Flexible Modular System of Highly Dynamic AL8000 Linear Motors
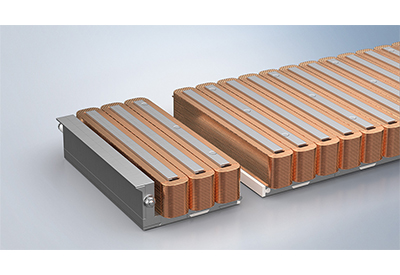
June 25, 2021
The new AL8000 linear motors supplement the Beckhoff drive technology portfolio by another innovative product series. In the three widths of 50, 80 and 130 mm, their modular design enables new solutions for linear motion applications in modern mechanical engineering.
Linear motors such as the AL8000 allow direct transmission of the motor power to the load to be moved and are therefore also called direct drives. No additional mechanical transmission elements are required, which would otherwise have to be taken into account in the design. This represents a decisive advantage over conventional mechanisms such as rack and pinion, spindle and toothed belt drives.
Linear drive technology – advantages and requirements
Due to the direct transmission of the linear motor power, a backlash-free construction between the motor and the load can be realized, which makes high-precision applications possible. The linear motor is therefore a wear-free drive and does not require regular maintenance. Since a linear motor eliminates the speed-limiting components through the direct operating principle, applications with the highest demands on speed and dynamics can be operated without any problems with maximum precision at the same time.
Even if the mechanical, backlash-prone transmission elements are eliminated by the use of a linear motor, other structural components, such as adequately dimensioned guide rails and bearings, are required. In addition, there is an individual machine carriage, which provides for the mounting of the coil part as well as other machine components. These structural components are indispensable for the completion of a linear axis based on a linear motor and often pose a challenge to the design.
Simplification through symmetry and modularity
In order to enable the designers to work as flexibly as possible despite machine-specific requirements, the development of the AL8000 linear motors focused on a symmetrical design and thus the realization of the simplest and most uniform machine design possible. The main approach is the modular coil concept of the AL8000. It aims to facilitate the design of the individual machine carriage with regard to the attachment of the coil part and to create a common basis for different machine types or different coil parts.
In line with the modular concept, the entire coil part is assembled from individual identical segments during final production at Beckhoff in Germany. These segments represent the smallest modular unit of the coil part and comprise three motor windings. The shortest linear motor in the series therefore consists of one segment or three motor windings. Depending on the force requirements, the linear motors can be assembled from up to 15 segments, so that peak forces up to 6,750 N are possible in a compact design. The coil part therefore always comprises a multiple of this smallest modular unit. As a result, the linear motor series is systematically and symmetrically extended, resulting in the following constructive advantages:
- – The series connection of identical and space-optimized segments results in a compact design of the coil parts. The defined width and installation height of the AL8000 meet maximum force requirements in the shortest possible housing and thus achieve a very high force density. Since the new linear motors are optimized for such a high force density, this effect becomes clearer with increasing force demands. The coil part is therefore extremely short, and as a result, the travel path and thus the entire machine can be designed shorter and for a minimized footprint.
- – The modular coil concept also enables an exactly symmetrical structure of the coil parts, i.e., they always have the same drilling pattern grid within one of the widths due to always using the same stator segments. Thus, regardless of the length of the coil part, the respective distances are identical both within a longitudinal row and within a transverse row of the drilling pattern. In this way, the machine manufacturer can use a uniform drilling pattern for the machine carriage and flexibly use the longer or shorter AL8000 within a width without having to make any structural changes. It is also possible to manufacture a machine carriage for the largest motor in the 130 mm width across all widths and to install each coil part of the smaller width AL804x (80 mm) in addition to the shorter versions of the same width. However, the symmetrically uniform structure does not only bring constructive advantages. In addition, an even force build-up and a homogeneous heat distribution over the entire coil part is also realized, which enables optimal machine operation.
- – In addition to the coil parts, the magnetic plates also have a uniform drilling pattern within a width group, so that magnetic plates of different lengths can be used flexibly within a width.
If the entire linear axis is considered, cables and the associated drag chains are also required in addition to the linear motor and the mechanical components. Here, too, the AL8000 linear motor offers advantages for the machine manufacturer by combining the power supply with the thermal protection contact. Due to the merging of the two cables, one cable is omitted, which would otherwise have to be installed from the linear motor through the machine to the control cabinet. This not only significantly reduces material expenditure, but also minimizes installation effort and space requirements in the drag chain.
New concept for a wide range of applications
The new, highly dynamic AL8000 series offers linear motors in a compact design with maximum flexibility for the machine manufacturer. Their use reduces the space required in the machine in several respects and leads to a cost reduction. Currently, the AL8000 portfolio comprises 28 different coil parts, which are divided into three different widths.
This broad spectrum covers almost every force and speed requirement and thus enables a suitable drive solution for almost every linear application. Especially since specific customer requirements can also be flexibly addressed for very special requirements outside the standard portfolio. In this case, any linear motor can be designed within the modular coil concept.