Become a More Sustainable Industrial Organization
April 17, 2024
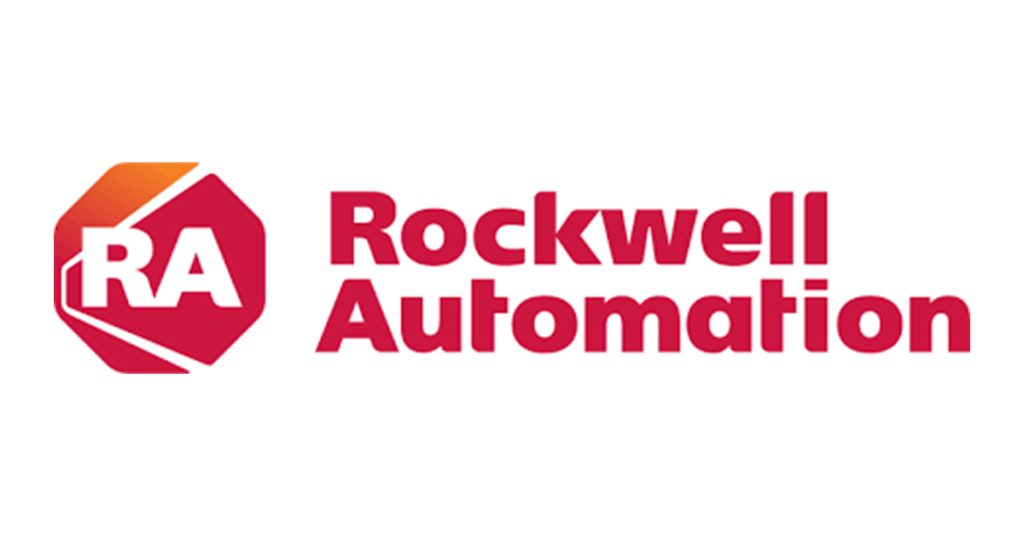
By Giulia Bucci, Sustainability Marketing Manager, Rockwell Automation
4 must-know trends to help industrial organizations become more sustainable in 2024
If you’re looking for ways to become a more sustainable industrial organization this year, 98% of manufacturers are thinking the same thing. They are working towards implementing sustainability systems and solutions in their own organizations.
As you work towards becoming a more sustainable industrial organization, you’re probably preparing for new mandates that regulatory bodies will require. Additionally, you’re preparing for different corporate targets for sustainability performance and profitability.
This blog explains 2024 trends that sustainable industrial organizations need to know, as well as actions you can take to make your practices more sustainable.
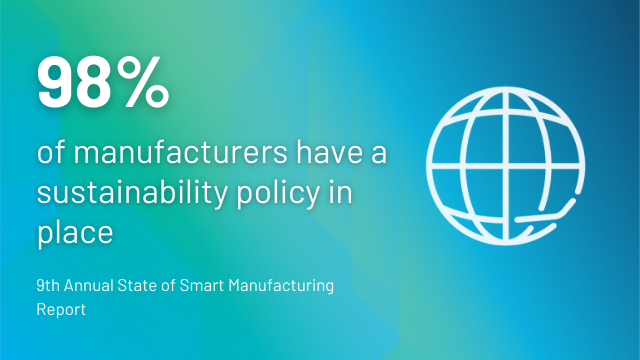
Must-Know Data for Organizations Working Towards Improved Sustainability
Why is it critical for a sustainable industrial organization to take swift action? Because industrial sectors account for nearly 40% of global energy consumption and more than 30% of global greenhouse gas emissions.
Given their impact, industrial companies are facing ESG-related pressure from major stakeholders. Investors are pushing companies to take more aggressive action to meet net-zero goals, while regulatory bodies are mandating changes to ensure sustainability is prioritized.
For example, U.S. public companies are facing dramatic changes in the ESG regulatory landscape. Pending SEC rules are poised to expand climate reporting requirements. The EU has long been the global leader in sustainability regulations and continues to set the standard for what businesses must achieve.
In Asia Pacific, countries are adopting rules and guidelines. And there’s been a surge in the recognition for more transparency in sustainability products, particularly in ESG fund requirements.
