AutomationDirect: Processor Power and Energy Efficiency
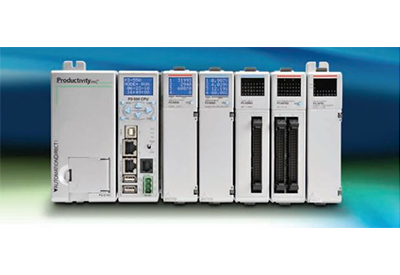
February 22, 2022
By Jason Horine, Product Engineer, Programmable Logic Controllers, AutomationDirect
Think about what your cell phone was like 15 years ago. Most likely, it could be used only for telephone calls—no texting, no photos, no videos and no music. Think about your business trips then with your carry-on bag crammed with a camera, a portable CD player, a travel alarm, maybe a GPS, possibly a tape recorder, a day planner, a calculator and more.
Now fast forward to today—where a smart phone can be used to perform all of these functions—and many more including fast Internet access, golf course distance calculations and many other tasks via imaginative apps.
The same trend of combining what once required separate components into one device is also apparent in industrial automation. Interestingly, the impetus for modern mobile phones to perform many functions with less energy consumption has helped make industrial automation components more powerful, less expensive and more reliable.
An Unlikely Connection
The goal of increasing energy efficiency while augmenting processor power is driven by the consumer electronics market, especially in regards to mobile devices such as cell phones. However, industrial automation equipment isn’t portable, so there’s typically no battery life to consider.
While energy efficiency is vital for consumer electronics, this isn’t necessarily the case in the automation world where the power consumed by the control panel is usually insignificant compared to that of the process being controlled. Moreover, although energy costs are soaring, amortized hardware costs still dwarf energy costs in terms of processors and other automation hardware.
It may therefore seem that the relationship between energy efficiency and processor power has no effect on the industrial automation world. However, the industrial automation customer does benefit from the chip manufacturers’ perpetual goal to create processors that do more while using less energy, a goal that requires cramming a great deal of functionality onto ever fewer chips.
Industrial automation users may not worry about the processor energy requirements, but these new powerful chips offer many advantages to the automation world in terms of price, time-to-market, flexibility and reliability.
More Functionality, Lower Costs
The research and development cycle for new microprocessors used in mobile consumer electronic devices is pushing down the price of processors to the level where automation suppliers can now offer very advanced, multi-function products at low cost.
Demands for increased energy efficiency for mobile phones have prompted chip makers to integrate functions such as memory, Wi-Fi, USB and memory card interfaces onto a single chip. Performing numerous and heretofore disparate functions within a single chip is one of the biggest benefits to come from new component designs.
In the industrial automation world, this means that functionality that used to require a printed circuit board (PCB) with 60 or more chips can now be provided with a single chip. This has enabled design engineers to create new applications in compact form factors that previously would have been impractical because of the PCB area required to house, power and connect all the chips and related components.
We see this trend in PLCs where the integration of more components into microprocessors has eliminated the need for additional external automation components. These components include but aren’t limited to data loggers, ASCII or math co-processors, digital communication cards, proportional–integral–derivative (PID) controllers and more.
Remember when you had to buy a separate Ethernet module, and all the hassle involved with integrating the module with the CPU module? Today, all but the very least expensive PLCs include an Ethernet port, with many featuring multiple Ethernet and other communication ports.
Many of us recall the time when a data logger was an individual entity, with its own mounting rack, power supply, CPU, I/O and memory. High-end PLCs that included data logging were introduced to eliminate the need for separate data logging systems in most applications, and now even inexpensive PLCs often have this feature. In addition to data logging, many PLCs offer database connectivity through the aforementioned communication ports, often supporting a wide variety of networking protocols.
Better Reliability
Consolidating functionality into ever fewer components, primarily the CPU for the PLC, doesn’t just provide more room in the control cabinet. It also creates lower overall costs and power usage for the total system, as well as easier integration and greater reliability. In part, designs with higher integration of functions built into the processor are more reliable. This is because less of the working circuit is exposed to external influence, like electromagnetic interference (EMI), generated by other devices in the area. They also naturally produce less EMI of their own. They’re also less susceptible to surface contaminants, since so many of the connections are sealed within the die of the chip.
