Beckhoff: TwinCAT PLC++ – Next Generation PLC Technology

November 12, 2024
Engineering and runtime with a significant leap in performance
Based on well over 40 years of experience with state-of-the-art automation technology, Beckhoff presents the newly developed TwinCAT PLC++, enabling control engineers to make a real leap in project performance. Both engineering and runtime can be accelerated, while the well-known TwinCAT advantages of consistent integration, compatibility and openness continue to be delivered.
TwinCAT PLC++ is a completely new development from Beckhoff that integrates seamlessly into the existing TwinCAT ecosystem. Of course, TwinCAT PLC++ continues to be based on the languages described in IEC 61131-3. Due to – but not limited to – the advanced compiler technology and the new architecture used, a significant leap in engineering and runtime performance can be achieved.
Beckhoff is consistently pursuing the path of merging automation and IT that it has taken from the outset. Although the company has retained familiar and proven features, it has redeveloped key components of the development environment such as editors and compilers based on IT models. What’s more, Beckhoff has placed particular emphasis on the possibility of using DevOps principles to implement continuous integration and continuous deployment, for instance. In general, there was a particular focus on the specific needs of users. The result: A PLC that is extremely advanced in terms of technology and perfectly tailored to practical requirements.
Performance gains in engineering and runtime
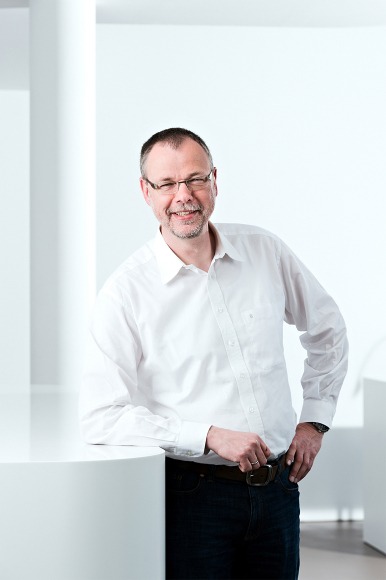
TwinCAT PLC++ offers significant performance advantages in the runtime compared to the previous TwinCAT PLC. With TwinCAT PLC++, the same control code can be executed up to twice as fast as before. As a highlight, the new compiler makes it possible to further optimize this control code in terms of execution time. This option – known from the IT world – leads to a further significant increase in execution speed.
This means that an industrial PC with less computing power may be sufficient for the previous machine control system, thereby reducing hardware costs. If the hardware platform remains unchanged, the freed-up computer resources can be used to implement more control functionality or to increase the productivity of the machine by minimizing cycle times.
Further performance gains can be achieved by combining the product with TwinCAT MC3, the new motion control generation from Beckhoff presented at the SPS 2023 trade show. TwinCAT MC3 features an advanced engineering and runtime architecture. When both TwinCAT basic functions are used together, sophisticated applications and processes can be effectively controlled and monitored, which increases the competitiveness of the customer solution.
From an engineering perspective, TwinCAT PLC++ achieves shorter throughput times all the way from control development and commissioning to the entire machine life cycle. This is achieved by reducing operating times with the help of shorter project loading times and an improved translation process. The minimized project lead times significantly reduce costs and also enable new machines and systems to be launched more quickly.
Increased user-friendliness
Beckhoff was able to incorporate almost 30 years of TwinCAT experience into the development of TwinCAT PLC++. The feedback from over 20,000 TwinCAT users worldwide played a major role in perfecting the implementation, resulting in an optimized, intuitive user interface as well as improved functions that make work easier for users.
Enhanced support for developers is provided by a programming assistant based on TwinCAT Chat, expandable code snippets, smart shortcut functionalities for guided code creation, an online-offline code comparison, and a favorites pool. This allows developers to work even more efficiently than before, thereby shortening the development cycle and reducing time-to-market.
Full IEC conformity and high code quality
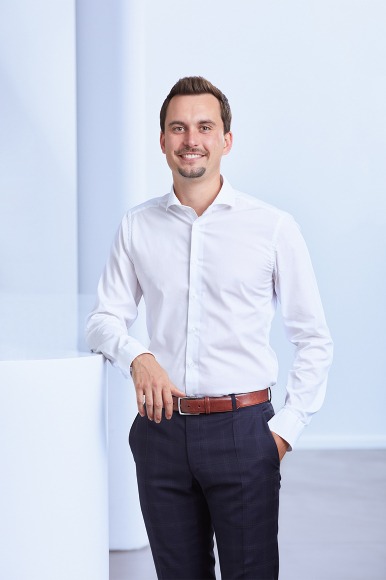
As a member of the German IEC group, Beckhoff has a direct influence on the latest developments and best practices in standardization. TwinCAT PLC++ is almost fully compliant with the fourth edition of IEC 61131-3 and in this way meets the highest international standards. The corresponding portability facilitates exchange and collaboration between different automation systems. In addition, it is possible to use standard-compliant object orientation including classes and access modification for variables, among other things.
Conforming with the IEC standard offers additional safety aspects for programming, which are supplemented by extended type checks in the compiler. TwinCAT PLC++ also supports a secure online change where pointers and references are automatically adjusted. This prevents the implementation of potentially error-prone code and ensures that the application is more reliable and secure. With the help of an emergency mode, it is possible to define explicit responses to an exceptional state of the machine, such as the execution of separate code for a safe shutdown.
Seamless integration into DevOps workflows
With TwinCAT PLC++, the program code is stored in plain text at file level for the first time. This simplifies the use of source code management systems such as Git, as the synchronization of different code versions is particularly easy and intuitive. What’s more, the new compiler is available as a stand-alone component and can be called up automatically via a command line interface. Given that a complete engineering instance is no longer required, this allows automated processes for creating and testing program code in unit tests to be greatly optimized in terms of time.
Therefore, TwinCAT PLC++ offers an excellent foundation for seamlessly integrating PLC code development into DevOps workflows and for checking and ensuring code quality through automated test procedures. Automated tests not only increase the reliability of the control system, but also boost the efficiency of the testing process. As result, products can be launched more quickly and the risk of errors in the field is ultimately reduced.
Assured continuity and compatibility
TwinCAT PLC++ is based on the familiar TwinCAT architecture and is fully integrated into the proven TwinCAT ecosystem. Complete compatibility with the existing TwinCAT Functions is ensured and the new PLC generation can also be used in parallel with the existing TwinCAT PLC if required. The available PLC libraries can also be used to their full extent. On the one hand, this enables a step-by-step changeover with parallel TwinCAT PLC and TwinCAT PLC++ operation. On the other hand, an integrated converter enables the efficient transfer of existing program code, so that existing expertise is easily available in TwinCAT PLC++. For example, existing TwinCAT Scope and TwinCAT HMI applications can continue to be used unchanged. Switching therefore involves little effort.
Integrated deeply into the TwinCAT world
The new TwinCAT PLC++ architecture also enables deeper integration of TwinCAT Functions. For example, TwinCAT HMI and TwinCAT Target Browser can access the PLC variables directly without the program code having to be compiled and executable beforehand. Furthermore, a programming assistant based on TwinCAT Chat can be integrated. This assistant supports the generation of both textual and graphical codes. In this way, the extensive potential of the TwinCAT world can be fully exploited and the efficiency of the entire engineering process can be increased.
In a nutshell, TwinCAT PLC++ is the latest PLC generation available in the TwinCAT system. The runtime and engineering performance is improved, creating significant added value, and the switch is easy to make while preserving current TwinCAT functionality – a real “plus plus” for the user.