Geopolitical tensions are also changing the landscape. The ongoing energy crisis in Europe, for example, creates instability in energy supplies and pricing which impacts both businesses and consumers.
Finally, pressure from customers is growing. More choices are made with sustainability in mind. Consumers expect companies to operate in sustainable ways and to offer sustainably made products. In one study, 32% of consumers reported they paid significantly more for a sustainable product or service.
Key Sustainability Trends: Insights for Industrial Organizations
Trend #1 Emerging technology is indispensable
Emerging technology—AI, robotics, digital twins, IoT, and AR/VR to name a few—is a non-negotiable part of becoming a more sustainable industrial organization.
If you’re not already exploring or using this technology, you will not make meaningful progress on your sustainability goals. Why? Because emerging technology makes manual processes—plant operations, workforce training, and raw materials sourcing—more efficient and more effective in producing high quality output.
Sustainable industrial organizations agree that adopting smart manufacturing practices, which use emerging technology, is extremely or very important. In fact, 85% of them have currently invested or plan to invest in advanced technology such as AI and ML.
Action Item
Initiate a small pilot program around one advanced technology. For example, you could use a digital twin to identify how to optimize operations for a single assembly line. Or you could use an AI tool for one piece of equipment to help you determine opportunities for energy savings. Alternately, you could experiment with AR/VR glasses to train a group of remote workers.
In other words, start small. Applying emerging tech to a targeted initiative will give your team time to learn and gain early wins that can secure wider organizational buy-in. But be sure to increase your use of technology over time. Becoming a sustainable industrial organization requires scaling the automation and digitization of your processes, operations, and more.
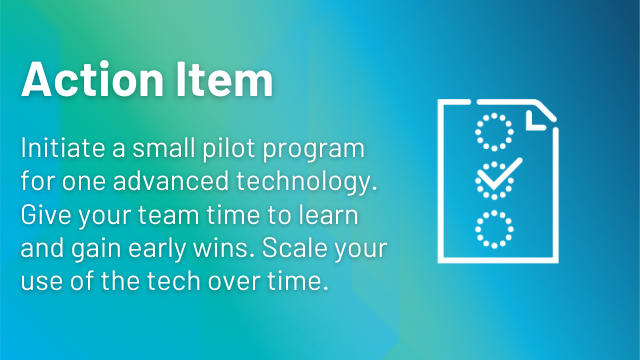
Trend #2 Human workers are still your greatest asset
Labor challenges continue to be one of the top cited struggles facing sustainable industrial organizations. The 9th Annual State of Smart Manufacturing Report found that “respondents plan to use new and emerging technology to amplify their workforce, fill the skills gap and maintain quality against a backdrop of employee turnover.”
Leverage automation to do the repetitive tasks in your facility, and free up your workforce to perform high-impact tasks that require skill. As the report says, “manufacturers have cited a lack of skilled workforce as the top reason they will struggle to outpace the competition.”
As an example, you can assign an AI tool to analyze large datasets faster and more accurately than your workers. That frees up your workers to do the more impactful work of making outcome-driven decisions based on that data.
Plus, the well-being of your workers is critical in advancing your sustainability efforts and improving your Environment Social Governance (ESG) performance.
As a reminder, the Social dimension of ESG criteria encompasses initiatives related to employee well-being, diversity and inclusion, and community engagement. Recent studies found that organizations with strong employee well-being initiatives outperform companies listed on the S&PK 500 index.
How a sustainable industrial organization can invest in their employees
- Developing valuable and ongoing employee education and training programs that upskill and reskill employees who will be doing higher level work as automation processes are implemented to do rote, repetitive tasks.
- Cultivating a diverse, equitable, and inclusive work environment so that employees are empowered to do their best, most productive work.
- Improving the safety of the work environment, which leads to fewer disruptions in operations and lowers healthcare costs for the organization.
In other words, human workers at a sustainable industrial organization are not going anywhere. In fact, they’re key assets to sustainable industrial organizations.