The same logic applies to the control cabinets themselves. For example, many former peripheral modules are now incorporated into single products like PLCs. This increases reliability by reducing external connections, while removing the need to integrate disparate components into a working whole. A modern system typically uses fewer power supplies and generates far less heat in the cabinet, further improving long-term reliability and reducing cooling costs
Highly Customizable
The semiconductor industry is releasing new tools all the time that help design engineers satisfy their customers’ needs for smaller footprints, increased reliability, easier programming, faster implementation and more.
How does this translate to the automation world? Many PLC and industrial PC developers are incorporating dual core ARM Cortex-A processor technology, originally designed for smart phones, into their designs. The ARM microprocessor has gained popularity because of its features, peripheral functions, low power draw and flexibility. Field-programmable gate arrays (FPGAs) have significantly benefited from high performance, low energy chip technology developed for the consumer electronic market. “These FPGAs can be installed within a PLC or industrial PC controller and perform tasks such as very high speed control and synchronization, which used to require separate automation components,” explains Robert Oglesby, president of Host Engineering (www.hosteng.com). “By pairing one or more FPGAs with off-the-shelf parts, such as the ARM chip, developers can create highly customizable products at a much lower cost.”
Easily Programmable, More Flexible Design
FPGA chips are not only extremely versatile, they now also come with tools that speed up development and enable changes to be made on the fly. Because FPGAs are reprogrammable, it’s easy to change hard-wired logic without having to buy new ASICs and design new printed circuit boards.
David White, senior design engineer with FACTS Engineering (www.facts-eng.com), describes how his company has been able to create a lower cost, higher performance motion control module using an FPGA-based Digital Signal Controller (DSC).
“The DSC was developed to provide better audio for consumer electronics. While the automation world doesn’t use the DSC for improving audio, it does benefit from its capabilities in motor control, power conversion and sensor processing applications,” says White.
Modern DSCs are highly flexible and very powerful. They can be used to control power supplies, inverters and stepper motors where they provide substantial energy and cost savings while increasing reliability and reducing circuit footprints.
“Because there is so much functionality integrated into the DSC, we’ve been able to create a motion control module at a much lower cost,” adds White. “The DSC handles what once required numerous chips, and modern development tools make configuration easy because it’s done in the software development environment instead of hard-wired,” explains White.
Caveats for the Industrial Automation World
Many industrial automation users are less comfortable with unfamiliar technologies and applications made available from these advancements. The challenge is to provide users with a familiar look and feel, while offering more powerful features for users who need advanced capabilities.
“You need to know how to satisfy the needs of both types of users by respecting the legacy while embracing the new,” says Robert Oglesby, president of Host Engineering. “You want it to give customers something they’re comfortable with, while also providing the maximum price-performance ratio with high reliability.”
Sidebar: Analog module technology comparison
Sometimes a picture really is worth a thousand words. As shown here, two modules, one approximately 10 years old and the other new, depict a huge change in design as a result of the advances in technology driven by the consumer electronics market.
For an accurate evaluation, the two modules shown are a direct apples-to-apples comparison with regard to form, fit, and function. They both supply eight channels of analog inputs to their corresponding PLC system. In the older analog module the components are mostly through-hole, which means they have two or more leads which protrude through the circuit board and are soldered on the back side. The newer module shown below is composed almost exclusively of surface mount components, which means they are soldered directly to the surface of the circuit board.
An important benefit gained from applying the latest consumer electronic technologies is the reduced footprint of the components required to design the module circuitry. The new module greatly reduces the number of components and chips, so a single smaller circuit board can now offer the same functionality that formerly required almost two full-sized circuit boards.
Another benefit is the reduced cost that goes along with smaller size and greater performance. The chart shows the two modules’ offerings along with the corresponding price. Not only does the price drop, but the new module contains extra functionalities that increase the price/performance ratio. The inclusion of configurable software in the new module enables developers to configure the module much easier and faster than in the past. The built-in LCD in the new module provides greater diagnostic capabilities, including display of the raw values in counts, voltage, mA, and more.