FLIR’s Thermal Camera Technology: A Crucial Component in Industrial Settings
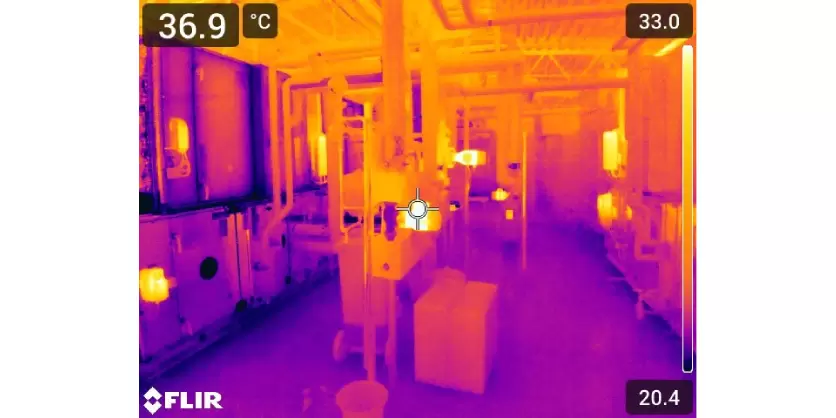
February 28, 2024
By Krystie Johnston
Thermography is an invaluable tool for industrial inspections and building maintenance, new 80° wide angle lens tackles big targets and tight spaces
Thermal imaging technologies like the ones by FLIR improve safety, operational efficiency, and cost savings in many automated and industrial applications. By capturing the infrared radiation emitted by an object or process, it identifies thermal anomalies that warrant further investigation by experts. Today, thermography is more sophisticated and accessible than ever, making is easy for anyone to begin to benefit from this technology. Rob Milner, Business Development Director, FLIR, a Teledyne Technologies company, discusses their latest wide-angle thermal lens and how industries are benefiting from thermal imaging right now.
An overview of thermal imaging
Thermal imaging, or thermography, captures the infrared radiation (otherwise known as thermal energy or heat) that an object emits and, with the help of specialized sensors, converts this heat signature into a thermal image that the human eye is not capable of seeing. This thermal image provides a temperature map of the area being visualized, and highlights hotspots and heat anomalies that warrant further investigation.
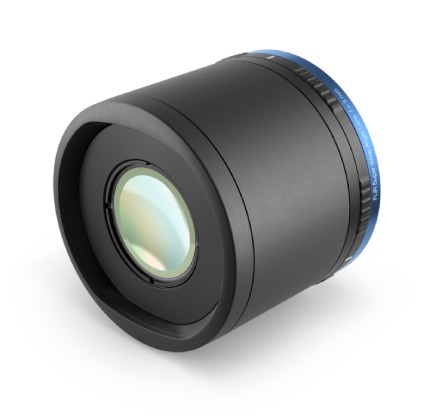
What makes a thermal camera different from a conventional camera used to take photographs? The lens of a thermal camera is most often made of germanium, an element found on the periodic table (Ge). Germanium is transparent to the wavelength band of infrared radiation most thermal cameras use (i.e.,7,500 to 14,000 nanometers). For reference, the visible wavelength spectrum is roughly between 400 to 700 nanometers, so thermal cameras allow people to visualize infrared energy beyond the capabilities of the naked eye.
Not only does a thermal camera require a special lens, but it also uses a unique detector that converts this energy into an image like the way a conventional camera converts light into a photograph. The detector of a thermal camera uses an uncooled thermal sensor known as a ‘microbolometer’. When infrared radiation with wavelengths discussed above strike the detector material, they heat it and change its electrical resistance.
Rob Milner explains, “When you pass a current through the detector element or pixel, and then you hit it with a photon of light, you can change the electrical signal that is passing through that detector pixel. When you do that in bulk, each detector element heats up and cools down, and as a result, it changes the resistance of the electrical signal that is being passed across it, and that is what generates the signal, pixel by pixel.”
Software then translates these signals into an image which represents the temperature variations of the object or process being viewed. Each temperature value is assigned a different colour; warmer areas are typically depicted in red, and cooler areas are typically depicted in blue.
Thermal imaging sees more
Thermal imaging can be used to detect and visualize heat anomalies that could indicate potential issues in a process or object, which can be incredibly useful in many applications. Milner says they are widely used in building inspections and construction sites. Every building inspector, plumber, electrician, roofer, millwright, journey person and skilled trades worker will benefit from having one. Thermal imaging is steadily becoming a widely used tool in many trades – and is a mandatory requirement in some areas.
