5 Simple Safety Tips of the Day to Increase Manufacturing Safety
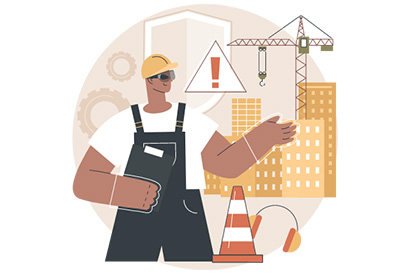
July 25, 2022
In today’s growing supply chain challenges, a heightened sense of awareness of potential hazards on the shop floor is required now more than ever. Everyone wants all their loved ones to return home safe and sound every day, the same way they left.
For manufacturing safety, the little things are the big things. Is your perimeter fence at a proper safe distance from the hazard it is protecting against? Does the safety switch on your gate meet the proper level of safety required for the machine to which it is attached? Are your safety devices functioning properly and well maintained? How can you improve safety in your manufacturing? Sometimes a checklist can help remind your team about some of the simple items that need attention. Here are 5 safety tips for manufacturing to think about this spring:
1. Egress Blockages Removed
Now that spring is here, it is a good time to walk around your facility and ensure that the inside and outside of the exterior doors are not blocked in case of a fire or emergency. Build up of garbage, winter debris, and items requiring storage are the most common hazards at these locations. One of the first manufacturing safety tips of the day is to consider taking a broom along and sweeping the dirt, salt, and garbage away to keep the area as safe as possible. Ontario Fire Code (2.7.1.7.) legally stipulates that the “means of egress shall be maintained in good repair and free of obstructions.” As simple as it sounds, emergency doors seem to be a common place for storage, or for debris to collect, and this is a simple task to complete.
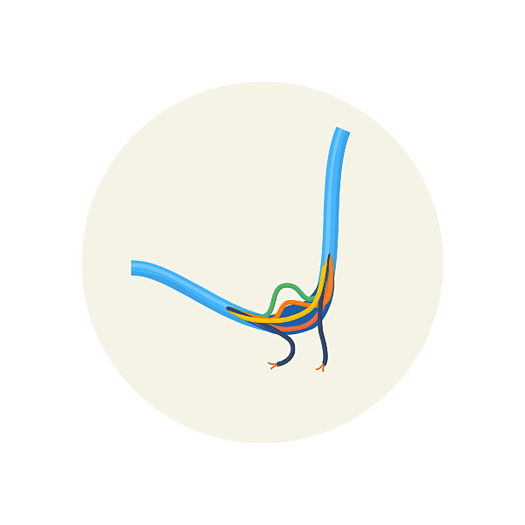
2. Damaged Cables
Rodents may be the main cause of cable deterioration in a manufacturing facility, but any maintenance person will tell you that human and forklift traffic are contributors as well. Cables that have exposed wiring due to fray, tearing, or being cut may not be sending the appropriate power to the machine or safety device. A surge in power can also lead to tripping a breaker, fire, or even worse, injury to a human through shock or electrocution. A detailed walk around a machine can show places where cables are exposed and in need of repair or replacement.
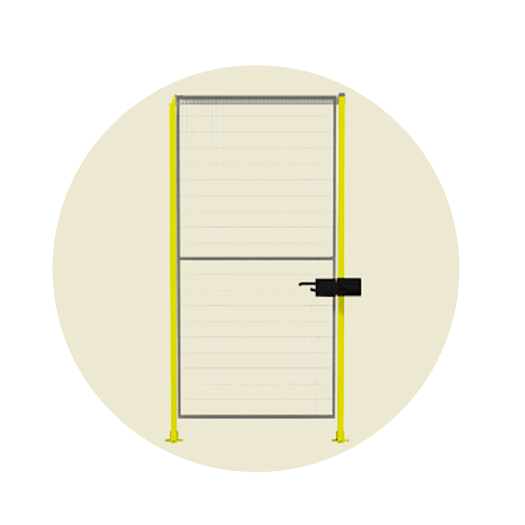
3. Machine Guarding Installed Correctly
Another safety tip of the day has to do with machine guarding. In almost every manufacturing building in which I walk the floor, there is a machine or robotic guarding deficiency based on CSA standards. Panels or guards have been removed for maintenance, posts or panels have been damaged to the point of access, and doors have been tampered with to allow entry without proper protocols. CSA Z432-16 specifically defines safeguarding as “protective measures consisting of the use of specific technical means, called safeguards (guards, protective devices), to protect workers from hazards that cannot be reasonably removed or sufficiently limited by design.” Any significant damage creating reach through access or removal of said guarding without reinstallation before the machine restarts are in violation of the standard. Taking a walk around as a team and looking for deficiencies in the guarding can be a simple and affordable way to boost safety in manufacturing.
