Central Motion Control Facilitates Modularity and Reduces Overall Effort
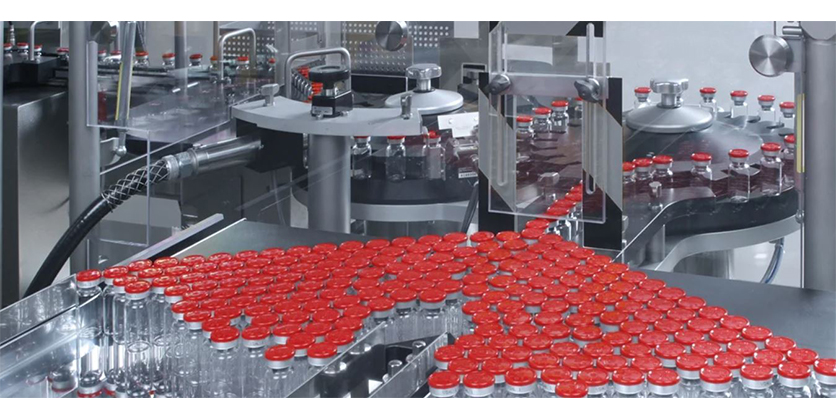
May 11, 2023
For more than 50 years, Bausch+Ströbel SE + Co. KG, headquartered in Ilshofen, Germany, has been developing packaging and production systems for the pharmaceutical and related industries. The company’s goal is to offer the best technical and economical solutions for the challenges of the modern market.
The new ESA1025 labeling machine for various pharmaceutical containers shows exactly how this is implemented with PC-based control from Beckhoff as the central motion controller.
High-quality liquid and powdered pharmaceuticals are filled into syringes, vials, cartridges, and ampoules on Bausch+Ströbel filling and packaging lines worldwide. The process starts with cleaning and sterilizing the objects and extends to labeling and syringe assembly. The ME8081 magazine unit, for example, contributes to the optimization of products and processes by efficiently and accurately storing vials and other essentials. The machine usually forms the end of a filling and packaging line, especially for the high-performance range with correspondingly large output and high process reliability, and can also be combined with testing equipment or object printing.
Modular label dispenser with servo drive technology
Self-adhesive labels on a roll are used for labeling vials and similar pharmaceutical containers. In a bid to ensure these can be applied particularly quickly, accurately, and with process reliability, the ESA1025 labeling machine has now been equipped with a new modular label dispenser. The associated benefits are manifold, including precise and gentle labeling, fast tool-free changeover to other object and label sizes, and even increased print quality through servo drive technology from Beckhoff. At the same time, the system is extremely compact, as the entire electrical system and control components have been integrated into the machine to save space.
The high control technology requirements can be seen in the complexity of the process flow alone:
- Object transport in the system: The vials are transported in via an infeed screw, which is engaged and disengaged on the main star while the system is running – at a reduced speed due to the mass inertia. The main star can have different star pitches (ratios) depending on the object size, which is relevant when coupling with the inlet screw and the electronic cam switch. The outfeed wheels are mechanically coupled to the main star and have no drive of their own.
- Accumulation: This is operated at a constant speed derived from the label dispenser. Good synchronization is required here to avoid wrinkling.
- Labeling: The label dispenser is operated in a cycle – i.e., the gearless label web feed is restarted at full speed every 75 ms. The label web feed is stopped by means of a sensor, which detects the gap between the individual labels. A special logic ensures that correct positioning takes place even in the absence of labels (missing triggers). The servo drive of the label tape feed generates different, highly accurate trigger signals that are required to control the vision and printing systems.
- Options: If required, an additional drive can be integrated to decouple the printing from the labeling process and thus enable a continuously running label web. For all-round vision inspection, it is also possible to ensure that the objects are continually rotated at the same angle at any machine speed by means of a rolling system coupled to the main star via electronic gearing.
Gerald Kreft, programmer in the Software Development/Standardization department at Bausch+Ströbel, explains further special features that are important for transporting pharmaceutical containers: “The ESA1025 labeling machine can also process objects with very thin walls (such as vials) and/or fragile (like ampoules with a crushing ring). It is also essential to ensure that the labeled object shows no signs of cosmetic damage (in terms of the imprint, for example). This is precisely why the through transport has to be as ‘stress-free’ as possible.”
When it comes to labeling, it is essential to support the current trend of moving away from paper-based substrates toward substrates made of plastic with the thinnest possible walls, as Gerald Kreft goes on to note: “Substrates made of plastic are much more unstable, by which I mean more prone to stretching, than their paper counterparts. This trend makes high-speed processing much more difficult. With our new label dispenser, however, the printing can be decoupled from the labeling process via a separate servo drive, which allows us to achieve fast and accurate positioning of the printing even with plastic substrates.”
Benefits of the central control architecture
In the previous model of the ESA1025, the servomotors for the label dispenser and for the through transport were each controlled via separate servo drives. Gerald Kreft explains the optimization potential offered by central motion control implemented with PC-based control as follows, “Separate controls meant having to establish, manage, and maintain several communication paths. There were also several software projects that had to be handled and documented separately. By merging all servo axes into a central TwinCAT controller and achieving a higher degree of standardization, we are able to achieve a lower overall cost here. In addition, PC-based control from Beckhoff makes optimum use of the already limited installation space due to the integrated control cabinet.”
The ESA1025 stands out in particular on account of its super-fast label dispenser, which is capable of handling up to 48,000 units per hour. As Gerald Kreft points out, “The actual maximum output that can be achieved depends on the material being processed, such as the vial size and label length; however, the new dispenser makes it possible to cut right down on the dependence on the label material. The consolidation of all servo drives in a central motion controller was essential for this, and as mentioned, with minimized space requirements.”
Another advantage is the modular design, both in terms of software and hardware. This means that the labeling system can easily be used on other types of machines. It also means that further drives for special solutions could be integrated without much effort if required, in the case of an object transfer to a downstream machine, for example.
The core of the centralized motion control system is formed by a Beckhoff CX2062 Embedded PC with 8-core processor and TwinCAT software as well as the AX8000 multi-axis servo system. The latter features a modular design consisting of an AX8620 power supply module and three AX8206 dual-axis modules, which control the OCT servomotors in the AM8000 series. The range of PC-based control systems used is rounded out by various EtherCAT Terminals and the operating unit, consisting of a CP3918 multi-touch Control Panel and the C6930 control cabinet Industrial PC connected via the CP-Link 4 single-cable solution.