Milner says that thermal imaging is becoming mandatory in some instances in North America. “Thermal imaging is a requirement in the USA. In industries, they must perform thermography at least on a yearly basis, according to the National Electric Code, NFPA 70B. In Canada, we are not currently requiring thermography across the board.” He does point out some examples where thermography is mandated in Canada. “It is required as part of CSA 28219, which is the standard for emergency electrical power supply for buildings, and the requirement is to do thermography on a yearly basis. It is also required as part of Canada’s National Master Spec.”
Whether mandated or not, thermal imaging improves safety and operational efficiency in many industrial settings and is an effective component of preventative maintenance programs. Identifying thermal anomalies early on allows experts the opportunity to investigate and remedy potential problems before they become safety concerns or catastrophic failures.
Milner gives some examples, “There might be thermal camera looking at a bunch of flare stacks at a petrochemical plant, making sure the flares are lit. There might be [a thermal camera] looking at a refractory line vessel in a steel mill or smelter; that refractory can break down and hot metal can come spewing out of that vessel. A thermal image is effective at indicating if that refractory is breaking down because it will show a hot spot in that area.”
He adds, “Thermal imaging is also used extensively for electrical substation monitoring. There we are most interested in condition monitoring because a breakdown of connections can happen randomly, or perhaps because of a material defect at installation or during repair. Again, we will see that hot spot as it gets worse over time.”
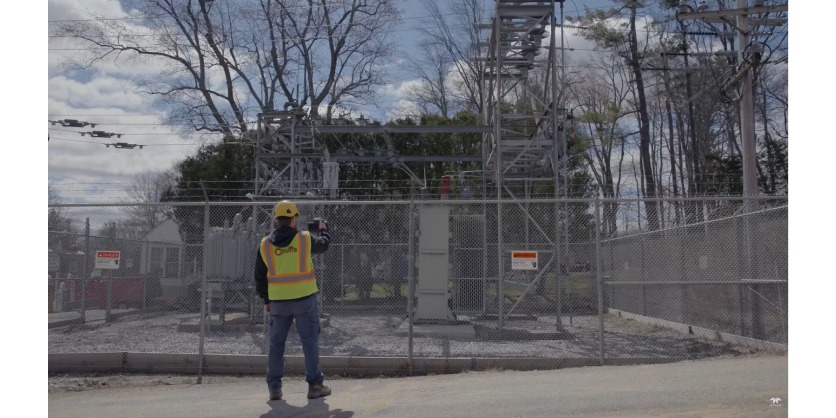
FLIR’s thermal technologies play an invaluable role in preventative maintenance strategies across industries. Whether portable or fixed mount, they have a solution that will provide the best return on investment in any application.
“If you have a particular process that does not degrade quickly, a better return on investment might be to use a portable system and inspect it periodically. On the other hand, if you have something that is extremely critical, dangerous, or has the potential to fail relatively quickly between inspections, you are going to want to have a fixed unit continuously monitor that process or product,” says Milner.
Thermal imaging misconceptions
There are some misconceptions surrounding thermal imaging. One is that thermal imaging is only for intense industrial processes or advanced facilities or defense. The fact is thermography is becoming increasingly attainable for many businesses today. As Milner said earlier, thermal cameras are widely used in building inspections and construction, and any business that uses a lot of power.
Another misconception is that the technology is cost prohibitive. The reality is that thermal imaging technology is available along a spectrum of cost: from cameras that cost several thousands of dollars to ones that are a couple hundred. As Milner says, for a couple hundred dollars, anyone can have a thermal camera and start to make use of it. In fact, FLIR has incorporated thermal imaging technology into devices like multimeters, clamp meters, and moisture meters, making it more accessible than ever.
Perhaps the most common misconception about thermal imaging is that these cameras can see through anything. Popular culture portrays infrared imaging as infinitely akin to X-ray vision processed by superheroes, but this is not the case. “Thermal imaging cameras cannot see through steel. Infrared windows installed on electrical cabinets are specifically constructed with materials that permit thermal wavelengths to pass through, such as geranium and modified calcium fluoride. It is a myth that infrared cameras can see through most things.”
