Creating Complex Components Atom by Atom: Ready for Series Production in Electrochemical Machining With PC-Based Control
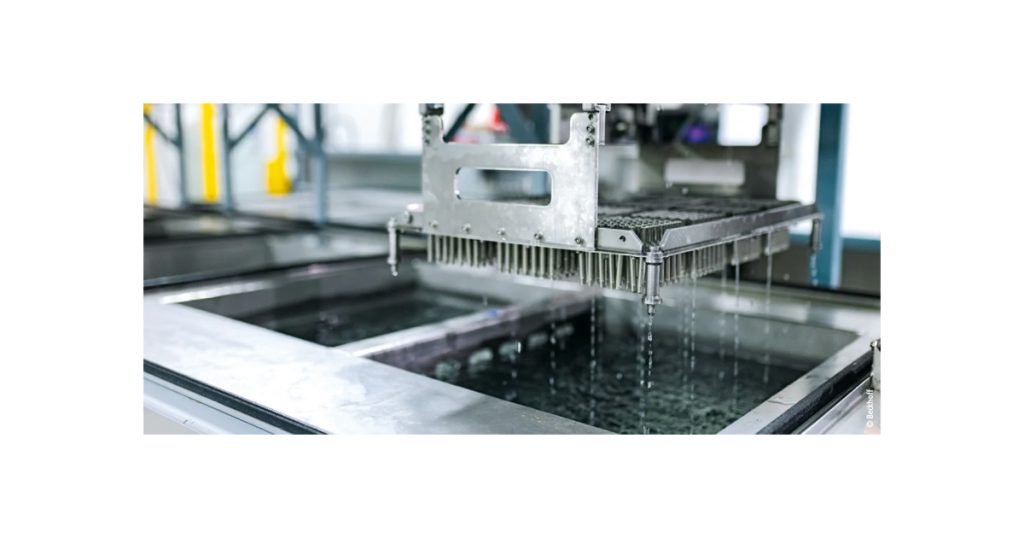
December 11, 2024
PECM (Pulsed Electrochemical Machining) is a fast corrosion process that can form complicated geometries atom by atom. It is therefore ideal for the precise manufacturing of metal parts for high-tech applications. To integrate the core process into a fully automated, high-throughput production line, Voxel Innovations and Palmetto Mechatronics relied on the open PC-based control technology from Beckhoff.
Daniel Herrington, CEO of Voxel Innovations, was working for the U.S. Department of Energy’s Advanced Research Projects Agency–Energy (ARPA–E) when he had a realization. “Manufacturing underpins most major advances in technology, whether it’s in the energy industry, medical device or aerospace. I realized I wanted to work in manufacturing, and I saw that electrochemical machining had significant untapped potential.”
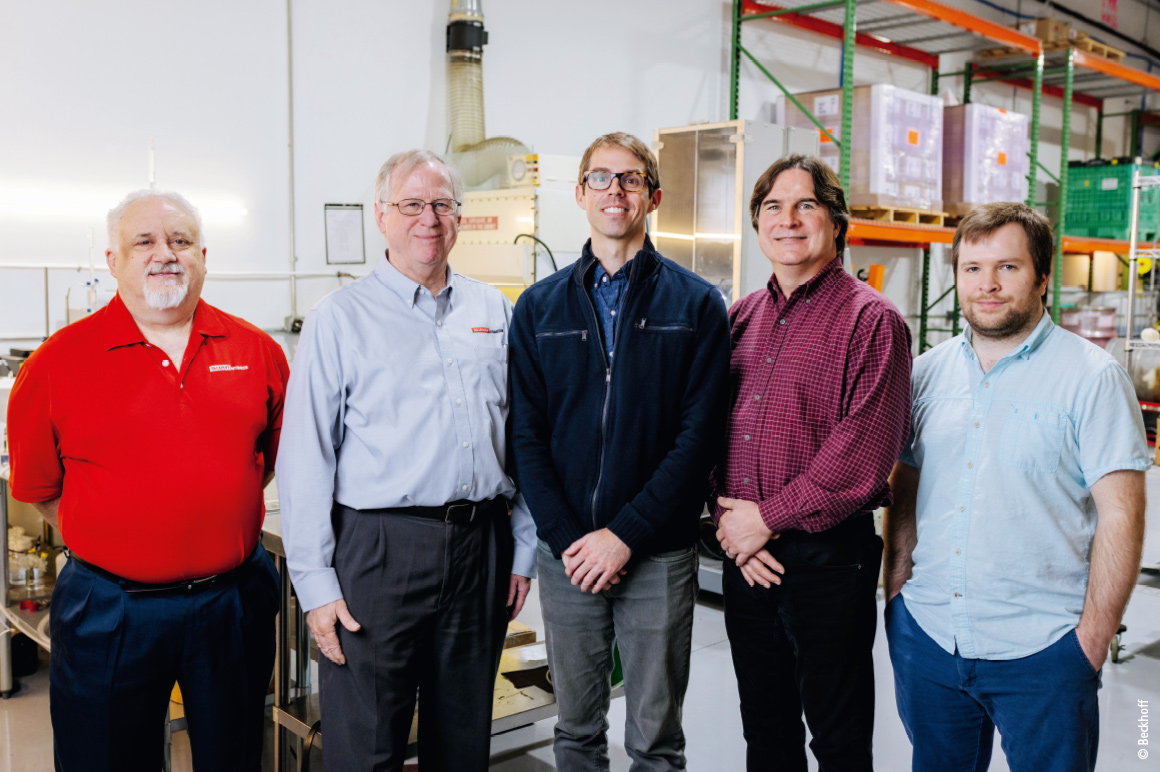
Founded in 2015 in Raleigh, North Carolina, Voxel is now an established provider of pulsed electrochemical machining (PECM). Using machinery developed in-house, the company offers contract manufacturing to support customers across the U.S. These are operating in aerospace, medical device, energy and other industries that need highly engineered, metallic components in large quantities.
One of the first hires at Voxel seems unconventional at first glance. Previously electrochemist Dr. Omar Yepez worked to protect offshore equipment against rust for as long as possible. Now, Daniel Herrington wanted him to do the opposite for Voxel. That’s what PECM is, after all: very fast, highly targeted corrosion that shapes intricate, high-quality geometries atom by atom. “The PECM process is non-contact and non-thermal, so it can create thin-wall geometries with intricate features without deforming the part. With it we can produce parts that traditional manufacturing processes can’t handle as economically or, many times, couldn’t make at all,” Daniel Herrington says.
