How GraceSense is Predicting Unplanned Downtime
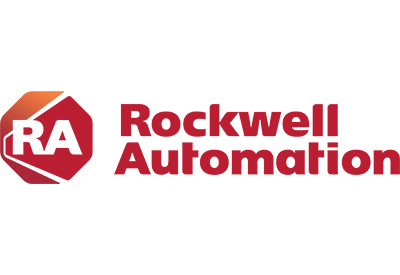
March 7, 2023
By Nick Schiltz, Content Marketing Specialist, Grace Technologies, Inc.
Nobody wants to deal with unplanned downtime, but for many it is unavoidable. Maintenance personnel are the first responders to an unforeseen event and must perform reactive maintenance to get their plant back up and running as quickly as possible. Unplanned downtime poses numerous risks including lost production time. This is also the window where over half of safety incidents occur. When production unexpectantly halts, lives are put at risk.
To address these risks, a globally leading nonwovens manufacturer initiated an investment project to integrate an IIoT driven equipment monitoring system. In turn, this act would improve their maintenance insights and decrease the risk of their maintenance teams during reactive maintenance scenarios. With better insights, they can help prevent unplanned downtime by addressing anomalies before they become catastrophes.
In the example of the nonwovens manufacturer, the production of their products requires fibers to be processed through complex machinery. During this process, excessive heat generated by the equipment can result in a thermal event when the fibers make contact. This scenario could result in unplanned downtime, material loss, and the risk of injuries or fatalities to personnel.
In their search for a predictive technology solution, the manufacturer discovered Grace Technologies through their local distributor. Grace is a Rockwell Automation Technology Partner manufacturing electrical safety and predictive maintenance products. The distributor worked with Grace to introduce the manufacturer to the GraceSense™ Predictive Maintenance System.
The field proven Predictive Maintenance System is an asset condition monitoring system that uses wireless sensor technology integrated alongside wired sensors. Advanced data analytics provide asset managers with deep insights to machine health to effectively prioritize resources and maximize the value of their maintenance spend. GraceSense technology improves overall plant reliability, safety, and maintenance metrics by remotely monitoring asset health and sending timely notifications to plant floor personnel through SMS or email alerts with pre-configured, step-by-step remediation instructions when anomalous behavior is detected.
What immediately appealed to the nonwoven manufacturer’s Maintenance Manager was the wireless sensor technology provided by GraceSense. They were looking for a solution that would provide temperature feedback without wiring up their machines. While their initial concern was with temperature monitoring, they are also planning on using the vibration monitoring features on more equipment in the future.
Currently, they have deployed 140 GraceSense Vibration & Temperature Nodes onto equipment throughout the manufacturing plant. These nodes are wireless sensors that monitor vibration and temperature to assess the health of rotating equipment. Using advanced edge processing and IEEE 802.15.4 ZigBee compatible communication, the nodes enable personnel to monitor equipment, detect anomalies, and predict asset health continuously. Multiple mounting options deliver quick deployment across applications in any industry and their replaceable batteries deliver 3-5 years of life.
The Vibration & Temperature Nodes communicate via GraceSense gateways that transfer accumulated field node information to an actionable troubleshooting platform through the Maintenance Hub Cloud and/or PLC, SCADA, DCS systems. Any customer can choose from three types of gateways to fit their application; CloudGates, ControlGates, and ComboGates.
CloudGates transfers field node information to the browser-based Maintenance Hub where actionable, real-time insights are provided. This Wi-Fi or LTE configuration can provide cloud-based support to all wireless nodes within a 30m line-of-sight radius, making the architecture massively scalable. ControlGates provide users quick integration into their control network via PLC/SCADA and EtherNet/IP™ or Modbus TCP/IP communication options.
The Maintenance Manager described the integration and application of the GraceSense system as very quick and simple. The cloud-based capabilities proved to be an effective solution, but they also wanted to integrate the system within their PLC network. The team at Grace worked with Rockwell Automation to create a solution for the nonwovens company to use both the cloud and PLC networking to transmit data from the Predictive Maintenance System.
To support this application, the nonwovens manufacturer installed ComboGates to communicate with their 140 Vibration & Temperature Nodes. They currently have 15 ComboGates transferring information from their field nodes. ComboGates are a hybrid configuration of the CloudGate and ControlGate configurations. This option securely provides data to both PLC/SCADA/DCS systems using EtherNet/IP™ or Modbus TCP/IP along with featuring communication options for field node information transfers to the Maintenance Hub via Wi-Fi or LTE service.
Grace Technologies provided the node and gateway installation oversight with the manufacturer’s on-site staff as well as their electrical contractor. Grace performed a site survey to determine locations of gateways and made sure they could service the nodes that they had installed. Once the hardware was installed, Grace worked hand in hand with Rockwell Automation to provide the PLC integration support.
Alarms configured within the manufacturing plant’s PLC infrastructure. The data pulled from the Predictive Maintenance System is displayed on HMIs when temperature reaches a warning level. When temperature anomalies are detected by any of their 140 nodes, the system will automatically trigger a shutdown to help prevent a thermal event. The nonwovens manufacturer’s Maintenance Manager stated that the GraceSense Predictive Maintenance System has already detected abnormal temperature rises and helped prevent six unplanned downtime scenarios that could have resulted in contaminating their production or a thermal event.
Before GraceSense, their unplanned downtime could range from 5 hours to, in even more catastrophic downtime scenarios, up to several weeks of downtime. With the GraceSense deployment, they are now detecting future events and addressing them with just 1 hour of planned downtime.
The parent company of the nonwovens manufacturer intends to use this location as a testing grounds for the GraceSense Predictive Maintenance System with plans to potentially expand their integration into more of their facilities.