Festo Vision Systems – Everything You Need to Know
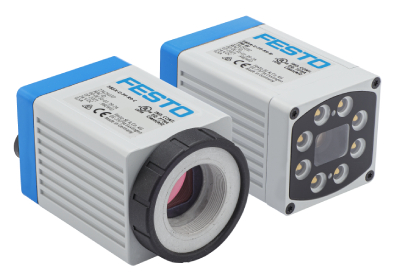
June 21, 2022
By Krystie Johnston
Machine vision systems are used for a multitude of applications. This technology provides image-based automatic inspection and analysis in many industrial applications, more efficiently and accurately than a person. From inspection to identification, barcode reading to robotic guidance, measurement to colour analysis, machine vision systems tackle a wide range of tasks. Festo’s latest generation of SBS vision sensors satisfy the demanding machine vision requirements your application requires.
Panel Builder & Systems Integrator’s sister publication, Mechatronics Canada, had the opportunity to talk with Eric Rice, Product Market Manager – Electric Automation at Festo. In this article, he walks us through some of the latest features of the SBS vision sensors and their common applications. Features like improved resolution, more powerful software tools, easier integration, and greater flexibility, all of which are optimized to meet your machine vision requirements and your application.
What is a vision system and how does it work?
A vision system is a combination of hardware and software that work together to automate visual inspection and analysis tasks. The hardware is specialized in acquiring detailed, digital images and the software is used to analyze those images.
A common example is the detection of liquid fill level in a test tube. The hardware in this case includes the lighting (to illuminate the test tube and liquid), a lens (to focus the light into the camera), an image sensor (to capture the light), and electronic components (to process the resulting digital image). The software in this system is where a computer or microprocessor interprets the digital image data to ensure that the fill level occurs as desired.
There are many use cases for vision systems in industrial and factory automation. Machine vision systems are often used to improve quality, reduce waste, comply with traceability requirements, position robotic grippers, and much more.
Watch this video for an overview of the New Machine Vision Cameras from Festo
{videobox}3M3Qp2BYMNU{/videobox}
What are the features of the SBSA and the SBSX?
There are various types of vision systems available on the market, but all contain some form of the following components: lights, a lens, a high-resolution image sensor, a computer or microprocessor for analyzing digital image data, and a data connection to other automation sub-systems. Vision sensors from Festo are specifically designed to acquire high-resolution 2D images and analyze those images with a broad range of powerful software tools.
The SBSA vision sensor is commonly referred to as a “smart camera” because it includes all the hardware components of a machine vision system in a single device. Illumination of the field of view is provided by eight on-board LEDs in a choice of white, red, or infrared light, while an integrated lens captures that light and focuses it on the embedded image sensor.
An embedded computer resides inside the SBSA, and it runs the software that processes and interprets the digital image data. It also communicates the image data and inspection results over the Ethernet to external controllers or PLCs. To configure the SBSA for the specific machine vision task at hand, the user installs configuration software onto their Windows-based PC and uses that software to configure the SBSA to the specific application requirements.
The SBSX vision sensor is the same “smart camera” as the SBSA but varies in that it does not include the integrated lighting and lens. This gives the user greater flexibility in choosing the best lens for the application. For example, lenses with longer focal lengths or telecentric lenses can be used in place of an integrated light and lens. The SBSX also requires external lighting to be used to illuminate the field of view.
The main advantage of smart cameras like the SBSA and SBSX vision sensors is ease-of-use. Because all (or most) of the system’s components are integrated into a single device, the user spends much less time designing and installing the system into their application. Another advantage is the price. Integrated solutions like the SBSA and SBSX vision sensors will almost always cost less than competitive systems built with all individual components.
What are some examples of applications for vision systems?
Vision systems are commonly used in manufacturing, including automotive, electronics, food & beverage, medical devices, and pharmaceuticals. They are used in logistics and warehousing, life sciences, machining, farming, mining, retail, and much more.
The SBSA and SBSX vision sensors are most often used for industrial machine vision tasks in manufacturing, logistics, and life sciences. Many of the machine vision tasks in these applications require the analysis of 2D images, like verifying the presence of electronic components on printed circuit boards; tracking automotive parts through the assembly process with the use of 2D data matrix codes; verifying the safety and integrity of foodstuffs during the packaging process; adherence to traceability requirements in pharmaceuticals manufacturing using barcode scanning and tracking; and much more.
In one notable application, a major snack food manufacturer needed to ensure the safety and integrity of the snacks being packaged on high-speed bagging lines at all their packaging facilities. To do this through human inspection would have been far too slow and costly, so the manufacturer employed a solution running high-speed barcode scanners and deployed it out to all their facilities. The result was substantial savings in cost and a major reduction in food safety-related liability.
What software is available?
The SBS Vision Sensor software is used to configure the SBSA and SBSX vision sensors. It is available for free from Festo and comprises three main software tools. The first tool is the SBS Calculator, which is a selection tool that assists users in selecting the best vision sensor for their application in terms of lens choice and resolution.
The user enters their dimensional requirements for field of view (area to be seen by the sensor) and working distance (distance from the lens to the part or area being imaged), and the SBS Calculator provides results based on the focal length and image resolution available. Once a vision sensor has been installed into the user’s facility, the Vision Sensor Device Manager is used to find the vision sensor on the Ethernet network and connect to it for configuration. The Device Manager is also used to start simulated sensors for use in evaluating images offline.
The Vision Sensor Configuration Studio is the third software tool and is used for configuring all aspects of the tasks to which a vision sensor will be applied, including the job settings, alignment (tracking) of the part if it moves within the field of view, detector settings for the various detection tools available (e.g. BLOB, caliper, pattern matching, color tools, etc.), and output settings for communicating data and results to external automation systems.
What service is available?
One of the advantages of working on automation projects with Festo is the deep level of sales and support available from a large team of dedicated automation professionals. In the case of machine vision systems, users are supported by a special team of technical people who are focused on machine vision applications.
These technical people are primarily Festo application engineers located throughout the Americas. Most have many years of experience in Festo products and machine vision, and they are ideally suited to assist users in deploying SBSA and SBSX vision sensors into new applications.
Machine vision is used in any application where the detection, inspection, identification, and measurement of parts or features of an object must be carried out accurately, quickly, and repeatedly. Festo has the latest vision systems to meet your needs, and the expert service to support you when you need it.
To learn more, visit www.festo.ca/visionsensors