To continue its growth trajectory, Voxel needed to implement a more sophisticated automation platform for their system that would scale to support increasing production volumes. After extensive vendor research, they selected Beckhoff. This decision also led them to Robert Belk, Jr., Owner and Automation Consultant at Palmetto Mechatronics in Greenville, South Carolina. Working together, the teams at Voxel, Palmetto and Beckhoff developed an automated production line with integrated robotics and inspection capabilities.
Product handling and quality control built in
In the line, the parts are first separated, and then a SCARA robot loads them onto a tray. A gantry moves the tray through pretreatment baths. Next, an articulated robot grabs multiple workpieces and inserts them into the PECM cell. Inside, the tooling lowers into place, and an electrolyte solution fills the minute gap between the tool and the part. By applying the correct voltage potential, the system dissolves metal through electrolysis. Simultaneously, the electrolytic fluid also acts as a flushing agent that removes waste material and any residual heat.
Afterward, the robot unloads the machined parts onto a separate tray. A second gantry then takes them through post-treatment baths and a drying chamber. Finally, another SCARA unloads the trays, while routing parts to an inspection station with Micro Epsilon optical gauges.
The sophisticated operation requires fast cycle times and exact synchronization between different processes. On top of that, interfacing with databases, connecting to web-based platforms to extract data and straightforward integration with third-party devices were all considerations.
Automation software solves tough challenges
Robert Belk worked with Voxel Controls Engineer Kevin Judd to program the machine using Beckhoff TwinCAT 3 automation software. TwinCAT enables engineers to program in whichever language best suits their skillsets and the needs of the application. Belk relied on Structured Text, along with C# for HMI customization.
