Embracing the Future of Collaborative Robots
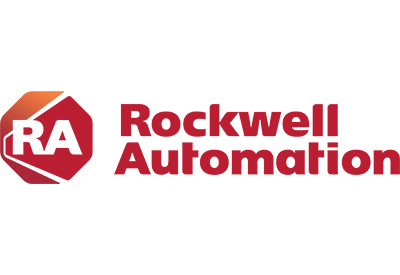
March 21, 2022
By Paul Santi, General Manager, Powertrain Systems Group, FANUC America, and George Schuster, TÜV Functional Safety Expert (FSExp), Business Development Manager, Rockwell Automation
This exciting technology is being enabled by advances in safety technology, including sensors, robots, and cell controllers.
And it’s attracting manufacturers, OEMs and system integrators alike with promises of increased productivity, reliability and cost savings.
For example, FANUC introduced its first-ever force-limited robot: CR-35iA. The robot has a soft outer shell and sophisticated sensing technology. It is designed to work alongside humans collaboratively in a variety of applications and can provide support in areas such as lifting heavy objects, mechanical assembly, palletizing and packing, and material handling.
But before manufacturers and industrial operators can reap the benefits of collaborative robots, they must first understand the safety implications and human impacts of having employees and robots working together on the plant floor.
Standards for Safe Collaboration
In some cases, collaborative robotic applications can reduce the need for safety fencing, which can free up valuable floor space and cut costs for operators. At the same time, they also introduce new safety risks.
The standards ANSI/RIA R15.06-2012 and ISO 10218 outline four approved methods for using collaborative robotics on the plant floor:
- – Safety-rated monitored stop: Safety sensors detect a human’s presence and stop the robot if a worker gets too close.
- – Hand-guiding operation: Operators stop the robot, enter the work cell and then manually control or reposition the robot based on the task at hand.
- – Speed and separation monitoring: Operators and robots work in the same space while maintaining a pre-determined distance between them.
- – Power and force limiting: In this method, if a robot accidentally comes into contact with a human, the robot reduces its force or torque so the human isn’t hurt.
Power and force limiting is an emerging method where the robot may come into contact with a human during its operation. The ISO/TS 15066 standard outlines findings from one study on pain tolerance to help identify just how much force or pressure certain body parts can withstand.
The safety requirements for industrial robots intended for the use in collaborative applications with humans are also incorporated in the new editions of ISO 10218 and as a result, the ISO/TS 15066 standard will be withdrawn as soon as the new editions are published.
A Learning Process
Collaborative robotic applications are changing the way humans and machinery interact, and they represent an exciting future in manufacturing.
But in order to implement these systems effectively and most importantly safely, manufacturers and industrial operators will need to adopt a new set of standards, tools and approaches to analyzing risk.
Additionally, workforce acceptance of closer human-machine collaboration will require increased diligence on the part of system designers and integrators to be sure of the continued safety of all stakeholders.
Learn more about how you can comply with safety standards to reduce the risk of injuries and improve productivity.