New from Festo: smart optical inspection that’s extremely flexible yet simple enough for any user
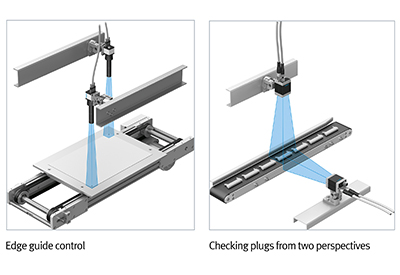
December 9, 2019
Festo’s new SBRD smart camera system delivers exceptional flexibility for the professional user – covering a dozen fields of analysis, tracking and verification for automation and robotics. Yet it’s so simple to set up and operate that even novices can make full use of its extensive capabilities. The result is an extremely cost-effective solution for fast, reliable inspection that can perform a wide range of tasks where using a multi-camera approach is required.
The SBRD system is comprised of three elements: 1) extremely lightweight, compact high resolution USB cameras that can deliver monochrome or colour images with a resolution up to 5 megapixels; 2) a specially designed, space-optimized yet powerful controller with two camera interfaces; and 3) its own image processing software, the Camera Configuration Studio (CCS), which delivers fast process-reliable results.
The fanless remote head controller is designed for multi-camera tasks and has a dual core processor and PROFINET communications. The two camera interfaces allow inspections to be carried out from several different perspectives with large fields of view. The many inspection and functions the system can run make it possible to check almost anything: for example, pattern matching, brightness inspection, colour checking, data matrix code or bar code reading, pixel cloud location, circle and edge finding, optical character reading (plain text in various fonts and forms), and much more.
With the CCS software, users can configure inspection programs and define, log and adjust all processes from image recording to the input and output parameters – and simulate them in advance on the PC. The software processes images using image analysis and image lists rather than individual images. It’s a much simpler set-up process than the ones used with most conventional inspection systems. Users simply take different sample pieces and record these. Then, they can define exactly what needs to be analyzed and how this should be done. The tolerance ranges are based on the results data of the recorded images, but manual changes can be made as well. Even better, the software’s CCSxRun tool enables test tools to be parameterized quickly. Users only need configure the settings once, and then the system applies them to all objects it detects. This makes program development and maintenance easier and keeps the program structure neat and tidy.
For more information, visit www.festo.com.