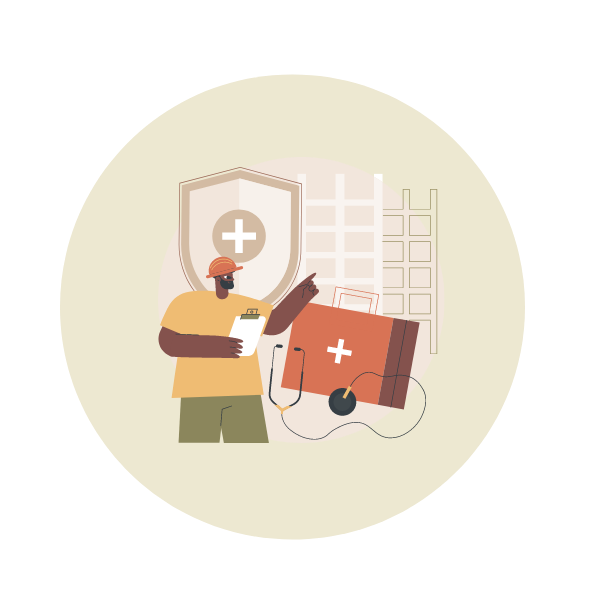
4. Ergonomic Upgrades
As employees return to work, it is important to evaluate the stations at which people are working. Are your desks, work tables, and machines designed to support tall and short personnel? Has your company considered standing desks, adjustable tables, or lifts to assist in making life comfortable and safe for employees to do a full day at your facility? CSA updated this standard (CSAZ412) in 2017 and the preface specifically states that “the objective of this Standard is to apply ergonomics to enhance user health, well-being and to optimize system performance in order to prevent occupational injuries and illnesses or to reduce the severity of harm related to occupational activities in offices.” When is the last time your team reviewed your ergonomic requirements?
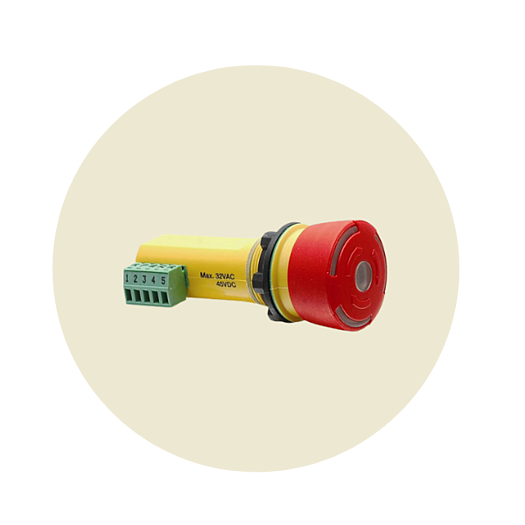
5. E-stops Visible on Control Panels
Another important manufacturing safety tips is to make visible e-stops on control panels. Emergency stops are often considered a crucial part of any safety design for a machine or robot application. Some manufacturers design the emergency stop directly into the safety switch on the door, but more often than not, additional buttons are required around the cell or at the control panel. Omron Automation blogged about E-stops in 2020 on their website where they stated that “at every operator station, there must be an emergency stop ready to be activated whenever necessary. The effects of an E-stop – namely, the ceasing of hazardous machine motion – must be maintained until the device can be manually reset according to ISO 13850-2006. This prevents machinery from starting up prematurely while the situation is being investigated.”
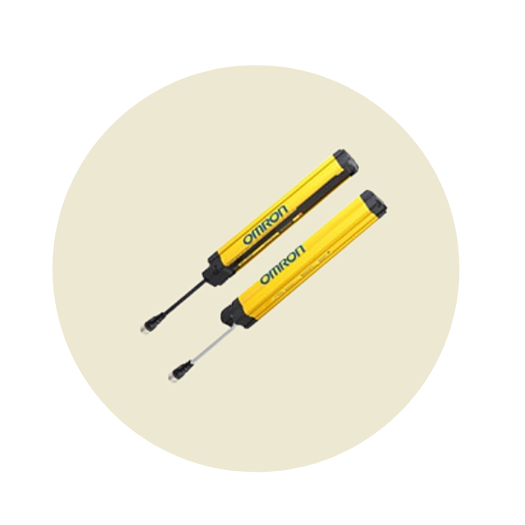
(Bonus) Light curtain check-up
In places where light curtains have been installed to prevent access to a machine, it is imperative to ensure that mounts are checked regularly, and alignment is accurate. Most manufacturers suggest regular maintenance of cleaning and inspection to ensure the product is functioning optimally. Omron has listed in the F3SG manual that the user should “perform daily and 6-month inspections for the F3SG-R as described in Chapter 6 Checklists. Otherwise, the system may fail to work properly, resulting in serious injury.” A one-minute check-up might save a life.