Yaskawa iCube Control: Automation Technology That Puts You in Total Control
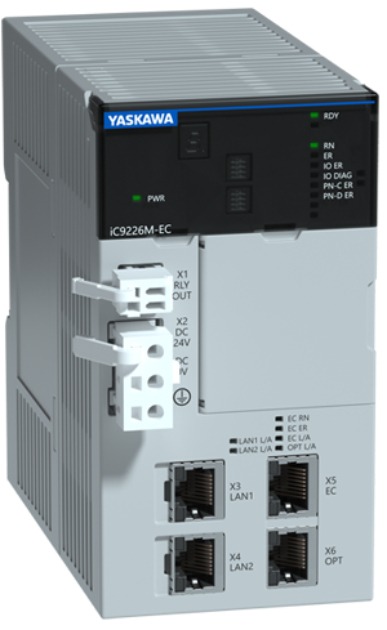
February 3, 2025
Yaskawa iCube Control: Automation Technology That Puts You in Total Control
Yaskawa iCube Control is the open automation machine control technology solution that gives everyone, including engineers, application developers, machine builders and designers, total control over their systems, delivering:
FLEXIBILITY
- Program in IEC61131-3, along with other high-level languages.
- Collaborate securely across teams and geographies.
- Choose from a wide variety of Yaskawa servo technology matched to your application.
SCALABILITY
- One machine controller and one software engineering tool for Motion, Logic, Safety, HMI and Robotics.
- Scale controller features to meet your specific application requirements.
- Easily integrate additional components with open network communications.
CERTAINTY
- Engineered to ensure the highest quality long-term product life cycle.
- Integrated FailSafe over EtherCAT for a complete machine safety solution.
- Secure controller communications and web-based management.
EXPERT SUPPORT
- Expert engineering resources, from design to development.
- Quick, nimble and thorough response, from concept to implementation.
- Delivered by Yaskawa, a global manufacturer of robotics automation systems.
BUILT FOR YOU
Whether you want the flexibility of open system design, the scalability of modular system integration or the certainty of security and safety—you get it all with the iCube Control platform. With one controller, built to perform impeccably over the life of your system.
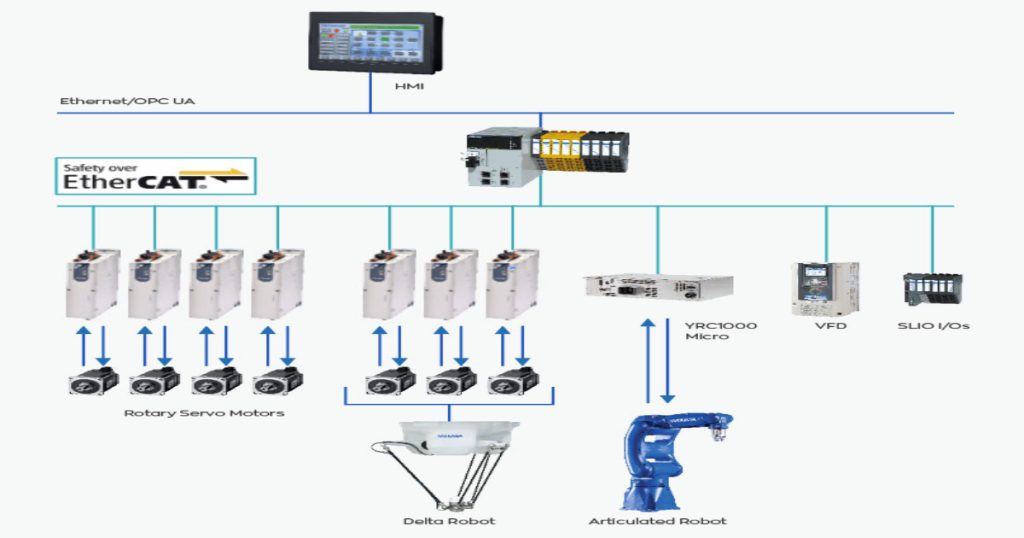
iCube Control is the adaptable, powerful platform that adapts to your personal needs, working methods and ideas. It combines these four separate systems into one:
MACHINE CONTROL
EtherCAT master for all motion control and logic functions.
Program using IEC61131-3 or other high-level languages.
MACHINE SAFETY
Integrated FailSafe over EtherCAT master meeting SIL3 requirements. Program machine control and safety in a single software engineering tool.
