Building Factory of the Future with Digital Twins
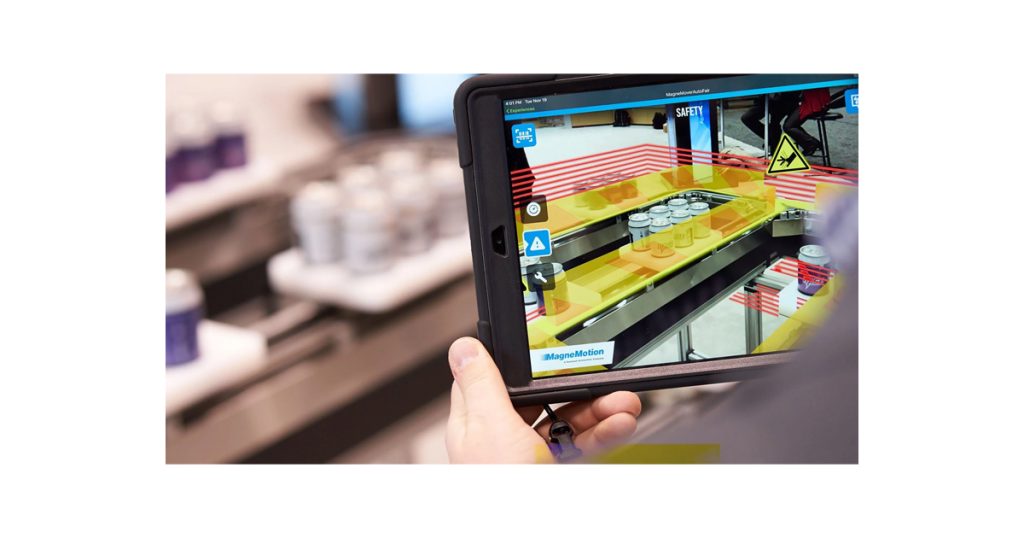
December 11, 2024
By Andrew Ellis, Vice President, Global Portfolio Engineering at Rockwell Automation
Digital twins are a key component of the factory of the future – in fact, they are a key component now. The ability to create a digital model of any process, asset, product, and even facility—regardless of the complexity—transforms how manufacturers design, build, commission, maintain, and decommission all aspects of their operations.
Rockwell Automation and Microsoft are helping manufacturers deploy digital twins to automate and optimize production, create resilient and predictable supply chains, empower the workforce, drive sustainability and ESG initiatives, as well as accelerate business transformation.
Digital twins play a pivotal role in realizing the factory of the future
Digital twins are digital representations of a physical asset or system. They allow users to visualize and analyze all aspects of a manufacturing process. From designing components and writing code to training employees and predicting maintenance, we have seen digital twins become essential components of a smart manufacturing ecosystem. The 9th Annual Rockwell State of Smart Manufacturing Report supports this trend with 95% of participants in the research planning to incorporate smart manufacturing technologies.
Visualize solutions with digital twins
Manufacturers deal with a vast amount of data generated from machines and processes. This is a challenge that we see over and over with customers. The data lacks context and lives in disparate silos.
Digital twins combine and contextualize data across the heterogeneous manufacturing environment to create virtual 3D models that show relationships and hierarchies. They reveal how each piece of the system interacts at micro and macro levels.
Digital twins become the blueprint—the single source of truth—across the manufacturing value chain. They allow users to monitor and analyze real-time and historical data to understand why one production line is more efficient than another one or how a temperature change affects quality. The digital feedback loop unlocks the value of data by providing insights that optimize the entire manufacturing process, improve safety, and reduce commissioning time.
It’s important to remember digital twins do not exist in isolation. Digital twins become super-charged when they leverage a cloud platform like Microsoft Azure. Leveraging cloud scalability allows developers to deliver new functionalities across the enterprise and teams unable to collocate work together in real time.
Mobilize digital twins across the value chain
Rockwell Automation has manufacturing facilities around the globe and has seen firsthand the power of digital twins at different stages of the value chain. Several years ago, the company moved a manufacturing line from Switzerland to Milwaukee. Our findings were:
- Guide early design process. Engineers relied on digital twins for early design decisions. The digital twin allowed the team to design the footprint, operator interactions, equipment needs, potential throughput, and identifiable pinch points. Contributors in Milwaukee and Switzerland could seamlessly collaborate in real time to keep the project continually moving forward.
- Retrofit equipment. To improve equipment operations, a digital twin replicated the actual control system to show the implications of the retrofit prior to starting work. Engineers could test the PLC code to validate connections and interactions. Equipment operators were trained before the system went live and their input used to identify potential operator issues.
- Reduce commissioning times. The twin replicates how a component is designed, installed, tested, operated, and maintained before the component is built, avoiding costly post-construction changes.
- Analyze outputs to spot anomalies. A control system may be reporting one thing, but the digital twin can indicate that there should be a different outcome. It spots inefficiencies and waste before they are solidified into the manufacturing process.
- Guide predictive maintenance. Engineers can model potential causes and timing of equipment failures. They can also model the impact on equipment operators, ensuring a safer working environment. Finally, they can estimate the life of a component and understand how to retire equipment before it is even built.
Learn more about building factories of the future with digital twins
Digital twins are dynamic tools to address technology challenges faced by manufacturers, fostering growth, innovation, and improved operations by providing an enterprise-wide view of data. Rockwell Automation and Microsoft have deep expertise in supporting organizations pursuing the factory of the future technology.