Action Item
Sustainable industrial organizations encourage employees to voice their opinions. Consider developing anonymous surveys, focus groups, online forums, and/or an open-door policy with managers. Enable employees to speak openly and safely about their level of well-being and what the organization could improve.
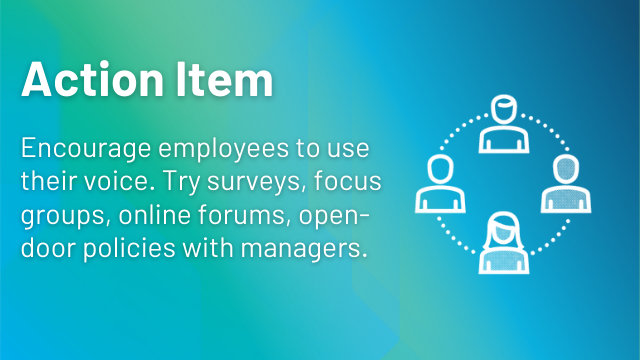
Trend #3 Prepare now for upcoming regulatory changes
Today, manufacturers are not only concerned with their own sustainability but are also working to ensure that their suppliers and partners adhere to similar standards. Under the Securities and Exchange Commission’s (SEC) proposed climate regulations, companies may soon be obligated to report not just their Scope 1 and 2 emissions, but also their Scope 3 emissions.
Sustainability efforts must extend across the supply chain. Moreover, regulatory changes and government incentives have been instrumental in shaping this new mindset. Governments worldwide are enacting stringent environmental regulations and offering financial incentives to companies that embrace sustainable practices. This regulatory landscape has significantly motivated manufacturers to incorporate sustainability into their operations proactively.
This would mark a significant change for many U.S. and international companies, as they have traditionally only been required to disclose their direct and indirect emissions, excluding those from their broader supply chain and other external sources.
Action Item
Act as if you’ll need to report on your Scope 3 emissions sooner rather than later.
Expand your sustainability committee to include your suppliers, product designers, customers, investors, and any other stakeholders who can speak to your organization’s emissions throughout the entire value chain.
Next, consult this resource from the World Economic Forum for a step-by-step process.

Trend #4 Continue to equate sustainable industrial organization practices with productivity
There is no question that improved sustainability leads to improved productivity. The main reason that industrial organizations pursue sustainability is because it will increase efficiencies.
The link between sustainability and productivity is apparent on the world stage, as well. At Davos 2024, much discussion was had about making sustainability more achievable and ROI-focused.
For Cyril Perducat, SVP and Chief Technology Officer at Rockwell Automation, a big takeaway from Davos is that sustainability must be translated into something highly doable and ROI-focused for organizations:
“We need to make sustainability even more practical and actionable so that people understand, ‘If I invest in this way, here are the benefits I’m going to get, the time I need to implement, and the return on investment I’m going to get.’”
In other words, when sustainability efforts are practical, connected directly to ROI, and have a clear timeline, organizations will be more willing to commit.
Watch more of Cyril’s takeaways from Davos 2024 here
Echoing Cyril’s findings is our VP of Sustainability, Tom O’Reilly: “Productivity and sustainability need to be one. And the key to that is the integration of systems leveraging the same data for both productivity and sustainability.”
Action Item
Read first-hand accounts of how other sustainable industrial organizations have achieved improved efficiencies by prioritizing sustainability efforts.
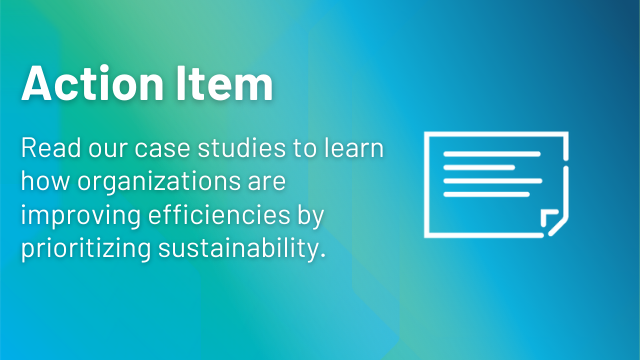