Rockwell Automation: Flexible Biomanufacturing Solutions Defy Economies of Scale
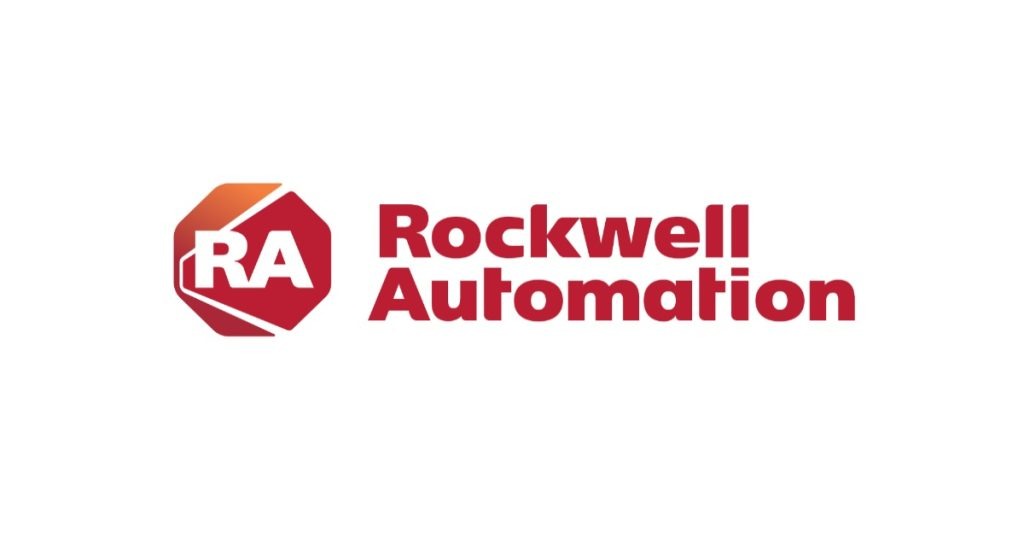
February 28, 2025
How Digital Technologies & AI Can Offer Flexible Biomanufacturing Solutions
By: Billy Sisk, Life Sciences Industry Manager EMEA, Rockwell Automation.
For more than a decade, there have been significant changes in how drugs are manufactured. The pharmaceutical industry has been undergoing a paradigm shift in its manufacturing practices, with an increased focus on flexible manufacturing to accommodate the production of complex, targeted medicines.
In parallel, advances in digital technologies and AI are becoming increasingly important for the continued success and competitiveness of global manufacturing. But how is Industry 4.0 impacting the pharmaceutical sector and specifically how drugs are manufactured? The “Facility of the Future” concept first caught my attention about eight years ago. Since then, we have been working internally and with customers to develop digital and automation solutions that address the challenges found in such a facility. Let us discuss how technologies advancements are affecting the primary biopharmaceutical manufacturing process and how automation is evolving to help support flexible, scalable manufacturing.
With the Industrial Internet of Things (IIoT) and Industry 4.0-capable systems providing momentum, companies demand more agile and flexible manufacturing practices to meet the industry’s drive towards more personalized medicines. Simultaneously, manufacturers are seeking competitive solutions that meet regulatory and security challenges.
These considerations, coupled with a growing trend of locating smaller, more agile facilities closer to customer markets, are pushing manufacturers towards facilities that can be easily reconfigured to support the manufacture of multiple products, including complex therapies like cell and gene therapies. Additionally, manufacturers are looking for repeatable and scalable solutions that can be developed in one location and then deployed in other locations, minimizing capital expenditure and reducing time to market. This is what is known as a Facility of the Future.
The “batch of you” philosophy is also rewriting the economies-of-scale rule book that has underpinned pharma for so many years. To make it feasible, pharmaceutical companies must deploy technology that leverages every capability and nuance of a fully integrated and connected processing and automation system.
Digital technologies are becoming increasingly important in this context. It involves the near-seamless transfer of data and processes from development to manufacturing, ensuring that complex therapies can be produced as efficiently and consistently as possible. This digital approach helps to streamline operations, reduce errors, and accelerate time to market. Highly flexible and agile manufacturing facilities help answer this challenge for many of our customers, producing personalized and advanced treatments but it does have additional demands and challenges for production and operations teams working in these environments.
For example, facilities should be multi-product capable, use disposable, single-use consumables, and deploy an agile, plug and play, integrated architecture to make changeovers as quick, seamless, and error-free as possible. This requires operators to manage and troubleshoot a complex network of assets and devices. Despite automation, there are still many manual interventions required, such as making connections or adjustments, which can be error prone.
How Digital & Automation Technologies Can Assist
Real-Time Monitoring & Control: Digital technologies like IoT and AI enable real-time monitoring of the manufacturing process. This allows for immediate detection and correction of deviations, helping to ensure consistent product quality.
Predictive Maintenance: AI-driven predictive maintenance can forecast equipment failures before they occur, reducing downtime and achieving smooth operations. This is particularly important in a flexible manufacturing setup where equipment is used intensively.
Advanced Training Tools: Augmented reality (AR) and virtual reality (VR) can provide immersive training experiences for operators, helping them understand and manage the complexities of flexible manufacturing systems more effectively.
Digital Twins: Digital twins create a virtual replica of the manufacturing process, allowing operators to simulate and optimize production without disrupting actual operations. This helps in planning and executing complex manufacturing layouts and tasks more efficiently.
Automated Changeovers: Automation systems can significantly reduce the time and errors associated with changeovers. Autonomous mobile robots (AMR) and advances in capability and flexibility of robotic arms can handle the physical aspects of changeovers, while software technology solutions can manage the configuration changes.
Enhanced Connectivity: Advanced communication protocols and centralized control systems allow for all equipment and systems to be seamlessly integrated. This reduces the complexity of managing interconnected devices and improves overall efficiency.
Guided Work Instructions: Digital work instructions, often enhanced with graphical aids, can guide operators through complex tasks step by step, reducing the likelihood of errors and improving efficiency.
By leveraging these digital and automation technologies, flexible manufacturing plants can overcome the complexities faced by operators and production staff, leading to more efficient, reliable, and adaptable production processes required to produce advanced therapeutics.
In my mind, the automation concept must enhance and not hinder the overall objectives of the Facility of the Future.
By listening to our customers and delivering solutions that meet their most pressing needs, we are in a great position to help define the future roadmap – where data is king and patients get the increasingly complex treatments they need, without economics and technology getting in the way.