What is a PLC?
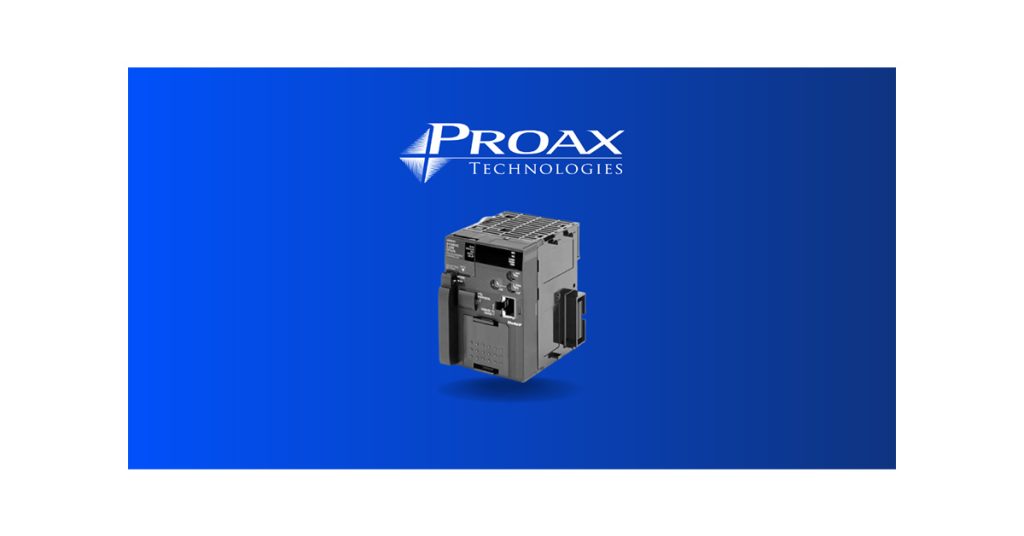
October 26, 2023
Programmable Logic Controllers (PLCs) are the linchpins of modern industrial automation. These ruggedized computers are engineered to monitor and control machinery, assembly lines, and robotic devices, optimizing operations for heightened efficiency and productivity.
With their user-friendly programming and robust fault diagnosis, PLCs offer a streamlined solution to manage complex processes. Their modular design ensures a seamless fit for diverse industrial applications, making PLCs a prime choice for businesses aiming to leverage automation for enhanced operational excellence.
From Relay to Revolution: PLC History
- First PLC, Modicon’s model 084, was unveiled by Dick Morley in 1969, aimed at replacing relay systems for General Motors and Landis.
- This innovation eliminated the need for rewiring and additional hardware for each new logic configuration.
- Model 084 notably enhanced control functionality while minimizing the required cabinet space.
- The commercial stride in PLCs’ journey was marked with Modicon’s model 184 in 1973, designed by Michael Greenberg, setting a commercial milestone in industrial automation.
PLC Core Anatomy – What Is Inside?
- Central Processing Unit (CPU): The brain behind the operations, executing control instructions from the user’s programs stored in nonvolatile memory, ensuring retention even post power loss.
- Communication Interface: Facilitates interactions with external entities such as I/O devices, programming devices, networks, and other PLCs, building a cohesive control network.
- Memory (ROM and RAM): ROM houses the core instructions, while RAM provides the workspace for temporary data during operations.
- Input/Output (I/O) Modules: The sensory and action organs, interfacing with the external world for data intake and command execution.
- Power Supply: The lifeblood of the PLC, converting and providing the necessary voltages for operation.
- Programming Device: The tool to instill the desired logic and control sequences, shaping the PLC’s behavior to meet the application needs.

How PLCs Work
Unlocking the functionality of a Programmable Logic Controller (PLC) can be boiled down to a rhythmic cycle that follows four essential steps. This sequential dance is choreographed to ensure seamless control and automation:
1-Sensing the Surroundings (Input Scan):
The PLC kicks off its cycle by scanning the connected input devices such as sensors, switches, or meters. This step is crucial as it gathers real-time data regarding the process or system it’s monitoring.
2-Deciphering the Data (Program Scan):
Post data collection, the PLC delves into the heart of its operation – executing the pre-programmed logic. Here, it deciphers the gathered data, making sense of the current state of affairs.
3-Commanding the Control (Output Scan):
Based on the logical conclusions drawn, the PLC now orchestrates the output devices like relays, lights, valves, or drives. It’s where the PLC directs actions, ensuring the system behaves as intended.
4-Maintaining the Momentum (Housekeeping):
The cycle concludes with housekeeping chores which include communicating with programming terminals, conducting internal diagnostics, and possibly interacting with broader networks like SCADA systems for a holistic operational view.
Each step is a note in the symphony of automation that PLCs conduct tirelessly, ensuring a harmonious performance in the industrial environment. Through this cyclic operation, PLCs prove to be the silent yet indispensable maestros, orchestrating a myriad of processes with precision and reliability.
PLC Types
Compact PLCs: These are suitable for simple applications with a limited number of I/Os (Input/Outputs). They are cost-effective and are typically used in standalone applications.
Modular PLCs: These are more flexible and can be expanded by adding modules for I/O, communication, and other functions. This makes them suitable for larger applications where scalability is essential.
Rack-mounted (High-performance PLCs): These are used for large industrial applications. They consist of a chassis (rack) into which different modules can be inserted. They can handle a high number of I/Os and are highly customizable.
Machine Automation Controllers (MAC): Advanced controllers that blend PLC functions with other automation tasks. MACs, like Omron’s NX1P, handle complex motion control, networking, and IoT integration. They are ideal for precise coordination in automation setups.
Choosing the Right PLC: What to Keep in Mind
1-Voltage Type:
- AC Voltage: If your system operates on AC voltage, look for PLCs designed to work with AC power.
- DC Voltage: Conversely, if DC voltage powers your system, a DC-compatible PLC is the way to go.
2-Memory:
- Ample Memory: Should your program be extensive, target PLCs with a generous memory capacity.
- Moderate Memory: For less complex programs, a PLC with moderate memory should suffice.
3-Speed:
- High Speed: High-speed PLCs are suitable for time-sensitive applications.
- Standard Speed: For regular operations, standard speed PLCs are cost-effective and efficient.
4-Programming Software:
- Familiar Software: Opt for PLCs programmed with software you are comfortable with.
- New Software: If keen on exploring, choose PLCs with new, highly-rated programming software.
5-Input/Output (I/O) Capacity:
- High I/O Capacity: Required for applications with numerous inputs and outputs.
- Standard I/O Capacity: Adequate for applications with a moderate number of I/O requirements.
6-Analog and Discrete I/O Handling:
- Mixed I/O Handling: Choose PLCs capable of handling both analog and digital I/O if your application demands it.
- Specific I/O Handling: Select PLCs that excel in either analog or digital I/O based on your specific needs.
7-Communication:
- Multiple Ports/Protocols: Beneficial for diverse communication needs.
- Standard Communication: Suitable for straightforward, less complex communication requirements.
8-Network Connectivity:
- Network-ready PLCs: Ideal if remote monitoring or data sharing is crucial.
- No Networking: Opt for simpler PLCs if networking isn’t a priority.
9-Location and Distribution:
- Centralized System: Choose compact or rack-mounted PLCs for centralized setups.
- Distributed System: Modular PLCs or those with remote I/O capabilities are apt for distributed systems.
By aligning your answers to these considerations with the features of available PLCs, you are well on your way to making an informed decision that caters to your project’s needs.