ROBOTICS
The Singular Control architecture allows for programming of articulated robots and standard mechanisms with the same PLC open function blocks.
HMI
Integrated HMI development for HMI applications running with remote panels via OPC UA or running locally on the controller via a web server.
iC9226M-EC
EtherCAT Machine Controller
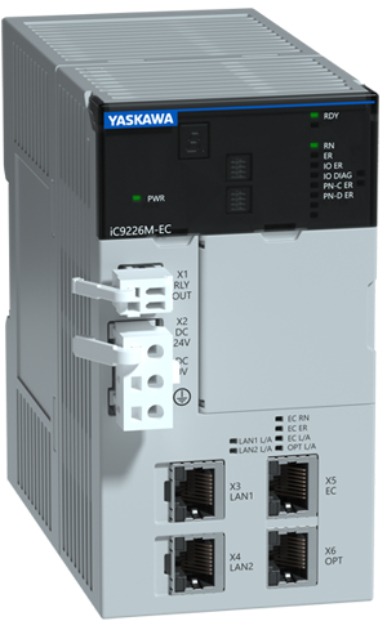
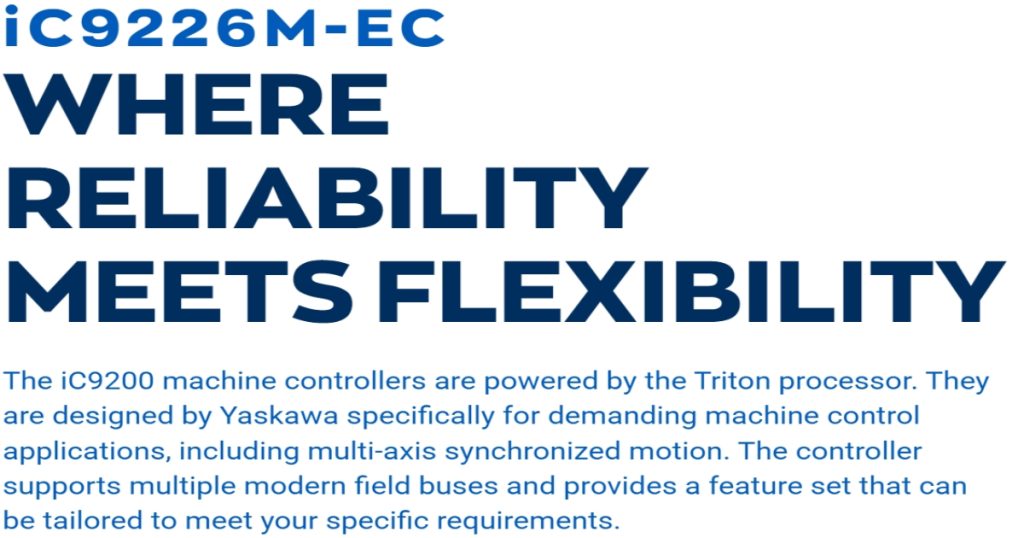

Network Master | EtherCAT (CoE, FoE, EoE) |
---|---|
Fieldbus Support | OPC UA Client, Server, Pub/Sub, EtherNet/IP Scanner and Adapter, PROFINET IO RT, PROFINET I-Device, Modbus TCP Client/Server |
Connections | 2 x Gigabit Ethernet, 2 x 100 Megabit Network, 24 VDC Power Supply (Input), SD Memory Card Slot, Integrated Slice Bus for local SLIO Modules |
Processor | Triton ARM Cortex-A17 1.26 GHz, 3 Core Processor |
Memory | Flash Memory: 4GB eMMC, SDRAM: 2 GB DDR4Program Memory: 12 MB Data Storage Memory: 32 MB Retained Data Storage: 3 MB MRAM |
Synchronized Axis Count | Up to 64 Real and 64 Virtual Axes |
iC9226M-FSoE
EtherCAT Machine Controller & EtherCAT Safety Master (FSoE)
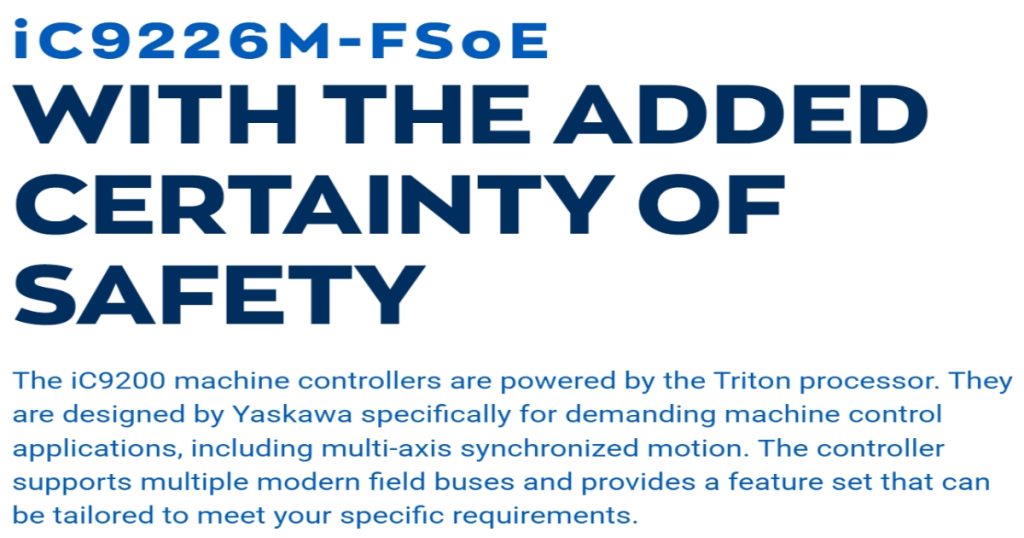
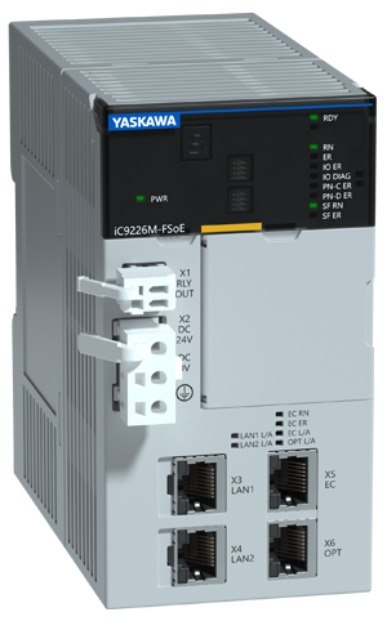

Network Master | EtherCAT (CoE, FoE, EoE)EtherCAT Safety (FSoE) |
---|---|
Fieldbus Support | OPC UA Client, Server, Pub/Sub, EtherNet/IP Scanner and Adapter, PROFINET IO RT, PROFINET I-Device, Modbus TCP Client/Server |
Connections | 2 x Gigabit Ethernet, 2 x 100 Megabit Network, 24 VDC Power Supply (Input), SD Memory Card Slot, Integrated Slice Bus for local SLIO Modules |
