Machine Safety Strategy in Manufacturing: Why It Matters and How to Get Started
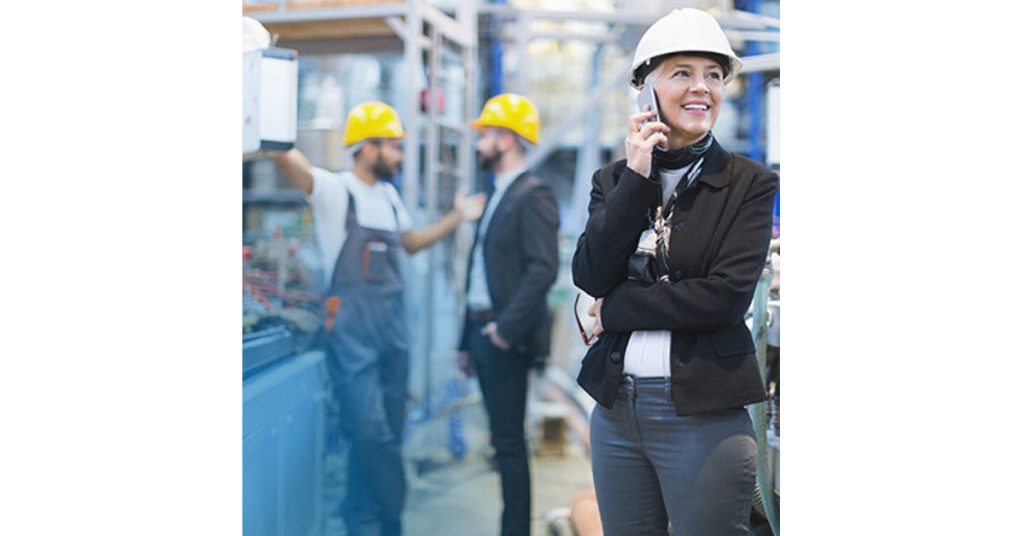
February 1, 2024
Machine-related accidents in the workplace can have devastating consequences, causing injuries, disabilities, and even fatalities. These incidents also result in significant financial losses for businesses. To mitigate these risks, it is crucial for companies to establish a comprehensive machine safety strategy.
This strategy should encompass compliance with standards and regulations, hazard identification and risk assessment, implementing safe work procedures, and regular maintenance and inspections. This article will explore the significance of machine safety in industrial workplaces and offer guidance initiating the development of a machine safety strategy.
Developing a machine safety strategy is essential in industrial workplaces to prevent accidents, injuries, and fatalities related to machinery and equipment. This strategy involves identifying hazards and implementing effective risk mitigation measures. By adhering to machine safety protocols, industries ensure compliance with regulations and create a safe working environment. Key elements of a comprehensive strategy include conducting risk assessments, installing safeguards, implementing safe work procedures, and scheduling regular maintenance and inspections. Prioritizing machine safety not only protects workers but also enhances overall equipment effectiveness.
Adhering to industry standards and regulations is crucial for ensuring machine safety. Notable standards include ISO 12100 and ANSI B11.0 which provide guidelines for machine design, risk assessment, protective measures, operator training, and maintenance procedures. Additionally, different industries and regions have their own safety regulations, such as the Machinery Directive in the European Union and OSHA regulations in the United States. Regulatory bodies play a significant role in enforcing safety standards and ensuring compliance by conducting audits and investigations.
Non-compliance with safety regulations can lead to serious consequences, including legal penalties, financial losses, reputational damage, and, most importantly, increased risk of accidents and injuries. To stay up to date with evolving safety standards and regulations, it is important to review industry publications, attend safety conferences, and seek guidance from experts. By remaining proactive, organizations can align their machine safety strategies with the latest best practices and regulatory requirements.
Hazard identification and risk assessment are vital for addressing machine safety in industrial workplaces. These processes involve systematically identifying potential hazards associated with machinery and equipment and evaluating their severity and likelihood. Thorough hazard identification and risk assessment enable the development and implementation of effective control measures to mitigate risks.
To begin, gather information about the machinery, including design, operation, and maintenance procedures. Conduct a comprehensive hazard analysis to identify all potential hazards. Assess each hazard based on factors like severity of injury, frequency of exposure, and likelihood of occurrence. Develop and implement control measures, which may include engineering controls, such as machine guarding and safety devices, administrative controls, and personal protective equipment. Regularly review and update the hazard identification and risk assessment, especially with changes to machinery, environment, or procedures. Document the process, findings, and implemented control measures.
Implementing safe work procedures is crucial for an effective machine safety strategy. Clear and comprehensive procedures ensure safe and efficient machinery operations and maintenance. Here’s how to develop and implement them:
- Create clear and concise procedures, documenting all steps, hazards, and safety measures. Use visual aids, such as diagrams and flowcharts, to enhance clarity.
- Train employees in their responsibilities, providing hands-on demonstrations and encouraging questions.
- Regularly review and update procedures to remain effective and compliant with changes. Encourage employees to provide feedback and suggestions for improving procedures.
- Enforce procedures consistently, holding employees accountable for violations and providing positive reinforcement for adherence.
- Monitor and evaluate effectiveness of procedures through observations, audits, and incident analysis. Continuously refine procedures based on evaluations.
By implementing safe work procedures, manufacturers minimize the risk of accidents, injuries, and fatalities, fostering a safe working environment and improving productivity and efficiency.
Regular maintenance and machine inspection are critical for worker safety and production efficiency. Well-maintained machines are less likely to experience breakdowns or malfunctions that can lead to accidents. Maintenance also helps identify potential problems early on. Common maintenance tasks include:
- Visual inspections: Identify any visible damage or wear and tear to the machine.
- Functional tests: Perform tests to ensure that the machine is operating properly.
- Lubrication: Apply oil or grease to the moving parts of the machine to reduce friction and wear.
- Adjustments: Adjust machine as needed to ensure that it is operating within the manufacturer’s specifications.
- Repairs: Fix any damage or wear and tear to the machine.
The frequency of tasks varies based on machine type and manufacturer recommendations.
It is also important to have a system in place for reporting and investigating accidents and injuries. This will help identify hazards and to develop measures to prevent future incidents.
By following these tips, you can help to ensure the safety of your workers and the efficiency of your production processes.