Guide to Synchronous Serial Interface (SSI) in Industrial Applications

April 24, 2024
Synchronous Serial Interface (SSI) technology is a cornerstone in the realm of digital communication, particularly for conveying position and speed feedback from encoders in both rotary and linear forms.
Known for its precision and resilience to noise interference, SSI plays a pivotal role in applications demanding high accuracy, such as in CNC machines and robotic control systems.
This guide aims to explain the workings, advantages, and practical applications of SSI, providing a resource for engineers and professionals aiming to leverage this technology in their systems.
Key Mechanisms of SSI
Serial Data Transmission
At the heart of SSI’s design is its method of serial data transmission, where information is sent sequentially, one bit at a time, along a single data line. This contrasts with parallel transmission, which sends multiple bits simultaneously across several channels. The serial approach has several advantages:
- Simplicity in Wiring: With only one data line required for the transmission of information, the complexity and cost of cabling are significantly reduced. This simplicity also facilitates easier installation and maintenance.
- Reduced Interference: Serial transmission is less susceptible to electromagnetic interference (EMI) compared to parallel transmission. In parallel transmission, the slight differences in cable lengths can lead to timing issues known as skew, which can distort the data. By transmitting data serially, SSI avoids these timing discrepancies, ensuring more reliable data integrity.
- Longer Transmission Distances: The efficiency and reduced susceptibility to noise of serial data transmission allow for longer cable runs without loss of signal quality. This is particularly beneficial in large industrial facilities where encoders might be located far from the control unit.
Clock Signal Synchronization
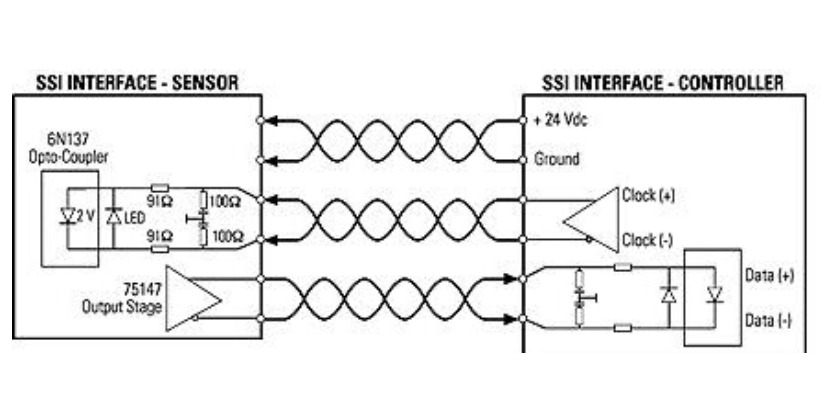
SSI’s reliance on an external clock signal for data transmission is crucial for its accuracy and reliability.
This mechanism involves the controller sending a clock signal to the encoder, which then sends back data synchronized with this clock:
- Precise Timing: The clock signal ensures that the exact timing of data transmission is controlled, with the encoder sending each bit in perfect synchronization with the clock pulses. This precise timing minimizes the risk of data being misinterpreted due to timing errors.
- Enhanced Data Integrity: By aligning the data transmission with the clock pulses provided by the controller, SSI ensures that both the sending and receiving devices operate in lockstep, significantly enhancing the integrity and reliability of the data received.
- Error Minimization: The synchronization with the clock signal also aids in reducing errors due to jitter and electromagnetic interference, as the timing of each bit’s transmission is strictly controlled.
Differential Signaling
Differential signaling is a method employed by SSI to further enhance its immunity to electromagnetic interference, a common challenge in industrial environments. This technique involves transmitting two complementary signals simultaneously:
- Noise Cancellation: Differential signaling sends the data signal and its inverse along two separate lines. At the receiving end, the difference between these two signals is calculated to determine the original signal. Since any interference would affect both lines equally, it can be effectively canceled out when the difference is computed, thereby preserving the integrity of the data.
- Improved Signal Integrity: This method allows SSI to maintain high signal integrity over longer distances and in environments with high levels of electrical noise. It is particularly beneficial in industrial settings where machinery and other electronic devices can generate significant interference.
