Festo Didactic and SICK Release New Curriculum for Robot Safety Awareness
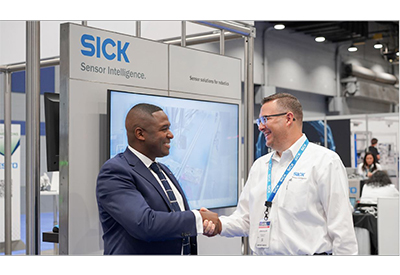
October 4, 2022
Smart Technology is rapidly evolving, especially in the automation and engineering space. This can make it difficult for professionals and aspiring engineers to be adequately prepared throughout their careers.
Festo Didactic developed the program to holistically teach students robot safety. Students can learn the latest industry best practices and become valuable contributors to their employer from the first day on the job.
With safety as the main focus, Festo Didactic and SICK created a Safety Awareness Training Package that combines curriculum and hardware. The content of the curriculum focuses on robot risk assessments as well as the implementation of the system approach vs automation à la carte. The hardware consists of a Festo Didactic manufacturing production system (MPS), a simulated Cyber-Physical Smart Factory with six-axis robot, SICK area scanners, safety PLC and safety relay.
Industry should drive education
“With such a demand for Smart Manufacturing methods to be demystified, students who have been exposed to this sort of implementation have a real advantage when it comes to applying to jobs compared to students not provided the same experiential learning and job training,” said Ted Rozier, Director of Engineering at Festo Didactic North America.
Not only is the curriculum assisting students in understanding the importance of risk assessment, but it’s also helping them understand what to do with the digital data captured. The curriculum walks them through the Six-Step Method of Robotics and Automation equipment safety to understand topics such as:
- 1. Risk assessment
- 2. Safe design
- 3. Technical protective measures
- 4. Administrative measures/information about residual risks
- 5. Overall validation of the machine
- 6. Deployment of machinery
They also learn the definition to terminology, such as performance measures, areas of severity, frequency, and avoidance.
In the past, robotics education has traditionally focused on a specific robot brand and only the robot operation itself. By adding safety curriculum to Festo’s product line MPS (Manufacturing Production System) and Cyber-Physical training equipment, students develop a well-rounded working knowledge of how robots are tightly integrated as a system in the real world. This is also why Festo and SICK designed the curriculum to be robot agnostic, meaning it is adaptable to all leading robot manufacturers.
Festo considers the installed base of robots operating inside production plants in the area near the training institution before selecting the robot brand. This strategy is exercised to ensure that schools purchase the “best of breed” robot – the brand most likely to increase student employability – depending on the location of the education partner. “This approach ensures that students can qualify for jobs locally. Regardless of the robot manufacturer, Festo and SICK have created this content to be agnostic, which means it will align to the best practice of any robot manufacturer, allowing students to become adaptable contributors from day one on the job,” Rozier said.
Working with SICK
For more than seven decades, SICK has led the world in opto-electronic safety solutions for hazardous machines and work areas. With advanced technology taking off at the speed of light what should be included in every robotic training program?
“A thoughtful safety concept!” says Rozier. “SICK has a strong safety portfolio which allowed us to create solutions that we call a virtual 360 degree ‘safety suit jacket’. This makes SICK the ideal partner for this program,” Rozier added.
Beyond the classroom
Although the safety awareness training package is set up in several community colleges and universities across the country, its use is not limited to current students. Incumbent workers may also sign up for the safety awareness course to upskill their robotic knowledge base. After learning and performing the competency-based exercises in the curriculum, students acquire the in-demand skills they need to be successful at work and throughout their career.
Safety: the bottom line
Susan Nangle, Consulting & Digital Solutions Sales at SICK, finds the partnership to be representative of Dr. Erwin Sick’s goals, the founder of SICK. Implementing safety into automation was a driving factor of Dr. Sick’s mission when he started the company in 1946.
“SICK wants to make the world a safer place. It’s about educating students that safety is important. It’s about getting beyond the manufacturing site and taking a step back to those students before they even hit the plant floor, so they recognize the importance of machine safety,” Nangle said.
For more information, visit HERE.