouses, refrigerated rooms, or tending hot ovens. This may help with hiring and retaining employees in the current labor-shortage environment.
Cobots can also work alone to reduce the risk of contamination in low-touch processes.
The Bottom Line
These are some of the advantages cobots can provide for your food and beverage operations. The payback time for an investment in collaborative robots in the food industry will of course vary based on many factors. For example, payback time was 365 days for Cascina Italia. For Orkla Foods Sverige, payback time was 6 months. For Nordic Sugar payback time was 124 days.