- Robustness: Differential signaling contributes to the robustness of SSI communications, ensuring reliable data transmission even under adverse conditions. This makes SSI-equipped devices particularly suited for critical applications where precision and reliability are non-negotiable.
These mechanisms combined—serial data transmission, clock signal synchronization, and differential signaling—form the foundation of SSI’s effectiveness as a digital communication protocol, particularly in environments where accuracy, reliability, and resistance to interference are crucial.
Advantages of Synchronized Communication
Enhanced Data Integrity
The hallmark of SSI is its unmatched ability to maintain data integrity, even in the face of potential disruptors like electrical noise and timing discrepancies. This integrity is largely attributable to the protocol’s synchronization between the clock and data signals, a feature that ensures data is transmitted and received as intended:
- Accuracy in Transmission: The synchronization ensures that each bit of data is sent and received in perfect alignment with the clock signal, which means that the exact timing of data capture is controlled, reducing the possibility of errors.
- Resistance to Electrical Noise: In industrial environments, electrical noise is a common challenge that can corrupt data. The synchronized transmission method of SSI effectively minimizes the impact of such noise, as the differential signaling used in conjunction with synchronization makes the system inherently resistant to these disturbances.
- Minimization of Timing Discrepancies: Timing discrepancies between the sending and receiving ends in a data communication system can lead to data corruption. SSI’s synchronized communication guards against this, ensuring that data is accurately captured at the controller end, every time.
Efficient Use of Bandwidth
SSI’s communication protocol is designed to maximize the efficiency of bandwidth use, making it especially beneficial for applications that require the transmission of high-resolution data without delay:
- Serial Data Efficiency: The serial nature of SSI’s data transmission, paired with the synchronization of data to the clock pulses, means that every bit of bandwidth is used effectively. This results in the ability to transmit high volumes of data quickly and accurately, without the overhead and complexity associated with parallel transmission systems.
- Data Transmission: This efficiency ensures that even with limited bandwidth, the system can transmit detailed, high-resolution encoder data. This capability is critical for applications where the precision of movement or position is paramount.
- Reduced Latency: The efficient use of bandwidth also translates to reduced latency in data transmission, an essential factor for systems that rely on timely data updates for optimal performance.
Real-time Feedback
The capability of SSI to provide real-time feedback is a critical advantage in many industrial applications. The synchronized nature of its communication ensures timely and accurate data on position and speed, enabling immediate adjustments and responses:
- Immediate System Response: In automated manufacturing processes or robotic operations, the ability to receive immediate feedback on the position and speed of components allows for dynamic adjustments, ensuring precision and reducing the likelihood of errors or inefficiencies.
- Enhanced System Dynamics: Real-time feedback is essential for systems that operate at high speeds or require instant reaction to changing conditions. SSI ensures that feedback is not only timely but accurate, enabling systems to achieve superior performance and reliability.
- Critical for Process Control: Many industrial processes depend on precise control over movement, where even minor discrepancies can lead to significant issues. The real-time feedback provided by SSI enables precise control, ensuring that processes operate smoothly and efficiently.
Together, these advantages underscore why SSI is a preferred choice for industrial communication, particularly in applications where precision, reliability, and efficiency are non-negotiable. By ensuring enhanced data integrity, efficient use of bandwidth, and real-time feedback, SSI supports the critical requirements of modern industrial automation and control systems.
SSI Data Transmission Mechanism
SSI operates with remarkable simplicity and efficiency, using just two primary lines for communication: a data line for transmitting the actual information and a clock line to synchronize the transmission. This setup is key to the protocol’s reliability, especially in environments where precision is critical.
- Data and Clock Lines: The data line carries the information bits from the encoder to the controller, while the clock line carries pulses from the controller to the encoder. These two lines work in tandem to ensure that data is transmitted synchronously and accurately.
