Express Customization and Expanded Product Offering Now Available for nVent HOFFMAN Global IEC Floor-Standing Enclosures in North America
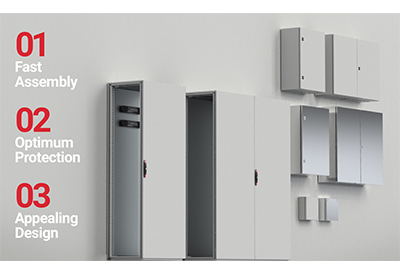
April 26, 2021
To offer customers more flexibility and faster access to high-quality products, nVent Electric plc, a global provider in electrical connection and protection solutions, recently announced the expansion of its nVent HOFFMAN Global IEC offering and Express Customization services in North America.
As part of its commitment to redefine simplicity when ordering, designing, configuring and assembling enclosure solutions, nVent launched a comprehensive global portfolio of IEC-rated enclosures and accessories in North America for optimum protection of equipment in electrical infrastructure and a variety of industrial applications. Specially designed and engineered for global use, the portfolio accelerates the design and installation process through interchangeable accessories and patented tool-free, click-in technology for assembly, while streamlining ordering with global part numbers.
To meet the needs of customers who need fast delivery, the nVent HOFFMAN brand is expanding its Express Customization offering to Global IEC Free-Standing enclosures, which include standard-sized enclosures that ship from the factory within 10 days. This Express Customization service allows modifications for standard sizes of the Global IEC Modular Floor-Standing enclosures in mild steel, including:
- – Simple holes and cutouts
- – 28 paint colors, including OSHA safety options
- – Accessories options
These new services come as part of the company’s commitment to make it easier for customers to do business with nVent and its brands. nVent also offers enclosure customization through local HOFFMAN Certified Modification centers, and recently launched a new website, hoffman.nvent.com, to seamlessly guide customers through selecting a product, requesting a quote and finding their closest distributor or sales representative in North America.
In addition, the nVent HOFFMAN IEC portfolio has expanded to include more sizes and accessories to offer even better availability and versatility through standard stock. New additions include:
- – More standard enclosure sizes and associated accessories, such as plinth bases, side covers, mounting profiles and mounting plates
- – 19” accessories for rack mounted equipment and swing frames for some industrial networking applications
- – More handle options, including a slotted insert