Big targets and tight spaces
One of FLIR’s latest advancements in thermal imaging is their new 80° wide angle lens which almost doubles the horizontal width of the previous 42° lens. A wider-angel lens provides several advantages, the main ones, says Milner, are its ability to view bigger targets or get into tighter spaces.

This new lens is compatible with FLIR cameras that has a certain optical design: this comprises their Exx units, T500 Series, T800 Series, A400 Series, A500 Series, and A700 Series of products. It is not compatible with other cameras because they do not share the same optical block.
Giving some examples of where the new wide-angel lens is beneficial, he says, “In a petrochemical facility, there are a lot of flare stacks located relatively far from one another, and if you want to monitor all of them with a single camera, you need a wide field of view. Similarly, if you are monitoring a steel making ladle in a mill, that is a large object, and although the mill is big, there is only so far back one can go to place a camera, so you need a wide field of view to see the entire target if you are pressed for space.”
Another common application where a wide field of view is used is the tight spaces within electrical cabinets. The components therein are often confined within a small space, making it difficult to view with a narrow field of view.
Milner says, “The conductors, switches, fuses, and other components we need to inspect are typically less than 30 centimeters from the front of the panel. When there is a lot of equipment spread out within that panel, you will not be able to see it all if you have a relatively narrow field of view. The wide angel lens gives us the ability to look through an infrared window into an electrical cabinet and get a nice field of view so that we can see all the components within that cabinet in one image.”
Preventative maintenance and more
Thermal imaging is a key component in industrial settings because it is a valuable tool for preventative maintenance, condition monitoring, and safety. Thermal images allow users to identify thermal anomalies quickly and make it possible to detect problems early. Manufacturers in Canada – and around the world – have electrical rooms containing switch gear, motor control cabinets, power control cabinets, transformers, and other equipment which can degrade over time for a variety of reasons.
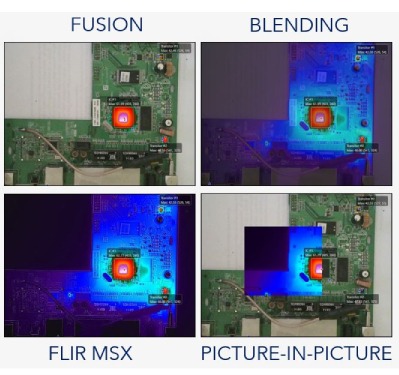
“Thermal cameras are used to inspect this electrical equipment and catch degrading components before they turn into failures and cause interruptions with productivity. It is well known that something as simple as a lighting panel could cause a major disruption to the plant, or even a fire if it arcs, and worker safety issues. This is why we perform thermography.”
Thermography is a critical element to a preventative maintenance strategy designed to keep plants operating productively and safely. Moreover, thermal imaging cameras and their related components such as wide-angel thermal lenses and software, are addressing manufacturing challenges of today such as a shortage of labour and skilled workers, which, in and of itself is affecting the productivity and efficiency of businesses today.
Milner says, “We are finding repeatedly that businesses are struggling to find skilled and experienced trades people – especially thermographers. What we are doing is creating new digital solutions, like routing, data integration, and new products that are revolutionizing the industry because we are creating the ability to have one experienced thermographer support a team, and in many cases, a large team of electricians.”
How to get started
Thermal imaging technology is accessible today. When considering the use of thermography in your operation, the first step Milner suggests is that a company should ensure a reliability leader is trained on thermography. FLIR has an impressive support section on their website that offers support and training. An understanding of thermography will help you tailor your thermal imaging solution to your needs, rather than buying based on an arbitrary budget figure. Software is also an important consideration.
Milner says, “Begin with the outcome in mind. You need to ask questions like, ‘Where is the data going? What are my reporting requirements? What do I need from the software, the connectivity, the data integration?’. You want to make sure you buy equipment that supports your process.”
“It still amazes me, when I talk to companies that use a lot of power that still do not perform thermography because, not only does it pay back in terms of productivity and safety, but their insurance companies probably would give them a break on their premiums if they used it. There is really no reason not to be doing it these days – the technology is really accessible.”
Conclusion
Thermal imaging is an invaluable tool in automated and industrial settings because it can detect overheated components, installation failures, and other problems that may not be visible to the unaided eye. It is a technology that is indispensable for building maintenance and is a vital aspect of any preventative maintenance strategy. Today, thermography is sophisticated and accessible, and it is easy for anyone to get into.