Data Transmission Cycle
The cycle of data transmission in SSI is a systematic process that guarantees the integrity and accuracy of the data transferred between the encoder and the controller. It consists of three main stages:
- Initiation:The cycle begins with the controller generating a clock signal, signaling the encoder to prepare for data transmission. This initial step is crucial for establishing the timing framework within which the data exchange will occur, ensuring that both the encoder and controller are synchronized from the outset.
- Data Transmission: In response to each clock pulse, the encoder sends a corresponding data bit back to the controller. This sequential transmission ensures that each bit is aligned with a specific clock pulse, thereby maintaining the integrity of the data sequence. The process continues bit by bit, with the encoder transmitting the complete data packet serially over the data line. The packet contains the essential information about the encoder’s position or speed, formatted into a predefined sequence of bits that the controller can interpret accurately.
- Validation: Once the data packet has been fully transmitted, the cycle may include an additional validation phase. During this phase, the encoder can send extra bits, such as parity bits, which the controller uses for error checking and validation of the received data.These validation bits provide a means for the controller to verify that the data has been received intact and without corruption. Parity bits, for example, allow for the detection of single-bit errors, enhancing the reliability of the communication by ensuring that any transmission errors can be identified and addressed.
Ensuring Data Integrity and Reliability
The SSI data transmission mechanism, with its emphasis on synchronization and validation, is designed to ensure the utmost data integrity and reliability. This precision is essential in applications where even minor errors in data interpretation can lead to significant issues, such as in CNC machining or robotic control. By meticulously aligning each bit of data with a clock pulse and incorporating validation checks, SSI minimizes the risk of errors, making it a trusted protocol for critical industrial applications.
Applications of SSI in Precision-Required Environments
SSI’s accuracy and reliability make it ideal for various high-precision applications:
CNC Machines
- High-Resolution Feedback: CNC (Computer Numerical Control) machines require exact positioning information to fabricate parts with precision. SSI interfaces with encoders to provide high-resolution feedback on the tool’s position and speed, enabling the CNC controller to make fine adjustments in real-time, thus ensuring the accuracy of the machining process.
- Enhanced Productivity and Quality: The precise control afforded by SSI contributes to improved machining speed and quality, reducing waste and increasing throughput in manufacturing environments.
Robotics
- Dynamic Positioning: In robotics, especially with robotic arms used for assembly, welding, or painting, precise movement is crucial. SSI delivers accurate and reliable feedback on the position and velocity of robotic joints, enabling sophisticated control algorithms to perform complex tasks with high precision.
- Improved Efficiency and Reliability: The use of SSI in robotics enhances the efficiency of automated processes and the reliability of the tasks performed, crucial in production lines where downtime can have significant cost implications.
Elevator Control Systems
- Accurate Floor Leveling: Elevator systems benefit from SSI by receiving precise floor-level positioning information, which is essential for the smooth operation and safety of the elevator. Accurate positioning ensures that elevators stop level with the floor, minimizing the risk of trips and falls.
- System Integration: SSI’s simplicity and reliability make it easy to integrate into existing elevator control systems, improving their performance and safety features without extensive modifications.
Telescope Positioning
- Astronomical Accuracy: In astronomy, the precise positioning of telescopes is vital for accurate observations. SSI enables the exact control required to align telescopes with celestial objects, ensuring that observations are precise and reliable.
- Enhanced Observation Capabilities: The accuracy provided by SSI allows telescopes to track celestial objects with high precision, improving the quality of astronomical data and enabling discoveries that require detailed observation over time.
Additional Applications
- Medical Devices: In medical imaging and surgical equipment, SSI ensures the precise movement and positioning required for accurate diagnostics and interventions.
- Wind Turbines: For monitoring blade position and optimizing efficiency in energy capture, SSI’s reliable feedback is critical for performance and safety.
- Automated Guided Vehicles (AGVs): In logistics and warehouse management, SSI contributes to the accurate navigation and positioning of AGVs, enhancing efficiency and safety in material handling.
These applications underscore the versatility and critical role of SSI in enabling precision and reliability across a broad spectrum of high-tech industries. By providing accurate and noise-resistant data transmission, SSI technology supports the advancement and optimization of automated and precision-dependent processes.