Rittal: Why Automotive Manufacturers Should Make the Move to Busbar Power in 2025
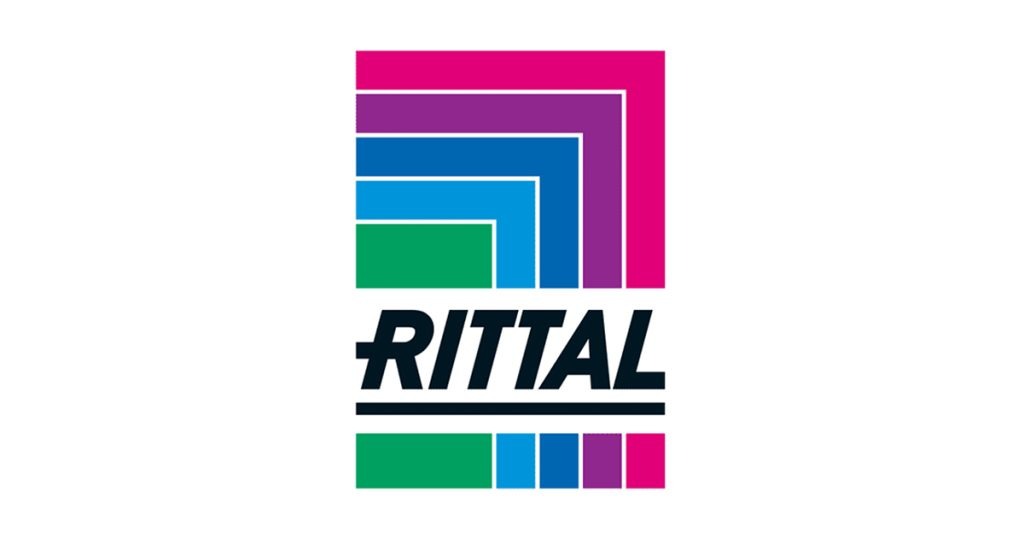
January 27, 2025
Rittal: Why Automotive Manufacturers Should Make the Move to Busbar Power in 2025
As automotive manufacturing continues to grow, with North American production projected to increase by 5% annually through 2031, manufacturers are under pressure to optimize workflows, reduce costs, and enhance efficiency. To stay competitive in 2025, they need flexible industrial automation solutions that can adapt to evolving production needs and enable smarter operations.
One such solution is Busbar Power Distribution Panels, a high-performance alternative to traditional wiring systems. These panels not only reduce the automation footprint but also improve energy efficiency, streamline maintenance, and enable scalability. Here’s why automotive manufacturers should make the switch to busbar power in 2025:
1. Busbar Power Reduces the Automation Footprint
One of the most significant advantages of busbar systems is their ability to eliminate bulky power blocks associated with traditional panel wiring. By removing these large units, automotive manufacturers can:
- Optimize Production Floor Space: A smaller automation footprint means better utilization of space, which is especially critical for new or expanding applications.
- Enhance Enclosure Configuration: Busbar panels replace traditional side-line wiring and accessories, freeing up space and increasing flexibility within the enclosure.
Legacy panels rely on numerous wires and cables to connect power distribution blocks (PDBs), which are space-intensive and limit configuration options. Busbar systems, on the other hand, use a single conductor to carry the same amperage, reducing the number of feed cables and simplifying the overall design.
From an assembly and installation perspective, busbar’s reduced size and simplified engineering allow for faster component swapping, easier maintenance, and quicker troubleshooting. Additionally, busbar systems do not require as much specialized tooling as traditional wiring, helping maximize uptime and productivity.
2. Improved Energy Efficiency and Cost Reduction
Energy efficiency is becoming a key priority for automotive manufacturers, particularly with the global shift toward sustainability and carbon reduction. Traditional wiring systems often result in energy loss due to inefficient connections and resistance in complex cable configurations. Busbar systems address these challenges by:
- Reducing Energy Loss: The streamlined conductor design ensures a more efficient power flow with minimal resistance.
- Lowering Operating Costs: By reducing energy waste and simplifying maintenance, busbar systems contribute to significant cost savings over time.
- Aligning with Sustainability Goals: Energy-efficient systems help manufacturers meet regulatory requirements and align with consumer expectations for greener operations.
As the automotive industry transitions further into electric vehicle (EV) production, the need for energy-efficient power systems like busbar will become even more critical to balance power demands while minimizing environmental impact.
3. Simplified Engineering for Scalable Manufacturing
Traditional panel wiring systems often restrict wire sizes and leave little to no room for future expansion. If expansion is possible, it typically involves complex processes like drilling or tapping, resulting in costly downtime and production delays. Busbar power panels address these limitations by offering modular, pre-engineered components that make scaling easier and more efficient.
This scalability is particularly valuable as manufacturers expand their EV production lines and adapt to market trends. Busbar systems allow for:
- Customized Configurations: Panels can be tailored to specific applications with varying sizes and lengths, optimizing the enclosure footprint.
- Standardized Design: Manufactured according to International Electrotechnical Commission (IEC) guidelines, busbar systems ensure faster and easier configuration compared to traditional wiring.
Rittal’s innovative modular busbar systems further simplify expansion with their ability to accommodate new configurations without the need for drilling or tapping. This makes them ideal for retrofitting or customizing enclosures for unique deployment needs, such as EV charging stations or renewable energy applications.
4. Modular Solutions for Versatile Applications
Busbar systems are designed to meet the demands of both traditional automotive manufacturing and the growing EV market. Rittal’s Mini-PLS Busbar System, for example, offers:
- Plug-and-Lock Connections: A 3-pole, plug-and-lock connection at the front of the panel simplifies cable configuration.
- Flexible Mounting Options: The Mini-PLS can be top-mounted, allowing for better use of space within the enclosure.
These features make busbar power an attractive solution for automotive manufacturers looking to optimize efficiency and performance while simplifying installation and configuration.
5. Supporting Future Trends and Global Growth
With the growing adoption of EVs, the expansion of renewable energy, and the global push for greener manufacturing practices, busbar power systems align perfectly with the trends shaping the automotive industry in 2025 and beyond. Their modularity and scalability make them ideal for:
- Expanding EV production facilities
- Building national networks of EV charging stations
- Integrating renewable energy solutions into automotive manufacturing processes
These forward-looking applications highlight busbar power systems as a foundational technology for future-proofing manufacturing operations.
Conclusion: Drive Efficiency with Busbar Power in 2025
As automotive manufacturers gear up for continued growth, the need for smarter, more flexible power solutions is clear. Busbar power panels offer a scalable, efficient alternative to traditional wiring systems, helping manufacturers reduce their automation footprint, enhance flexibility, improve energy efficiency, and align with sustainability goals.
Whether you are expanding EV production, retrofitting facilities, or building new lines, Rittal’s modular busbar systems can support your mission-critical tasks. It’s time to make the move to busbar power and accelerate your productivity in 2025.