Eliminating Waste in Panel Building Applications With Push-In Connection Technology
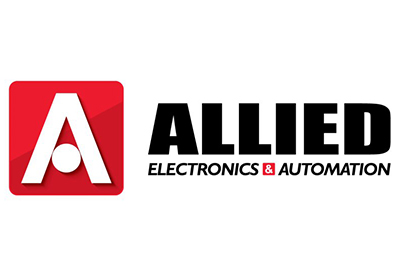
July 20, 2022
By Berea Janzen, Product Marketing Manager – Contactors, ABB
Many manufacturers employ Lean Six Sigma process improvement methods aimed at eliminating waste and reducing variation. In this context, waste is defined by the pneumonic device “DOWNTIME,” which stands for defects, over-production, waiting, non-used talent, transportation, inventory, motion and extra processing.
In the manufacturing industry, the three most common types of waste are:
- – Defects – When a product is declared unfit for use and must be scrapped or reworked, which costs both time and money.
- – Motion – When people move more than is necessary (e.g., to get tools or complete tasks), which wastes time and increases the risk of injury.
- – Extra Processing – When people do more than is required to complete a task.
Efforts to reduce manufacturing waste range from major overhauls that can generate significant savings — up to tens or even hundreds of thousands of dollars — to incremental changes that chip away at waste. But all waste reduction efforts boost manufacturers’ bottom line and, as such, are well worthwhile.
Eliminating Waste in Panel Building Applications
Manufacturing facilities feature many different types of applications with various purposes, processes and end products, but there is some consistent overlap. For instance, every manufacturing facility is equipped with electrical panels. So, panel building applications offer universal opportunities for waste reductions.
One of the easiest ways to reduce waste in panel building applications is to install devices equipped with push-in wire connection technology rather than traditional screw-in wire connection technology. Screw-termination connections require routine maintenance to ensure the safety and efficacy of the wire terminations, while push-in connections allow installers to simply insert wires into an entry hole where they’re terminated and held tight with a robust, high-reliability spring — even in high-vibration applications.
Push-in connections can typically accept solid wires and ferruled wires without any preparation and only require installers to strip a small amount of installation from stranded wires to accommodate insertion. By simplifying the wire termination process, push-in connections enable quicker, easier and higher reliability wire terminations that reduce the risk of installation errors while also reducing installer training requirements and, by virtue of saving time and eliminating the need for routine maintenance, save money. As such, they effectively reduce the three most common types of waste in manufacturing applications: defects, motion and extra processing.
Push-In Connection Pros and Cons
Push-in connections are a proven-robust and -reliable alternative to traditional screw-termination connections and are especially advantageous in panel building applications, which offer manufacturers a universal opportunity to reduce defect, motion and extra processing waste and, in turn, boost their bottom line.
Push-in connections feature clearly identifiable wire entry holes and enable quick, easy and intuitive wire termination, accepting solid and ferruled wires as-is and stranded wires after they’ve been stripped of just a small amount of insulation. This simple termination process can reduce installation time by up to half the time required for screw-termination, eliminates the need for calibrating torque tools and virtually eliminates the risk of wiring errors for even novice installers, which in turn eliminates the need for specialized training and frees up more experienced employees for more complex tasks.
Push-in connection technologies also feature a high-performance spring made of stiff, highly conductive, high-spring-force metals proven to reliably withstand stress relaxation, up to five or more pounds of pull-out force and shock and vibration per IEC 60068-2-27 and IEC 60068-2-6 for the lifetime of the component. In addition, push-in connections don’t require regular maintenance, unlike screw-termination connections, which have to be regularly inspected and retightened to prevent loose wires from causing panel fires or explosions.
The most commonly cited con for push-in connection technology is its cost. But while it’s true that push-in connections tend to cost a bit more than screw-termination connections, devices deployed in harsh-environment, high-vibration applications — like the electrical panels in wind turbines and oil rigs — almost certainly warrant the additional cost and, on balance, may even have a lower applied cost than devices with screw-termination connections that require much more time for installation and maintenance and introduce greater risk to the system.
Calculating the Benefit of Push-In Connections
ABB offers a free savings calculator that allows current and potential customers to quantify the benefit of choosing contactors equipped with push-in connections over those with screw-termination. Users simply enter a few data points about their panel building operations to see how much money they could save each year by specifying push-in panel devices over screw-termination panel devices.
For example, a user who purchases 800 three-pole contactors a year, spends about $400 on torque wrench calibrations and $0.03 per ferrule and reworks approximately 48 devices a year at a $50 per hour labor rate could save $6,011 a year by switching to panel devices equipped with push-in connections.