RoboDK TwinTool Offers Fully Automated Tool Calibration for Industrial Robots
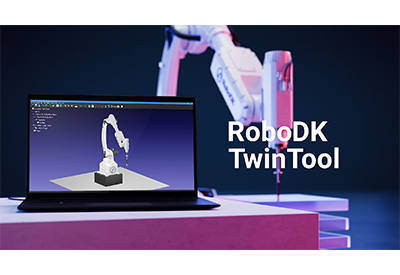
May 25, 2022
Canadian robotics software provider RoboDK has released TwinTool, an application that offers fully automated robot tool calibration for industrial robots. TwinTool is a cost-effective, quick, and easy solution to improve the tool’s accuracy in a wide variety of manufacturing applications. It is a competitive alternative to costly and complex robot calibration services currently available on the market.
Industrial robots are increasingly used for high-accuracy manufacturing tasks, such as assembly, soldering, and machining. However, new users are sometimes disappointed by the apparent low accuracy of their robots. They invest in expensive robot calibration systems to try to improve the accuracy.
Albert Nubiola, CEO of RoboDK, explains this is not always required:
“Many users don’t realize how important it is to calibrate the tool properly. They believe they need to calibrate the whole robot. However, properly calibrating the tool center point (TCP) can provide a significant improvement in accuracy.”
Repeatable, not accurate: the problem with industrial robots
Industrial robots have high repeatability, but low accuracy. This means they can move to the exact same position every time (repeatability), but their position doesn’t accurately match the world coordinate system (accuracy).
There are two main types of calibration procedures for improving a robot’s accuracy. Robot calibration requires precision laser systems to calibrate the robotic mechanism itself. Tool center point (TCP) calibration is a simpler procedure to ensure the programming system has an accurate model of the robot’s tool.
Samuel Bertrand, Software Developer at RoboDK, explains:
“TwinTool is a quick and affordable solution to automatically calibrate the robot’s TCP compared to other solutions such as laser trackers. Laser calibration is expensive, and many robot applications do not need such high accuracy.”
TwinTool achieves tool calibration with an off-the-shelf sensor
The typical way of calibrating a robot tool center point (TCP) is by a 4-point method, which consist of taking a series of at least for 4 joint readings when moving the tool to the same point with different orientations. This process is time consuming and less accurate as the user needs to move the robot in different position manually.
TwinTool calibration functionality is distributed as a RoboDK App, a plugin that extends the capabilities of RoboDK’s highly popular robot programming software.
RoboDK TwinTool requires an off-the-shelf linear gauge sensor (or LVDT) to directly communicate with any robot and to calculate the robot tool center point (TCP) without human intervention. TwinTool automatically records an unlimited number of points, and the linear gage sensor offers great accuracy for tool definition.
The app is compatible with a wide range of sensors from major brands including Mitutoyo, KEYENCE and Sylvac, allowing it to be versatile with any hardware. Other sensor brands can also be integrated on request.
RoboDK TwinTool supports more than 600 robot arms from 50 different robot manufacturers and is suited for many industrial environments.
This follows RoboDK’s well-established philosophy of remaining brand-agnostic for hardware.
Equally important, RoboDK places great emphasis on the ease of use and safety of its products. TwinTool runs directly from RoboDK, making the bridge between the robot controller and the sensor. No programming skills are required. Users only need RoboDK simulation software, a robot, its tool (spherical or conical), and a sensor. Singularities and collisions are avoided, and trajectories automatically calculated.
“We have created a user-friendly wizard to ensure that the calibration is done correctly and safely,” says Samuel Bertrand. “This is simple enough that it can be used by operators that don’t have robotics knowledge.”
To calibrate a robot tool, the user simply follows this 3-step procedure in RoboDK’s software:
- Select their robot model from RoboDK’s extensive robot library.
- Connect RoboDK to the robot and to the sensor.
- Move the robot on the sensor and start the calibration.
Albert Nubiola says:
“The procedure is fully automated and does not require any manual intervention. It automatically avoids collisions and does not require users to write a single line of code.”
With TwinTool, users can quickly and automatically improve the accuracy of their tool by up to 0.250 mm with some robot setups. This provides an accuracy improvement by 2 to 10 times, depending on the robot and the tool.
“Without this calibration,” says Albert Nubiola, “robot errors can be in the range of 2-5 mm. With this tool calibration, you can usually reduce robot errors up to 0.250-1 mm depending on your application.”
This accuracy improvement is more than enough for most robot applications, even those that require precision. This can save users a lot of money on unnecessary robot calibration services.
Future plans
Users can now request to add TwinTool to their copy of the RoboDK software as an optional RoboDK App.
Bertrand explains they will continue to improve TwinTool’s functionality. “Currently, the tool is oriented towards maintenance modes,” he says. “However, we are working towards a mode that will run the calibration procedure automatically during production.”
RoboDK also plans to extend its App interface by creating a RoboDK App Marketplace. They will invite companies to develop and publish their own apps for the software.
For more information, visit HERE.