Control Cabinet Considerations for Industrial Applications
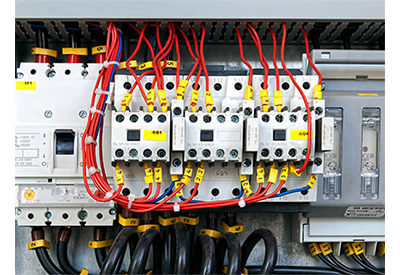
October 12, 2022
By Joe Reed, Product Director – Automation & Control, Allied Electronics & Automation
Power is vital to production, and well-designed control cabinets are key. Today, virtually every industrial application spanning the food & beverage and chemical processing industries to the oil & gas, power generation, product manufacturing, and wastewater treatment industries relies on critical — and often sensitive — powered electronic systems. These systems are vital to productivity, represent considerable investments, and pose serious safety risks, so it’s essential to keep them running safely, reliably, and efficiently. This is where control cabinets come in.
Control cabinets feature a combination of electrical and electronic devices that control the various mechanical functions of connected equipment. Similar to breaker boxes, they feature an enclosure and a back panel. But instead of just containing fuses, they contain components including fuses, contactors, miniature circuit breakers, transformers, terminal block connectors, DIN-rail power supplies, pushbutton switches, motor starters, overloads, grounding, power relays, industrial Ethernet switches, AC drives, PLCs, and HMIs.
Given this vast range of enabling components and a similarly extensive collection of common design, installation, and operating challenges — including enclosure and component sizing, standards compliance, power protection, electromagnetic interference, effectively separating power and control circuitry, low-voltage instrumentation wiring, reliable wire terminations, obtaining accurate voltage measurements, and employee and equipment safety considerations — designing a control cabinet can be daunting. But it doesn’t have to be.
Here I’ll share a few key considerations that will help you design the best control cabinet solutions for your unique application.
Control Panel Standards and Sizes
As is the case with most electrical and electronic products, there are national and international standards that control cabinets are legally bound to comply with. In the U.S., these include requirements mandated by the National Electrical Code (NEC) and the National Fire Protection Agency (NFPA). The NEC and NFPA standards are intended to protect employees, equipment, and facilities from fire and electrical hazards and include minimum requirements for factors such as spacing, wire size, and permitted equipment.
In most industries, it’s also critically important to design for future system expansions from the start, and particularly in terms of physical space. Doing so not only ensures that you’re able to easily and economically upgrade and expand your system as technology and your business evolves; it also helps you maintain compliance with applicable standards as they evolve, which usually happens every three years.
For example, the Underwriters Laboratories (UL) and the International Electrotechnical Commission (IEC) recently harmonized proprietary electrical standards to better account for different voltage ratings, testing requirements, and qualifications across regions and improve support for the increasingly global electronics marketplace. Changes like this overwhelmingly benefit the industry, but they put industrial operations without the space and flexibility to update their control cabinets accordingly in a bind. If you don’t allow adequate space to accommodate future expansions and standards updates early in the design phase, you could find yourself noncompliant or facing a complete redesign and reinstallation down the road, which could be costly as well as detrimental to organizational productivity.
Installation Location
When designing a control cabinet, considering its installation location is just as important as considering its size and ensuring standards compliance. In many industrial applications, controls cabinets are installed in locations with hazardous equipment or environmental hazards, including rain, salt spray, temperature extremes, and high-power washdowns. They can also be placed in areas that aren’t easily accessible for installation and maintenance. But the right enclosure can overcome these challenges.
Once you have a firm understanding of your application environment, you can use enclosure safety ratings as a guide. Every control cabinet enclosure comes with a UL safety rating, most commonly 508A, and/or a National Electrical Manufacturers Association (NEMA) classification. A quick look at these designations will reveal the enclosure’s properties, including indoor/outdoor ratings, hazardous environment ratings, and level of resistance to dust, solid contaminants, water, and potentially even explosions.
For example, NEMA 4 enclosures provide some protection against employee access to hazardous parts and some protection against ingress hazards including solid foreign objects like falling dirt, windblown dust, and water (e.g., rain, sleet, snow, and splashing and hose-directed water). They are also undamaged by external ice, so they are approved for use in both indoor and outdoor applications. NEMA 12 enclosures also provide some protection against employee access to hazardous parts, as well as moderate protection against dust and non-corrosive dripping or condensing liquids, oils, and lubricants, but are best suited for indoor industrial, manufacturing, and machining applications.
Enclosure characteristics can also help overcome the challenges of inconvenient control cabinet locations. For example, enclosures with a continuous hinge enable unparalleled ease of access for installation and maintenance. They are easy to open, achieve a tight seal, don’t warp or sag, and exhibit excellent durability.
Component Costs
One common mistake when designing control cabinets is to conflate component cost with value. However, industrial components, devices, and equipment tend to be priced according to their features. So, in general, higher-cost components are only justified if you have a need for the additional features those parts offer. To ensure that you select the best components at the best price, be sure to go into the specification process with a clear understanding of your application demands and work to acquire the components that meet those needs — no more, no less.
Every feature offered by the control cabinet components you select should be a feature that has real value for your application, ranging from high-value components such as human-machine interfaces to miniature circuit breakers and Ethernet switches and even terminal block connectors and pushbutton switches.
For example, complex, high-cost industrial applications with high-precision sensitivity demands could easily justify the cost of a sophisticated QUINT POWER Series power supply from Phoenix Contact since they’re renowned for providing maximum functionality and superior system availability and are capable of tripping at up to six times the nominal current. But many industrial applications would be better served by a more cost-effective, less multi-functional, but equally reliable power supply like the MEAN WELL’s MDR Series. Striking the right balance between product features and application demands is a delicate, critically important balance that it quite literally pays to invest your time in.
To help simplify this process, several control cabinet products are available with a variety of configurations, characteristics, and price points. Take programmable logic controllers, such as the Siemens SIMATIC S7-1200 Series, for example. These compact, modular PLCs provide extensive versatility, easy installation, seamless scalable functionality, and consistent, efficient performance. As such, they’re smart investments for a wide range of industrial automation applications in the low- to mid-performance range. Their modular construction makes it easy and economical to precisely address immediate needs, like input current, input count, supply voltage, and analog or digital inputs, and expand to accommodate future needs.
Don’t Go It Alone
Selecting control cabinet components and overcoming common design, installation, and operating challenges can be a daunting process, but you don’t have to go it alone.
Allied offers more than 17,000 ready-to-ship control cabinet solutions including PLCs, HMIs, contactors, miniature circuit breakers, terminal block connectors, DIN-rail power supplies, pushbutton switches, motor starters, overloads, power relays, industrial Ethernet switches, and AC drives engineered to keep your operations running safety, reliably, and efficiently.
You likely already know that you can count on Allied to deliver the control cabinet solutions you need from the leading brands you know and trust. But did you know that you can also count on our experienced and agile technical team to help you identify effective solutions to common control cabinet design challenges including the selection and sizing of enclosures and components, standards compliance, power supply selection and protection, electromagnetic interference, separating power and control circuitry, low-voltage instrumentation wiring, reliable wire termination, obtaining accurate voltage measurements, and employee and equipment safety considerations?
Allied offers dedicated key account managers committed to learning the ins and outs of your business, understanding your goals, and providing you with valuable insights into new and proven technologies sure to help you and your business succeed. Our experienced key account managers are ready and willing to assist you from the design phase all the way through to the end of the product lifecycle, providing you with personalized creative input to help you improve build time, maximize productivity, and reduce costs in both the purchasing and maintenance phases.