HMC Helps Shop Remanufacture Engines to Better-Than-New Condition
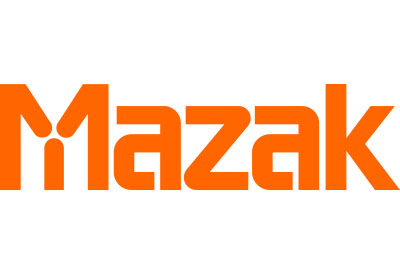
February 22, 2022
When Jasper Engines and Transmissions in Jasper, Indiana, remanufactures a family of engines or transmissions, they ensure their products are of the highest quality, meeting or exceeding OEM specifications. It starts with their New Product Development Division researching popular powertrain products, resolving inherent design issues and figuring out how to improve a product’s longevity. The JASPER process starts with core disassembly, followed by thorough cleaning, precise machining, installation of new, qualified, or improved parts and ending with product-specific testing.
Unfortunately, the time required to align bore camshaft housing bores for specific cylinder heads and meet their production needs proved to be an ongoing challenge for JASPER. That was until they upgraded their align-boring equipment from a manually intensive modified gundrilling machine to an advanced horizontal machining center. The new machine provides the required precision, speed and repeatability and automates their align-boring operations.
JASPER’s Wernsing Road facility, one of four, remanufactures up to 120 gasoline engines per day. During remanufacturing operations, their goal is to qualify as many parts from the original engine as possible. In fact, this is one of JASPER’s primary considerations in deciding whether a particular family of engines is worth remanufacturing. The ability to reclaim core components is key to keeping costs low.
Once an engine is in production/remanufacturing, JASPER will machine its block, heads, crankshaft, camshaft and connecting rods. As these castings are processed, they are checked for cracks, damage, pitting and other signs of wear. When core components are rejected, they are replaced with core parts/castings from the same engine family or replaced with new components. JASPER also offers an authentic engine build where the customer sends in their engine for custom remanufacturing and an optional numbers-matching build.
During overhead cam cylinder head remanufacturing, production first oversizes cylinder head cam bores and either builds up camshaft journals or they use a cam-bearing shell in place of the material removed from the bores. JASPER’s previous align-bore technology was very time consuming and required additional work in process to keep assembly operations fed.
Initially, production used right-angle heads on knee-mill type machines and short tooling that fit between the cam bearing caps. That one-bore-at-a-time method proved unreliable at maintaining concentricity from one bore to the next. This was when production tried a modified gundrilling machine and a 30″ long single-point line boring/reaming tool. The downside was that this process required manually loading the long heavy tools – a strenuous task for operators that eventually damaged the machine’s spindle with excessive wear. On top of that, the process ended up producing more rejects than acceptable ones, so it too was never able to keep up with production needs.
{videobox}PtQ7bo8g_f0{/videobox}
According to Garrett Robinson, CNC Specialist at Jasper Engines and Transmissions, the required long tooling was another key reason for going with a horizontal machining center, and in particular, one from Mazak. Production’s new machine is a Mazak HCN-6800 Horizontal Machining Center with a two-pallet changer and 80-tool storage capacity, but most importantly, its automatic tool changer easily accommodates JASPER’s 30″ long boring tools. Additionally, the machine’s MAZATROL SmoothG CNC, working in tandem with probing macros Robinson developed, significantly reduces the risk of error in part loading and actual machining and frees operators for more value-added tasks within the overall process.
The HCN-6800 isn’t the production group’s first Mazak. Other Mazaks at JASPER include several vertical machining centers – VC-500A/2PC, VC-570C, VCN-530C – and QT 250MSY, QTN 250MSY, and QTU 200 turning/multi-tasking machines. All turning machines are outfitted with bar feeders. JASPER uses these machines to produce components such as clamps and brackets for its remanufacturing departments.
“Prior to the HCN-6800,” said Robinson, “We had to use up to five different processes for oversizing cam bores, and the previous machine lacked the necessary accuracy and speed for the tooling we wanted to use. The HCN-6800 not only allows us to use that tooling but also gives us much better surface finishes and more precise and concentric bores, all at a much faster production level. Also, with this machine, we can bore any of our OHC heads, whether large or small in size.”
Robinson went on to say that having the HCN-6800’s fourth axis table opens up a lot of options, including the ability to run up to four parts at a time on two tombstone fixtures. To further automate OHC head machining, his probing routines remove any operator guesswork regarding fixture positioning and identification.
Running Robinson’s probing routine, the HCN-6800 checks for a part in all or any of the four fixture positions. Once it detects a part, the machine runs another touch probe macro to determine which families of heads are clamped on the tombstone, regardless of whether it’s a Ford 3.5L EcoBoost, Triton 3-Valve or any other late-model engine JASPER produces.
Then, the machine selects the appropriate program for the head type, determines how much stock is in the bore, and compensates for it in terms of machining speeds and feeds. This capability is especially useful because JASPER does not run batches and may have many random variations among the heads it processes on the HCN-6800.
“We need machines that are versatile and can handle OHC heads for multiple engine types along with all their included variations that may be in production at any given time,” said Robinson. “The HCN-6800 allows us to process more parts faster, so our other remanufacturing departments no longer wait for OHC heads.”
Part tolerances and surface finishes are extremely critical to the performance and longevity of a JASPER remanufactured engine. With the rigidity and highly capable MAZATROL SmoothG control of its HCN-6800, JASPER can tune the machine for vibration during the cut, further adding to the machine’s ability to hold consistent tolerances.
“The HCN-6800 is definitely making my job easier in terms of quality control, mainly because of its high accuracy and repeatability,” said Taylor Friend, a Quality Control Captain at Jasper Engines and Transmissions. “Some of the tolerances we have to hold are well below 0.001″, and our previous machines produced a lot of rejected parts. Additionally, the Mazak lets us track our part production.”
Friend went on to say, “Over the years, our tolerances have tightened considerably, leaving us less room for error in our production processes. Specifically in terms of machining operations, particularly maintaining specific part clearances, surface finishes, roundness and general shape requirements. What all this means is that we’ve had to continuously improve our equipment, and Mazak always delivers the speed, reliability and precision we need.”