Compact Drive Technology Makes High-Tech CT Unit Mobile
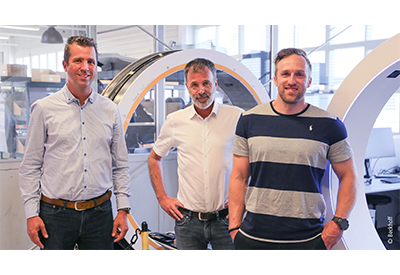
October 21, 2021
Austrian medical technology company medPhoton presented its imaging solution for radiation therapy for the first time back in 2014. This Imaging Ring is now also available in a mobile version, which makes it possible to view the inside of the body on surgical wards before, after and even during an operation. PC- and EtherCAT-based control and drive technology from Beckhoff is used to achieve the desired viewing angles and millimeter-precise alignment of the X-ray source to the patient.
The company medPhoton GmbH was founded by Heinz Deutschmann in 2012 as a spin-off of Paracelsus Medical Private University and the Salzburg State Clinics (SALK). Together with what was initially a small team of medical technicians and software developers, the distinguished physicist pursued the vision of creating a ‘Swiss army knife of diagnostic imaging’ and launching it on the market when he became self-employed. Fast-forward to today and around 35 universally applicable devices like these are now being built every year. “Our imaging ring is a high-resolution computer tomograph that not only provides two- or three-dimensional images, but also enables fluoroscopy with pulsed X-rays. This type of functionality is ideal for tasks such as capturing and digitizing intraoperative anatomical changes,” explains Michael Hubauer-Brenner, executive director operations at medPhoton, describing a solution that can be integrated into a wide variety of treatment processes.
In oncology, the invention from Salzburg plays to its strengths when it comes to visualizing tumors and offering targeted irradiation, while its surgical applications include facilitating 3D guidance for the operating physicians. “Our company background stems from the field of radiation therapy, where our devices are usually mounted on the ceiling or on the treatment table. These environments offer enough space for two to three control cabinets, but the situation is completely different in computer-assisted image-guided surgery,” notes Andreas Schippani, executive director finance at medPhoton, in reference to the usually very cramped conditions in operating rooms. With this in mind, efforts were made to accommodate the entire automation technology in the arms, legs and supports of the latest CT generation Imaging Rings. This design was facilitated by the compactness of the Beckhoff components used and a decentralized system architecture complete with distributed control and drive intelligence.
Flexibility in movement and imaging
The Imaging Ring m/Loop-X mobile imaging robot was developed in close cooperation with Brainlab – a world-leading specialist in software-based medical technology. It measures just 182 x 87 x 189 cm and offers an exceptional range of movement. “It stands on two legs, each of which have two wheels that can rotate independently in different directions. This is what allows it to move forward, backward and twisted, and perform rotations around its own center of gravity or any other point in the room, and even switch from one operating room to another in battery mode – all completely autonomously. All the operator has to do is enter the corresponding navigation commands on the control tablet,” explains Armin Schlattau, head of automation development at medPhoton.
It is also important to note that the robot offers maximum flexibility not only in terms of mobility, but also when it comes to imaging. The radial arrangement of radiation source and detector combined with simultaneous but independent motion offers a host of advantages, which include the ability to achieve a particularly large three-dimensional field of view and the possibility of non-isocentric imaging. “This means that patients do not have to be in the center of the gantry opening during the X-ray, as the system positions the scan region fully automatically in the relevant area,” describes Andreas Schippani. His colleague Armin Schlattau adds, “Although we have a small detector area, we can dynamically generate panoramic images with views from different angles by continuously moving the individual axes at different speeds.” The interaction between the total of 26 axes is orchestrated by a C6015 ultra-compact Industrial PC with an Intel Atom quad-core CPU. Its dimensions of just 82 x 82 x 40 mm mean it requires minimal installation space, making it a perfect fit for the design concept of the imaging robot, according to medPhoton. On the one hand, the IPC coordinates all motion control tasks and, on the other hand, it functions as a TCP/IP server that establishes the connection to the higher-level data processing computer via the TwinCAT ADS Communication library.
Path-controlled 3D X-ray imaging
Using the TwinCAT NC Camming cam function, medPhoton generates laser projections in the form of lines, crosses or rectangles on the patient as an optical positioning aid for all available imaging processes. This function establishes non-linear relationships between master and slave axes. “To calculate a volumetric 3D image from hundreds of 2D projections, we need to know exactly at which point in time and from which angle the individual images were taken. Any errors would have fatal consequences; after all, we are talking about medical interventions here,” stresses Michael Hubauer-Brenner with regard to the importance of the exact, time-stamped signals. “Not only do we depend on precise positional information, but we also measure how long we X-ray from each direction with nanosecond accuracy,” says Armin Schlattau, describing a process that uses equipment such as the EL1252 digital input terminal with XFC timestamp function.
Product diversity from a single source
More than 10 different terminal types from Beckhoff are installed in the imaging robot, including TwinSAFE components such as EL1904 or EL6910, as well as EL7037 stepper motor terminals, and EL7221-9014 servomotor terminals with One Cable Technology (OCT). “When we were looking for a control technology supplier for the mobile version of our Imaging Ring at the Smart Automation trade show in Linz back in May 2017, Beckhoff impressed us right away with its extensive variety of products available in a compact format,” recalls Armin Schlattau. According to the automation development engineer, the main arguments in favor of the automation specialist from Verl included the stepper motor terminal with incremental encoder, the integration of a full-fledged servo drive within an EtherCAT Terminal that measures just 12 mm wide and the bundling of power supply and a digital feedback system into just a single motor connection cable for the AM8121 servomotors.
“While we certainly increased the complexity and performance of our system, we were also able to reduce the space required for the automation technology to a tenth,” says Michael Hubauer-Brenner, delighted with the results of a productive collaboration that has exceeded all expectations to date. But it would seem that the finish line is still quite some way off: “There will certainly be some further developments to our Imaging Rings and we continue to hope for creative input from Beckhoff,” Andreas Schippani concludes. Balázs Bezeczky, head of the Beckhoff sales office in Vienna, responds by putting forward an initial optimization idea of his own: “With our new ELM72xx servomotor terminals in metal housings, it would be possible to get even more compact in terms of drive technology. What’s more, the ELM72xx-9018 model makes it possible to map a comprehensive Safe Motion function package including Safe Limited Speed and Safe Limited Position options.” His invitation to a test run with the two-channel ELM72x2 model has already been accepted.