Revealing the Real Story Behind Motor Power and VFD Ratings: Avoid Costly Mistakes
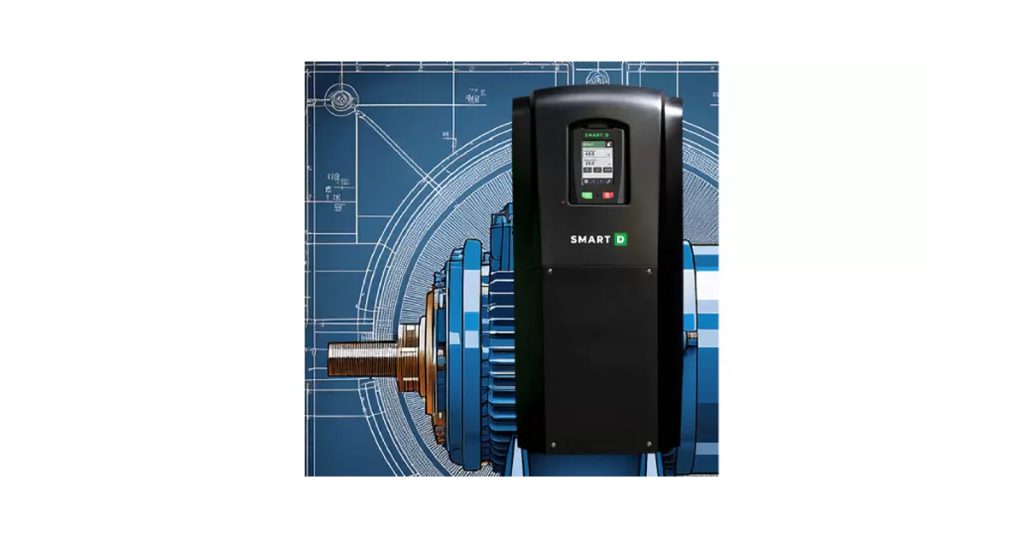
October 24, 2024
Understanding Motor Power Rating and VFD Ratings: The Reality Behind Normal Duty and Heavy Duty Selections
When it comes to selecting a VFD for a motor, many professionals start with the values provided for Normal Duty (ND) and Heavy Duty (HD). It seems straightforward — these ratings supposedly help match a drive to a motor based on its operating cycle. But here’s the truth: these numbers can be misleading. In fact, the Heavy Duty rating is essentially a derated version of the VFD’s Normal Duty value.
Breaking Down Normal Duty and Heavy Duty Ratings
Variable Frequency Drives usually come with two sets of ratings: one for ND and one for HD.
- Normal Duty (ND) covers applications with lower torque needs and fewer overload requirements.
- Heavy Duty (HD) applies when you need higher starting torque, frequent speed changes, or higher overload capacity.
Now, here’s the trick: these ratings aren’t as independent as they may seem. The Heavy Duty number is simply a reduced version of the Normal Duty rating. So, a VFD rated for 30 kW in Normal Duty could only handle 22 kW in Heavy Duty. What’s important to understand is that these two numbers don’t represent different capabilities — HD is just the drive operating in a more restrictive condition.
Why Current Is More Important Than Motor Power Rating
In real-world conditions, the current the motor draws is what really matters, not the power rating printed on the VFD’s datasheet.
- Current Rules the Day:
Motors running at full load, especially when they need high torque, will draw more current. If you select a VFD based on power alone, without considering current, you risk choosing a drive that’s undersized for the job. - Operating Cycles Matter:
Motors with fluctuating loads, like pumps or conveyors, will have varying current demands. You need to account for both the motor’s full load current and its peak conditions to avoid miscalculations.
The Service Factor: How It Impacts Variable Frequency Drive Selection in North America
In North America, many motors come with a service factor — this lets the motor temporarily operate above its rated capacity. For example, a motor with a 1.15 service factor can handle 115% of its rated load for short periods. This can be helpful for overloads, but there are a few things to keep in mind:
- Overuse Equals Overheating:
Relying too much on the service factor can lead to overheating, which reduces the motor’s life. - Don’t Forget the VFD:
If the motor is operating beyond its rated capacity due to its service factor, the VFD has to manage the extra current load. Make sure the drive can handle that — otherwise, you’re risking faults and unnecessary trips.
IEC 60034-1: Defining Motor Services Beyond North America
If you’re dealing with motors in regions that follow IEC standards, the IEC 60034-1 standard comes into play. It classifies motor services into different duty cycles, and this affects both motor and VFD selection:
- S1 (Continuous Duty): The motor runs continuously under a constant load. The Variable Frequency Drive needs to handle continuous operation at rated current.
- S2 (Short-Time Duty): The motor runs at full load for a limited time, followed by a cool-down period. The VFD needs to handle fast accelerations and decelerations.
- S3 (Intermittent Periodic Duty): The motor runs in cycles of load and rest. Peak current handling becomes critical for the VFD.
- S6 (Continuous Duty with Periodic Load Variations): The motor operates continuously, but the load varies. The VFD must manage fluctuating current and torque demands.
Understanding these IEC classifications helps ensure you’re not just looking at peak load conditions but also how the motor and Variable Frequency Drive operate under real-world cycles. Selecting the right VFD means matching it to the motor’s actual service duty, not just theoretical peak ratings.
The Bottom Line: Focus on Current, Not Just Power Ratings
At the end of the day, ND and HD ratings might help with an initial selection, but they’re far from the whole picture. You need to consider the motor’s actual current demands during operation. Combine that with a solid understanding of the service factor (if applicable) and IEC duty classifications, and you’ll be much closer to choosing the right VFD for the job. The goal is to avoid underestimating the current load, which could result in costly downtime or performance issues down the road.
Follow the step-by-step approach described in the Clean Power VFD user guide to select the VFD that fits your application: /clean-power-vfd-publication/vfd-selection