Case Study: Busbar Solutions Reduce Panel Building Time & Heat Generation for Southpoint Automation (Greenhouse Industry)
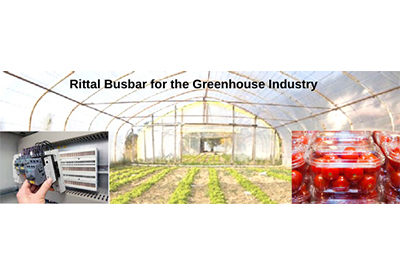
November 17, 2022
Located in Leamington Ontario, Southpoint Automation Inc . is perfectly situated to provide multiple local industries with an elevated level of expertise in a vast magnitude of automation services. Whether a customer requires custom programming services, electrical panel building support, or complete system integration, Southpoint is fully equipped to handle it all.
With experience on various control platforms and backed by an incredibly skilled team of robotic and PLC technicians, Southpoint can handle any job with a level of expertise that meets and exceeds their customers’ expectations. They are fully equipped to handle the design, build, installation, and programming of the latest automated systems.
Southpoint serves multiple industries such as Greenhouse & Agriculture, Automotive & Manufacturing, Warehouse Sorting & Packing, Food & Beverage, Pharmaceuticals, Water Treatment and Oil & Gas, to name a few. Their ultimate objective is to harness automation to reduce costs and increase production, to meet the stringent demands of every customer.
Challenges
Ontario is the home of the growing greenhouse industry, with the Windsor-Essex area in southern Ontario home to more than half of Canada’s greenhouses. Furthermore, it accounts for about 80% of the country’s overall output in greenhouse vegetables, according to Joe Sbrocchi, general manager of the Ontario Greenhouse Vegetable Growers Association. The challenge for automation companies is to find technology that can keep up with the rapid growth of this industry. The greenhouse sector is largely automated, with environments that control heat, water and nutrients as well as lighting. With increasing costs notably for seasonal and permanent employees, greenhouse growers are trying to cut costs to improve margins. The industry is therefore always on the lookout for innovative solutions such as lighting and growing systems that reduce production costs and increase efficiency and yield.
To serve their greenhouse customers better, Southpoint was looking for a high-quality product with reliable delivery times, offering safety, and easier integration with their existing systems. They were experiencing an increasing demand for grow lighting/warehouse lighting enclosures as well as larger motor control systems, and were in search of a solution that could offer optimization of control systems.
Rittal is the leading supplier of reliable power distribution and backup systems for control gear so Southpoint was confident in their expertise. Rittal and their distributor, Proax, offered Southpoint a winning solution that worked within their timelines, and provided them with some unique advantages to stay ahead of the curve.
The Solution
Southpoint was pleased with Rittal’s PLS 800 Busbar system to power up their enclosures for the following reasons:
- – Reduced installation complexity: A combination of IEC and busbar components allows Southpoint’s technicians to complete systems integrations easier and can allow for quick builds across many applications. Production processes can be further streamlined through the kitting of common parts, which increases productivity with the use of a labor force that doesn’t necessarily need to be proficient with elec¬trical equipment, further saving installation costs.
- – Power Distribution in a Confined space: Rittal’s modular RiLine Compact is the tried and tested system solution for compact power distribution in enclosures and small control cabinets. The 4.5 mm pitch pattern available throughout means that no valuable space is wasted on busbar supports.
- – Tool-free assembly made easy: The system is based on a shock hazard-protection board with integrated circuits which are simply top-mounted and secured simultaneously to ensure a secure electrical connection; no tools needed. The contact pitch pattern allows the components to be positioned wherever required.
- – Safe adapters: support fast screw-free connection of cables and devices. and the contact point itself is completely maintenance-free. They satisfy the special requirements of standard IEC 61 439, for safe, space-saving assembly of switchgear and protective gear.
- – Space-saving installation of motor controllers: RiLine Compact motor controllers are used to control motor drives and require 50% less space than conventionally wired motor control units. They are suitable for use with direct and reversing starter combinations. The hybrid technology creates a low-loss motor controller which is particularly gentle on the switching contacts; this in turn helps to extend the service life.
- – Guaranteed global use: Approvals to IEC and UL, and Fire protection corresponding to UL 94 –V0 permits the use of equipment from any manufacturer. End-users benefit from the global market acceptance of IEC components. Likewise, modular busbar systems possess most of the critical certificates necessary for world¬wide installations. The reduced labor costs associated with integration and reduced acquisition costs associated with panel savings can result in a significant cost reduction for the end-user.
All the above advantages make Rittal RiLine Busbar the ideal choice for powering control panel systems at Southpoint. This internationally accepted power distribution technique can be utilized to provide viable and competitive system solutions across a wide spectrum of markets that Southpoint caters to.
Results
“Rittal was able to provide us with an aesthetic and efficient product to satisfy our customers’ demands. It reduced our panel building time to 50% compared to traditional distribution block methods and provided a solution that generates less heat within the enclosure. Moreover, the costing was very competitive, and the products were in stock, so deliveries were quick and reliable!” – Curtis Anderson, Co-Owner, Southpoint Automation
“We are pleased to work with Southpoint Automation to meet the demands of their customers in the greenhouse and other industries. Over and above Rittal’s RiLine PLS 800 Busbar system, Southpoint has been deploying our Wallmounts, Junction Boxes, Hygienic Design enclosures, TS 8 freestanding enclosures, LED lights, HMI, and Fan & Filter Climate Control systems. There has been over a 400% increase in business from 2020 to 2021 which speaks volumes in the trust that Southpoint places with Rittal.” – André Bousette, President, Rittal Systems Ltd., Canada
Looking ahead
Southpoint has future plans to continue to expand the panel building portion of their business, by integrating Rittal’s RiLine Busbar solution wherever possible, from an engineering standpoint. Rittal looks forward to collaborating with Southpoint to come up with innovative and cost-effective solutions to take their business to the next level.
For more Rittal power distribution case studies, click here