Consider The OEM Your Machine Tool Service and Support Specialist
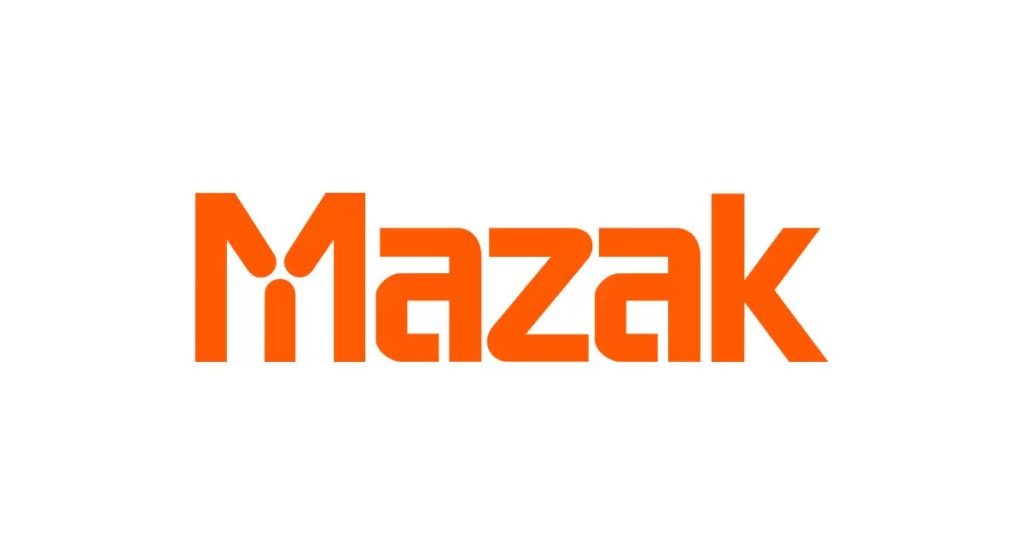
February 28, 2024
Usually, the OEM knows best.
When it comes to service and support from third-party suppliers, the phrase “jack of all trades and master of none” sums up the situation in some instances. While many third-party machine service and repair companies are quite capable, they typically work on a myriad of machine types and brands and aren’t always as well versed on the nuances of a particular model/brand as are the machine’s OEM.
Pairing a machine with a robust service and support package from the OEM can increase the value of that machine significantly – giving shops more for their machine tool investment – and contribute to lowering overall life cycle cost. Unfortunately, many shops miss out on those potential savings and instead opt to have third-party repair companies service machines. Why? The answer given most often is responsiveness. It comes down to how quickly a qualified service technician can address the problem.
There is nothing more detrimental to production operations than a down machine tool, and every second they are out of commission, shops lose money. Time is of the essence in these situations, and shops often believe that only third-party repair companies, as opposed to the machine OEM, can provide the fastest response time and service possible. When in fact, nothing could be further from the truth, especially when it comes to Mazak.
As part of its all-encompassing MPower service and support program, Mazak ensures customers immediate response through its substantially staffed call centers and service technician teams, instant real-time digital accessibility and a network of local Technology and Technical Centers.
For the past couple of years, Mazak has significantly grown its aftermarket service support team as well as restructured its call centers in all of its customer regions. For those call centers, this restructuring included the incorporation of state-of-the-art phone systems. These ensure that all calls receive live responses as opposed to customers having to waste time navigating through an automated phone menu before connecting with a human.
Because having a qualified Mazak technician work on customer machines is paramount, the company maintains a robust staff of Mazak service engineers working in tandem with service engineers from Mazak’s certified distributor network and from other contracted service providers. All are trained through Mazak.
On the digital support side of the MPower program, Mazak further streamlines machine service with its My Mazak service portal and Remote Assist Service. The My Mazak portal allows customers to quickly and easily access account information, open a case, check the availability of the next service technician or resolve the issue over the phone with tech support in real time. When a customer schedules an in-person service call, they can track the status of an existing work order or a service technician’s arrival.
Mazak’s Remote Assist service further shortens the time to repair and reduces the costs associated with in-person field service calls. Once a customer downloads a simple mobile or web app, a technician (located at one of Mazak’s Technology Centers, Technical Centers or at its Florence, Kentucky-based headquarters) can then interact with their connected devices to send specific work instructions and communicate with them just as in a face-to-face service call. This process can eliminate an in-person diagnostic visit before the parts order, saving customers valuable time when a machine is down. In addition to combining diagnostics and part orders into a single virtual visit, Mazak’s Remote Assist offers three-way connections that let service technicians collaborate on solutions with other experts.
For convenient local access to additional service and support, Mazak maintains Eight Technology Centers and five Technical Centers located throughout North America as part of the MPower program. The centers are a place for advanced applications expertise, education and training, new technology demonstrations and special manufacturing events.