IO-Link Safety: Transforming the Future of Safety Communication and Diagnostics
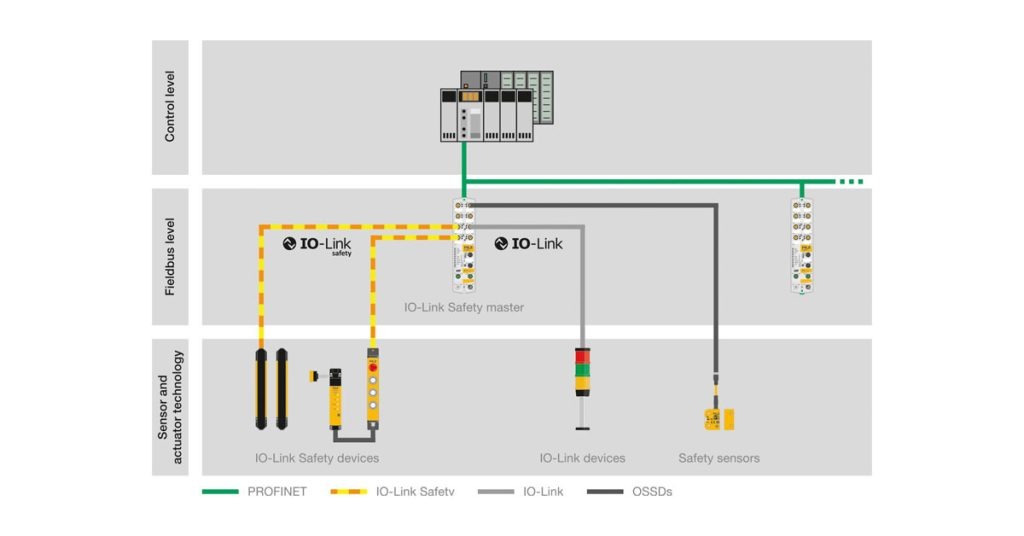
April 2, 2024
By Guillaume Lavoie, CMSE, Product Manager at Pilz Automation
With manufacturing companies moving into industry 4.0, data generated on the plant floor is increasing in importance. IO-Link has been a great success in reducing installation cost, providing greater flexibility and increased data to the user while keeping the communication universal.
The machine safety market has many of the same needs as the standard machine control. The systems need easier installation, which includes wiring simplification and simplification of product configuration. Installers are also looking to have fewer components to stock while still having the flexibility to use the best product for the application.
Direct device to controller wiring is currently the most common architecture. While this architecture is well known and universal it does lead to increased wiring cost and decreased immunity to noise and wiring faults.
Since IO-Link was such a great success IO-Link safety is a natural progression to the technology. The IO-Link safety standard is defined in the IEC 61139-2 standard and can meet Ple or Sil 3 according to EN ISO 13849-1 and IEC 61508/62061 standards respectively.
IO-Link safety acts as an extension of the existing safety networks like Profisafe and enables communication down to the safety component unlocking the path of data held in the component. Just like the existing IO-Link communication, IO-Link safe communication comprises of 3 main parts apart from the safety PLC:
- The IO-Link safety master; the gateway between the higher-level network (ex. Profisafe, CIP safety, FSoE etc.) and the IO-Link safety device.
- The Cable; typically, an unshielded m12 3 wire cable with a length of up to 20m.
- The Safety component ex: Light curtain, Area scanner, door interlock etc.
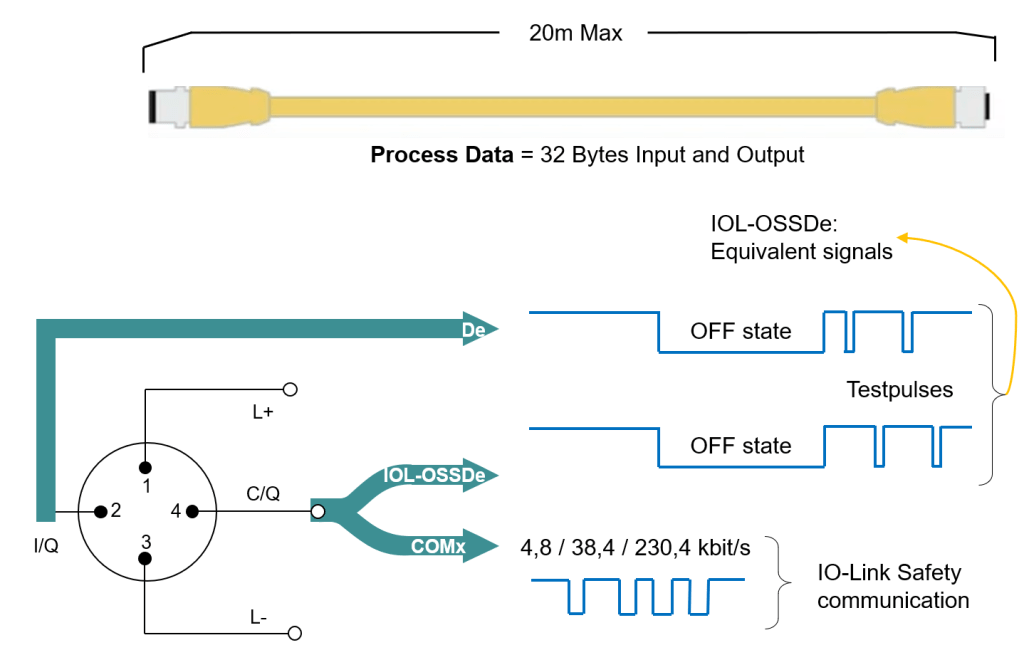
The safe communication remains noise resistant due to its 24v signal level. It can carry up to 32bytes of data bidirectionally at up to 230,4kbit/s, allowing safety, diagnostics, configuration, and additional features to be transferred. In addition to IO-Link safety communication many devices will also be able to function in OSSDe (standard dual channel safety signal) mode when the configuration of the device is needed but an io link master is not in the system.
What makes IO-Link safety communication safe is the addition of the Black channel principle already in use in existing safety networks and the addition of safety measures in the communication that include:
- Message numbering
- Time expectation via a watchdog timer
- Device authentication on startup
- CRC (Cyclic redundancy Check).
By using the standard M12 connection a typical safety device that used to have up to 12 wires which could take over 1 hour to wire in traditional ways can now be connected in less than a minute. The connection is less prone to wiring errors and since IO-Link safety provides identification data a device connected in the incorrect port can be detected and corrected immediately. The IO-Link safety masters are even downward compatible with standard IO-Link devices making your system even more universal.
Pilz will be introducing in the first half of 2024 its first IO-Link safety devices. The Profisafe IO-Link safety master will include 4x IO-Link master ports compatible for both standard and Safe IO-Link devices and 4 Traditional safety IO ports allowing you to take advantage of the new components but also supporting exiting safety components on the market. The next generation of the advanced light curtain PSENopt II Advanced will take advantage of IO-Link for configuration for applications where Blanking, Muting etc. are required and additional diagnostics will be provided like single beam evaluation.
The future PITgatebox with IO-Link Safety will also help reduce cost and provide more flexibility and reduced cabling complexity by allowing up to 15 Pilz SDD (Safety Device Diagnostics) enabled safety components to be daisy chained to the IO-Link PITgatebox allowing 16 safety devices to be connected a single IO-Link Safety port.
Keep an eye out for all the innovations that will be introduced in the coming year to make your plant smarter and safer.
For more information, visit the Pilz website HERE.
Register HERE for the upcoming webinar to learn more and interact directly with a Pilz Specialist.