AGV and AMR Technology: Solving Your Internal Logistics Challenges
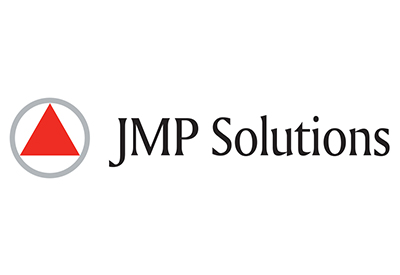
May 17, 2022
Adoption and utilization of automation and robotic technologies continues to proliferate across industries while evolving into use in increasingly complex tasks and processes. In-order-to effectively address these increasingly advanced applications, the implementation of emerging technologies such as Co-bots, Artificial Intelligence, and Autonomous Vehicles is becoming significantly more common. Automated Guided Vehicles (AGV’s) and Autonomous Mobile Robots (AMR’s) are both important pieces in this emerging set of technologies, and they both play or have played critical roles in the emergence and evolution of the use of robotic vehicles in manufacturing, as well as a wide scope of integrated internal logistics and material movement processes.
AGV’s and AMR’s address a number of key manufacturing process and facility-related concerns as well as key cost-related metrics in the migration towards continuous improvement philosophies such as lean manufacturing and six sigma.
Just in time delivery of product to assembly:
As one of the central principles of lean manufacturing, just-in-time (JIT) delivery is a production management philosophy that relies on raw materials arriving at a given stage of production exactly when needed, thereby minimizing all costs related to work-in-progress (WIP). The ultimate goal of this strategy is migrating along a path towards zero waste and maximizing cost efficiency of the combined efforts. When properly integrated into the processes and the existing control infrastructure of a plant, autonomous vehicle missions can be built around JIT schedules in order to maximize the efficiency of raw material inventorying and assembly processes.
Reduced WIP in assembly area:
Unfinished goods, including their associated costs such as labour, that are hung up within any stage of a manufacturing process contributes to work-in-progress cost. Focusing on reducing WIP helps to eliminate production bottlenecks and inefficiencies throughout processes. Reduction of WIP is a key metric that is measured and reflected on both financially and operationally on a consistent basis and throughout virtually every industry. WIP can be significantly reduced through the implementation of AGVs and AMRs by programming pickup and drop-off around a just-in-time strategy while allowing movement of raw materials and components while tasks requiring human interaction are being completed simultaneously.
Flexible assembly line design improvements:
As your processes evolve and progress there is a high degree of flexibility realized as a result of the mobility of mobile robots. Reassigning missions, relocating vehicles, and altering paths are very simple HMI driven procedures that curb the need to move your static facility elements like racking, conveyance, and packaging systems to name a few. Fleet expansion also delivers a simple method of increased capacity through additional vehicles as your business and operations grow and evolve.
Added safety due to less fork traffic:
When effectively integrated into the control infrastructure of a facility, vehicles are given a specific set of process narrative driven “missions” they yield incredibly predictable and safe, rules-based traffic patterns. Utilizing mobile robots does this while, in most cases, if applied properly for material size and payload, are able to eliminate a substantial portion of human driven / directed fork and hand truck traffic throughout a facility. The potential for human error is a common concern and prolific safety risk in any busy facility that is using manned fork and lift apparatus. Autonomous vehicles significantly reduce the safety risk of human traffic error while driving down the overall volume of traffic and waste movements.