Make Your Work Easier With Well-Designed Human Machine Interface Solutions
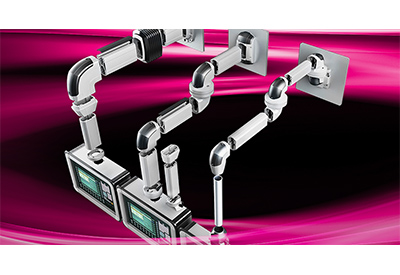
September 7, 2021
A key consideration for plant engineers and operators when choosing the right solution for industrial automation applications, is designing the right Human Machine Interface (HMI) for production programs. HMI includes the equipment and accessories that provides automation system operators with a bird’s eye view of their machines, systems, and processes for optimal manufacturing control and efficiency.
HMI is the engine that allows system operators to drive comprehensive industrial automation setups. With this in mind, let’s briefly examine why a well-designed HMI framework matters and the benefits manufacturers can experience by deploying an HMI system that is designed for today’s manufacturing landscape.
Toughness counts
It’s no secret that much of today’s manufacturing happens in harsh environmental conditions or where automation installations present unique challenges. HMI solutions are often exposed to elements, particularly when it comes to touchscreens and other digital interfaces. This means HMI solutions must be both durable and reliable to combat extreme conditions.
NEMA and IP ratings designate the level of protection for HMI equipment from dust and moisture, while temperature range designations provide guidance on protection from the heat and cold. The most commonly required ratings for HMI solutions are IP65, IP66, and NEMA 12, 4 and 4X, while UL , cUL, and CE Marks are the most common international certifications for HMI solutions.
When considering temperature, it’s important to note a majority of HMI solutions are engineered for ranges between 0℃ to 50℃, though some HMI solutions will allow for deployment in warmer or colder conditions without additional enclosure or climate solutions.
Selecting a HMI solution with the necessary ratings and/or approvals not only helps to ensure a longer service life but also significantly reduces the likelihood of HMI equipment failures.
Industry 4.0 & IIoT
Industry 4.0 and IIoT have made modern manufacturing more connected than ever before. Production processes are no longer isolated or siloed from each other, and each stage of the production cycle feeds the next. The need for end-to-end efficiency and complete control of production programs is paramount, and HMI is a critical component of an automation sequence that helps operators fully understand the performance and condition of machines.
HMI — monitors and other displays — is the primary source of performance and data visualization, which means HMI solutions need to be designed with Industry 4.0 and IIoT in mind to help operators retrieve metrics in real-time and facilitate operational adjustments.
An HMI solution engineered for integration into an Industry 4.0 and IIoT framework will help system operators:
- – Control machine function within the holistic industry network
- – Optimize productivity and reduce the potential for downtime through detailed diagnostics of performance, predictive maintenance, and the capacity for remote monitoring
- – Personalize the user experience via operator preferences and customizations to enhance the end-to-end control capability
Ergonomics at work
Space is at a premium in so many manufacturing contexts, particularly in the material handling space where warehouses and distribution centers are being pushed to the max as e-commerce continues to grow on a massive scale. The physical space occupied by enclosures, climate systems, and other elements of industrial automation systems is now a top priority for facility engineers.
The same considerations are now in place in terms of how machine operators move about a facility floor and how HMI can allow operators to foster the same level of productivity and efficiency with as few movements as possible. The intersection of HMI and ergonomics now means engineers and operators must consider how the design or location of everything from machine handles and shelves to drawers and keyboards can be optimized for ideal operational efficiency.
The value of Rittal’s HMI solutions
In the case of Rittal’s HMI solutions, command panels feature modular and ergonomic design and can be combined with a variety of support arm systems and pedestals for easy integration and reduction of downtime.
Rittal’s HMI consoles and workstations are also equipped with foamed-in polyurethane seals to prevent intrusion from foreign particles, and NEMA-rated carbon steel and stainless steel HMI consoles allow for process automation and the implementation of Industry 4.0 principles while providing durability and contamination prevention. NEMA 4X and IP 55 rated, Rittal stainless steel pushbutton boxes are engineered to protect equipment from dirt, dust, sprayed water, oil, and coolants.
Rittal’s arm support systems are ideal for use in static load ranges from 400 to 1800 N. A variety of configuration and combination possibilities, these arm support systems can be used in almost any application, and the Rittal support arm configurator makes it fast and easy to design a safe, reliable support arm system for your specific needs.
Rittal offers a variety of other HMI solutions and accessories to help companies maximize their investment and operate at peak efficiency. Some of these products include:
- – Handles:Handles on the Comfort-Panel and Optipanel operating housings facilitate optimum ergonomic positioning of the enclosures for different users. Other handle systems may be attached to the straight surfaces of any enclosures.
- – Monitors:TFT monitors in screen sizes from 15″ to 19″, and in some cases monitors can be engineered with a touchscreen interface for maximum efficiency.
- – Signal pillars:Designed to reliably display machine and system statuses using optical and acoustic signals, Rittal’s signal pillars include comprehensive accessories for mounting on different surfaces and support arm systems.
- – External mounting accessories: Engineered with practicality in mind, Rittal external mounting accessories allow operators to clearly display documents or other critical information without disrupting or complicating range of motion movements or manual tasks.
Rittal’s HMI solutions allow manufacturers to have greater control and flexibility with their production programs, but also make it easier for system operators to facilitate an industrial automation framework that promotes efficiency and productivity.
Learn how you can increase your panel building efficiency by 85% with a Rittal Automation Systems solution.
On Labour Day, or any other day of the year, make it easy for your employees and customers by choosing ergonomic Human Machine Interface solutions in your workplace.