Universal Robots Ships Cobots with Two-Week Lead Time, Enabling Manufacturers to Meet Tax Deduction Deadline
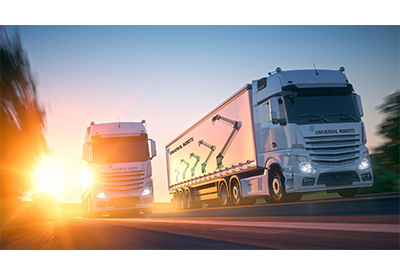
October 11, 2022
Facing unprecedented low unemployment figures, manufacturers of all sizes are struggling to fill repetitive and undesirable manufacturing jobs. With the help of the Section 179 tax deduction, US businesses may be able to significantly stretch their use-it-or-lose-it 2022 budgets and purchase collaborative robots to take on the repetitive manufacturing tasks that workers don’t want. Section 179 requires that qualified equipment and off-the-shelf software is purchased and placed into service by December 31, 2022, but with its unique two-week ship program, Universal Robots (UR) can make that happen.
“Manufacturers simply can’t staff positions to meet their production demands, and many can’t turn to traditional automation, which is too expensive and complex, especially for small and midsized businesses,” says Joe Campbell, senior manager of applications development and strategic marketing at Universal Robots. “UR cobots are cost-effective and easy to implement, and with the Section 179 tax deduction they can be even more affordable. Businesses should consult their tax expert right away to see if they can take advantage of this opportunity, and we’ll do our part to help them meet eligibility requirements.”
Universal Robots successfully navigating supply chain landscape
The strain placed on global supply chains this year continues to make headlines, from semiconductor shortages to labor and equipment availability, all exacerbated by geopolitical uncertainty. Despite these headwinds, Universal Robots has seen significant growth in production while fulfilling its production plan; One cobot is typically comprised of around 600 different parts, sourced from more than 100 separate suppliers.
The 150-person production team at Universal Robots are all involved in getting a cobot made on time, many specifically tasked with overcoming supply chain issues; dual or even triple sourcing parts, including team members travelling to component suppliers to oversee the finalizing and shipping of crucial components. “Collaboration and communication have been key, with the team speaking to primary suppliers on at least a daily basis,” said Vice President for Operations and Supply Chain, Anders Lassen, adding “The emphasis is on keeping everyone aligned to the shared goal – namely, the timely delivery of cobots to our customers.”
For more information, visit HERE.