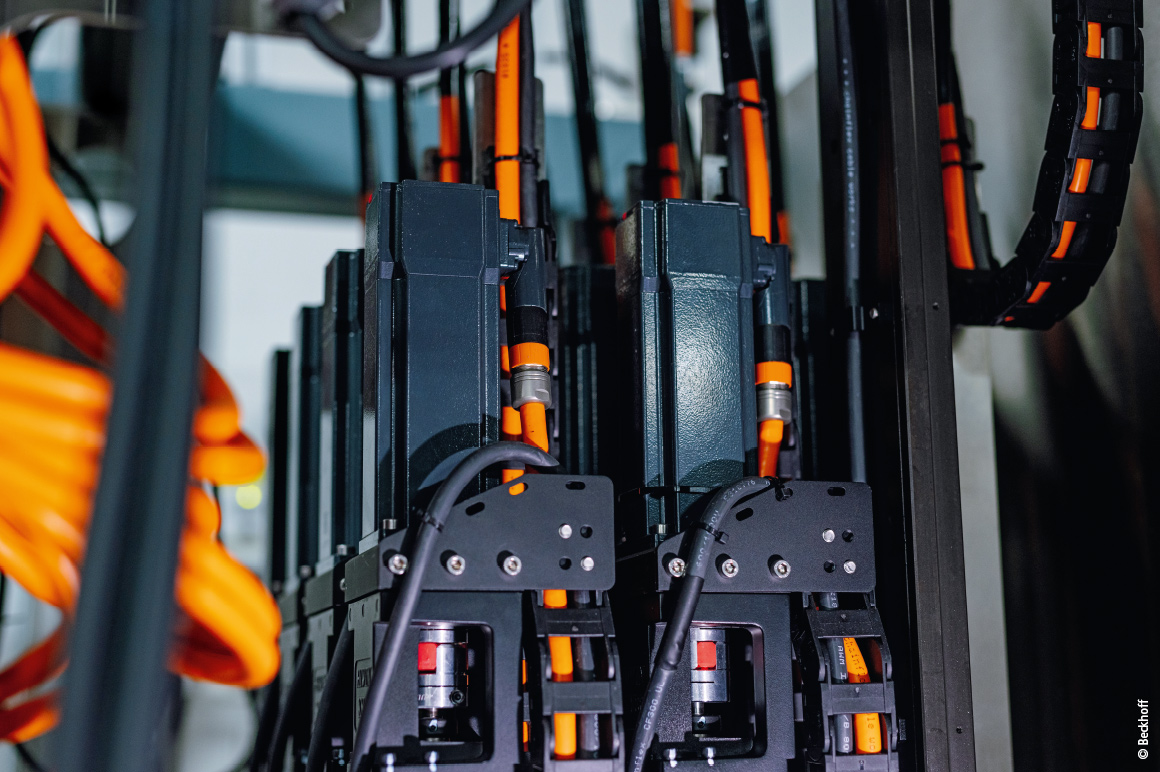
Beyond standard PLC functionality and running PID loops for process sensors, several other TwinCAT functions proved crucial, including:
- ADS communication between the machine logic and a custom Windows .Net application for interfacing with the optical measurement device and HMI
- PTP motion control library, for instance, to drive ball screw actuators with 13 Beckhoff AM8100 servomotors, which raise and lower the PECM tooling
- database connectivity with TwinCAT 3 Database Server for high-speed connection to a custom database for Work-In-Progress (WIP) control and determination of key performance indicators
“This system requires real-time interaction with an MS-SQL database. Each part is assigned a virtual serial number when placed into the first tray, and that is updated throughout each step of the process,” Robert Belk says. “The part data is very important for determining machine tool wear or damage and optimizing the machining process. The Beckhoff database client software enables very fast execution of stored procedures from within the TwinCAT control software.”
Precision control for precision machining
The PECM production line at Voxel uses a CX2042 Embedded PC running TwinCAT as the central machine controller. The CX2042 with directly connected EtherCAT Terminals communicates with the three robots, optical gauges, MS-SQL database and hosts the HMI program. Equipped with Intel® Xeon® multi-core processors, it provides the necessary computing power for short cycle times.
On the networking side, EtherCAT provides fast real-time communication and a flexible topology. EtherCAT Terminals installed on the articulated robot control the end-of-arm tooling with valves and sensors for 24 sets of grippers. Also, EL7211 servomotor terminals provided space-saving 48 V DC servo amplifiers for the AM8100 servomotors. TwinSAFE hardware as well as capabilities built into the robots enable the implementation of functional safety over the EtherCAT network.
Innovative automation for high volume production
After a year of development time, the automated PECM production line went live in June 2023, and is producing roughly four million parts a year. Voxel has hit the performance benchmarks set in the design phase. The system offers complete visibility into quality control data, pH levels, etc., providing traceability to comply with standards like AS9100 in aerospace and ISO 13485 in medical device manufacturing. In addition, it can pause production and alert the operator if anything falls out of tolerance.
“Whether it’s a part for a jet engine, an implantable medical device or a heat exchanger for an energy application, our vision is to offer customers differentiated technologies that help them optimize performance and cost metrics,” Daniel Herrington says. “Then we want to support them all the way through that process and throughout the product life cycle. Our model is to be that trusted engineering development and volume manufacturing partner.” And the demand proves him right: The company continues to run production around the clock in three shifts to keep up with orders.