Processor | Triton ARM Cortex-A17 1.26 GHz, 3 Core Processor |
Memory | Flash Memory 4GB eMMC, SDRAM 2 GB DDR4, Program Memory: 12 MB, Data Storage Memory: 32 MB, Retained Data Storage: 3 MB MRAM |
Synchronized Axis Count | Up to 64 Real and 64 Virtual Axes |
CONNECTIVITY DESIGNED FOR YOU
YASKAWA TRITON PROCESSOR
- 3 core ARM Cortex-A17 1.26 GHz processor for fast processing of synchronous motion tasks.
- High-speed DDR4 memory and eMMC flash.
- Integrated real-time Ethernet network support.
SAFETY OVER ETHERCAT
- Integrated EtherCAT machine controller and EtherCAT safety master.
- FSoE network safety profile meeting SIL3 requirements.
CONTROL SYSTEM SECURITY
- Secure web-based management with multi-level password protection.
- Secure OPC UA communications.
- Designed for network security certification per ISA/IEC 62443.
NETWORK COMMUNICATIONS
- OPC UA, EtherNet/IP, Modbus TCP, PROFINET, I/O Link.
WORLDWIDE CONNECTIVITY
- Easy web-based access from any Internet-connected location.
- Remotely change settings or update firmware.
REDUCED MAINTENANCE COSTS
- Monitor variables, status, diagnostics and alarms from any web browser.
- Download new programs to the controller without any Yaskawa software.
- Upgrade controller and amplifier firmware.
- Monitor Servo axis position, velocity and torque.
- Live display and setting of I/O values.
FLEXIBLE ACCESS
- Connect via computer or mobile device.
SECURE ACCESS
- HTTPS and password-based user logins with multiple levels of access.